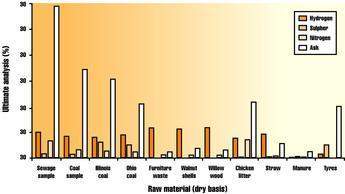
The European Commission enacted in 1996 the Integrated Pollution Prevention and Control (IPPC) Directive, now implemented in law in individual EU countries. The power sector is required to submit applications for IPPC permits for existing plants by March 2006; but new and substantially changed plants coming into operation from now on must apply for licenses before they begin operation.
The UK fossil fuel power generation industry has undergone dramatic change, resulting from both fiscal and legislative pressures through increased competition and increased regulation. These regulations include the New Electricity Trading Arrangements (NETA), the British Electricity Trading and Transmission Arrangements (BETTA) and the Integrated Pollution Prevention and Control (IPPC) Regulations.
Meanwhile, regulations such as the Renewables Obligation Order and amendments to the Climate Change Levy in 2002 introduced new opportunities for coal-fired plants, and a number are taking advantage of the commercial benefits associated with co-firing biomass fuels with coal in an existing coal-fired plant.
There are operational, environmental, financial and legislative implications associated with such co-firing schemes. For example, the introduction of biomass and waste fuels may also introduce toxic chemicals such as dioxins, as well as higher levels of heavy metals.
Environmental drivers
In recent years, the effect of emissions produced by primary energy fuels has received a lot of attention. The CO2 emissions question is set to dominate discussions, but there are other significant radiation-absorbing gases such as methane and nitrous oxide. In addition to the greenhouse effect, there are other processes to consider, resulting from emissions of carbon monoxide, NOx, unburned hydrocarbons and SO2. These result in a number of effects such as the formation of smog, atmospheric reactions and destructive processes that occur in the stratospheric ozone layer.
In addition to these factors, there is, in the UK, the continuing impact of the Climate Change Levy and the increasing importance of achieving accreditation under the Renewables Obligation, both of which can generate significant financial rewards. If operators of coal-fired plants can take advantage of these by converting to co-firing with biomass and waste, both landfill and sewage waste, then they may gain an economic advantage.
Co-firing options
The main argument in favour of implementing a co-firing scheme is that it displaces some of the primary fossil fuel by a biomass or waste fuel. The choice of an alternative fuel requires substantial evaluation of the effects on the overall performance of the plant.
Many of the available emission abatement techniques are “end of pipe” methods, and as such do not offer the optimum solution, namely the removal of the cause of the emission (such as sulphur) in the fuel prior to combustion. There is limited scope for modifying the fuel properties prior to firing due to the costs of pre-treatment involved.
Therefore, any effective abatement technique that can impact on the main fuel prior to firing would be preferable to both the operator and the regulator. In some cases, co-firing biomass with coal causes a reduction in emissions from the composite fuel compared with that of the primary fuel. However, in most cases there is a balance that must be achieved between levels of throughput, the effect on station operation, and a limited reduction in specific emissions.
Co-firing schemes
The introduction of a biomass or waste fuel to a conventional coal-fired boiler is often considered primarily in terms of throughput (coal displacement), generation costs and environmental impact. However, there are many other aspects that have to be considered. For example, the volatility and grindability of the biomass fuel are important characteristics that can dictate the design of the co-firing system.
Co-firing potential
A key requirement of a retrofit co-firing scheme is that it does not impact on the normal operation of the plant. Because the assessment of Best Available Technology (BAT) for a co-firing scheme considers the techniques employed throughout the entire installation, the evaluation of the effect of the co-firing process on all aspects of the station performance is integral to the BAT assessment. The limiting normal operation and accident conditions formed during the safety case also form an integral part of the BAT assessment.
As more experience is gained in the co-firing of biomass and waste in conventional coal boilers, there is a greater need for improved process modelling. Such models specifically for co-firing have entered the market. However, these should be used with care, as individual stations will have specific requirements which cannot easily be incorporated within these commercial packages.
Fuel characterisation
A critical step in the design of a co-firing facility is to evaluate the suitability of the raw material as a fuel component. Table 1 indicates the variability in volatile matter, fixed carbon and ash for various dried sewage sludge samples taken from a number of waste treatment plants.
Any derived composite fuel consisting of a mixture of coal and sewage will have increased variability compared to that of coal alone. It is also clear that the average GCV of a mixed fuel will be significantly lower than that of an average coal sample. This is typically the case for most agricultural based biomass materials and waste fuels. The GCV is important in determining the fuel throughput and heat input to the boiler.
The ratio of fixed carbon to volatile matter gives an indication of how easily a fuel will burn. Typical ratios of fixed carbon to volatile matter on a dry basis are 1 to 2-2.5 for normal power station coals, and lower volatile coals have ratios of 4 and higher. Dried sewage sludge samples produce an average fixed carbon/volatile matter ratio of 0.15 (see Table 2).
The reactivity of dried sewage sludge is low compared to that of coal, and the fuel should burn readily. However, it will do so at a different rate to that of the coal. The effects of this have to be taken into account since the faster burnout of the injected sewage particles may have implications for the operation of different types of low NOx or conventional burners. Heating processes associated with sewage particles occur much more quickly than for coal.
Low NOx burners operate by controlling the oxidation of the volatile nitrogen to NOx by creating a sub-stoichiometric recirculation zone. The volatile nitrogen released in this zone becomes gaseous nitrogen without being oxidised to form NOx. Recent investigations have shown that the higher NOx emissions from sewage sludge in unstaged combustion could be significantly reduced by staging. However, the potential for NOx reduction is not as high with sewage sludge as with other biomass fuels, owing to the higher ash content of the sewage sludge.
A secondary element of fuel characterisation is an analysis of the concentrations of the major elements found in the ash of the fuel. The data can be used to give an indication of the likelihood of the ash to either foul the heat transfer surfaces of the boiler or form slag within the furnace of the boiler.
Finally, the concentrations of the trace elements, including heavy metals found in the ash, are used to determine the impact that the ash might have on environmental emissions.
Process modelling
In evaluating the potential impact of co-firing on a conventional coal-fired power station, the heat rate can be derived from measurements around the power cycle.
As the level of dried sewage sludge is increased, the effect is to reduce the GCV. Figure 1 indicates the effect on overall fuel throughput of increasing the maximum heat input from the sewage, for a constant steam turbine heat rate. Similarly, the effect on the true heat effect attainable in the boiler is shown in Figure 2. In both cases, the effects of several additional potential co-firing fuels are included for comparison.
Fuel handling
The method of biomass or waste fuel preparation and feeding to the boiler tends to be very site specific. However, there are several methods normally considered. The first is to mix the biomass or waste with the coal at an early stage in the process. There tends to be more difficulty with this technique owing to the problems of achieving a homogeneous mixture of coal and biomass, the increased risk of exposing the biomass to further moisture, potential for contaminated run-off, and the effect of the blend on the normal coal feed system.
The increased residence time in an open biomass handling system can lead to health risks and odour control issues. In addition, special consideration is also required during plant shutdowns and periods of plant lay-up. An increase in lag time between the addition of the co-firing fuel and its effect on the system can raise serious issues with regard to control.
A second method is to handle the fuel separately, and pneumatically inject it into the boiler without impacting on normal coal feed operations. This technique depends in part on the form of the biomass fuel during handling. High moisture levels can lead to increased difficulties with regard to pneumatic conveying. The fuel has a greater propensity to clog, requiring larger volumes of conveying air, resulting in lower transport efficiencies.
The composition of the fuel will have a significant effect on the feed system as well as the boiler operation. Higher moisture content will impact on the mill drying capacity, which will also affect the total fuel mass throughput. Any evaluation of co-firing potential must evaluate the affect of moisture levels in terms of fuel feeding and boiler performance.
Pneumatic conveying is generally more expensive than conventional belt-type transport techniques. However, it has many advantages. It avoids the necessity to handle fuels such as dried sewage sludge on their way to the station, into storage vessels and into the boilers, and there is there no exposure of the fuel to the atmosphere. On arrival at the facility, the tankers are weighed at the weighbridge in a similar way to that with coal transportation. The tankers are then pressurised at a dedicated biomass granule “docking” station and the fuel pneumatically transported into storage silos. The biomass granules can be stored and distributed efficiently through the use of specially designed intermediate surge vessels and a novel feed system. Controlled injection at a suitable location is required in order that there is enough time for the biomass to mix with the coal prior to combustion. If a problem does occur, the injection process can be immediately halted by the station control system with minimal coal barring required.
A final and more recently developed method is the gasification of the biomass or waste fuel in order to widen the applicability of the co-firing method to combined cycle power plants as well as a wider range of coal-fired power plants. This is a more recent technique that has the potential for application to a large range of alternative fuels.
Flue gas characteristics and emissions
A comparison of dried sewage sludge and coal samples is shown in Figures 3 and 4. Figure 3 indicates that the dried sewage sludge contains a higher proportion of nitrogen than coal does. This has implications for emission abatement techniques installed at the plant, since the inclusion of sewage will increase the levels of NOx. The levels of sulphur in dried sewage sludge and coal are similar, and thus only a small increase in SOx would be expected.
Another important difference is the increased ash content of sewage compared to that of coal. This has potential consequences for emission of particulates.
The performance of an electrostatic precipitator (ESP) will be affected by a change in resistivity of the fly ash. A layer of dust on the collector plates with an increased resistance will reduce the current flow, and as a consequence, there will be a reduction in collection efficiency. Dust such as silica, which forms a large fraction of fly ash, has a high resistivity, but if its surface is coated with a conductive layer of sulphuric acid, the resistivity of the dust can be reduced. As a result, the sulphur content of the fuel will have an effect on the ash resistivity and ESP performance.
Other constituents of the ash will also influence the ESP efficiency. One of the most important of these is calcium oxide, which tends to absorb the surface acid. Iron oxide can act as a catalyst that assists in converting SO2 to SO3 in the gas stream, and thus has an influence on the surface condition of the ash. The presence of sodium oxide, especially when the sulphur content is low, can enhance the sulphation reaction. In the case of dried sewage sludge and coal, the sulphur content are fairly similar. Therefore, for an ESP, assuming the collection efficiency remains constant, any increase in particulate emissions should be limited.
It is evident from Figure 4 that when comparing hydrogen, sulphur, nitrogen and ash concentrations for various conventional, waste and biomass fuels, the dried sewage sludge is likely to have a higher (other than for chicken litter) nitrogen and sulphur content. In addition, in terms of carbon and oxygen concentrations, the dried sewage sludge has a lower carbon content (sewage 40%, wastes typically 50%) and lower oxygen content (sewage 20%, wood wastes typically 40%). Combined with a significantly higher ash content, it appears to be a limited choice, in terms of composition, for a co-firing application compared with the potential alternative fuels such as wood waste or straw.
Numerical simulation
Numerical simulation techniques such as computational fluid dynamic (CFD) modelling has the ability to evaluate the complex combustion processes associated with co-firing different fuels, and provide information not obtainable by other methods. These types of model are regularly applied to process performance or evaluate design changes. However, a CFD model requires accurate input data (as boundary conditions) which are primarily sourced from laboratory-based analysis, and validation of the numerical solution by data recorded from plant-based trials or measurements. Currently, an evaluation of the impact of co-firing will require a combination of both trials and simulation activities.
BAT appraisal
The Best Available Technology (BAT) assessment methodology is an extremely valuable tool for designers. Where the principles of BAT are incorporated at an early stage within the feasibility and scheme design stages of a co-firing scheme, and where the BAT assessment is used as an integrated design tool, developers will ensure a more robust and sustainable design solution is achieved.
In considering the aspects of a co-firing scheme which are to be taken into account within a BAT assessment, a number of processes resulting from the effect on the station of the characteristics of the fuel composite must be considered including:
- Fuel source. This covers the availability of the fuel, the long-term security of the fuel, the consistency of the fuel characteristics, the distance it must be transported, and the means by which it will be transported, handled and stored.
- Plant efficiency. This covers the calorific value of biomass fuel compared with coal and the moisture levels.
- Thermal balance. This covers the ease of fuel burn, which is based on the ratio of fixed carbon to volatile matter, and the burn rate of biomass fuel compared to conventional fuel, and the consequent impact on burners.
- Flue gas characteristics. This covers the impact on discharges to atmosphere, including NOx, SO2, CO, CO2, particulates, heavy metal, and polycyclic aromatic compounds (PAC).
- System performance. This covers the volatility of biomass fuel and the risk of explosion or fire, the grindability of the fuel and the consequent impact on the mill plant, the fouling of heat transfer surfaces, slagging of the boiler furnace, erosion and corrosion levels, employee handling of biomass during maintenance or repair operations, and fly ash/bottom ash composition and saleability.
- Environmental impact. This covers discharges to atmosphere, water and land.
Financial, operational and environmental weightings can be applied to these parameters to assess the impacts on the installation as a whole, to formulate a co-firing strategy and demonstrate compliance with the BAT principle.
Pilot and plant scale trials
Because of the achievable throughput levels, and since in many cases measurement and sampling techniques are already in place at most stations, pilot scale trials can provide sufficient data to determine the suitability of a station for co-firing. A typical trial will involve the co-firing of 5-20 tonnes of biomass or waste material through a single coal feeder or to a single unit. The biomass or waste material can be supplied to the station by tanker, truck or ship and located in a covered storage area.
One basic method is to supply the fuel in intermediate bulk containment type sacks that individually hold one tonne of material. Using appropriate lifting and handling equipment, the sacks can be opened and, under gravity, feed a supply vessel attached to the coal feeder. A blower system can also be operated in conjunction with the supply vessel to feed the required fuel to the coal feeder. This will then replicate the fuel and air addition from pneumatic conveying relative to that of scaled co-firing operation. Alternatively, the fuel can be stored in a dedicated area of the station and manually added to the coal conveyors.
Larger scale trials have the benefit of providing both performance data and detailed replication of the material storage, handling and operational issues involved in the co-firing process. Such trials can incorporate the design and installation of plant storage, handling and delivery systems. A detailed engineering design and specification programme is required to determine the arrangement of the required equipment. The costs associated with such a design are higher compared with pilot scale trials, but may be offset by the utilisation of the trials equipment in the final co-firing facility.
Tables
Table 1. Analysis of sewage and coal samples
Table 2. Fuel reactivity