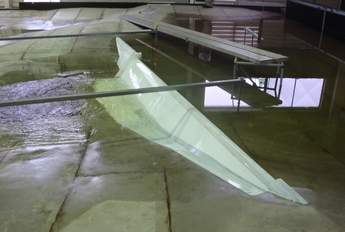
Wyaralong dam site is located in south-east Queensland, Australia, near the township of Beaudesert. The project is part of the south-east Queensland water grid, providing water supply for this region of Australia. When completed, the dam will have the capacity to store approximately 103,000 ML of water.
The Wyaralong Dam Project is being delivered as an Alliance, where the Client, Designer and Contractor work together in a contractual arrangement which shares the risks and the rewards associated with delivering the project. Following the completion of the preliminary design, a value engineering process occurred during the months of February and March 2009 as part of the bidding process chosen by the client, Queensland Water Infrastructure Pty Ltd, to select their Alliance partner. The selected Alliance partners consisted of Macmahon, Wagners, ASI Constructors, Hydro Tasmania Consulting, SMEC and Paul C. Rizzo Associates – which combined with Queensland Water Infrastructure to form the Wyaralong Dam Alliance. The design consultancy services are being provided by Hydro Tasmania Consulting, SMEC and Paul C. Rizzo Associates, while construction is being undertaken by the contracting partners Macmahon, Wagners and ASI Contractors.
Detailed design of the roller compacted concrete gravity dam commenced in May 2009, with initial early works construction starting on site in October 2009 in parallel with the design. Construction is planned to be completed during early 2011. This paper provides some of the details of the dam, along with some reasons behind the final design adopted at Wyaralong.
Dam – General
Wyaralong Dam is a 47m high (above lowest foundation level), 490m long, roller compacted concrete (RCC) dam, with a centrally located ungated primary spillway and a secondary spillway on the left abutment. The total volume of RCC will be approximately 190,000m3. The general arrangement is shown in Figure 1.
The dam has a wet intake tower attached to the upstream face of the dam, located on the right abutment. This intake tower allows water to be drawn from various levels within the reservoir. Water is then discharged back in the river channel through the outlet works at the base of the dam through two submerged, vertical discharge valves.
The dam is also designed to provide fish passage in both the upstream and downstream direction. An innovative bi-directional fish lift is being incorporated to provide this capability.
An aerial view of construction during June 2010 is shown in figure 2. In the photo, RCC placement has started in the spillway section. The upstream side of the dam is on the left side of the photo.
Foundation
The initial geotechnical investigation was carried out in 2006/07 and in the first half of 2009. This investigation consisted of boreholes across the damsite and two dozer trenches were excavated, one on each abutment of the dam. The dozer trenches involved removing soil and overburden and mapping the top of the rock surface. After the initial investigation was complete, 14 additional borings were drilled and the dozer trenches were extended. The geotechnical investigation also included water pressure testing, unconfined compressive strength testing, direct shear testing, and acoustic televiewer surveys.
Geological sections were developed based on the investigations conducted and rock was classified based on the degree of weathering on the sections. Weathering classifications used were distinctly weathered with seams, distinctly weathered without seams, and slightly weathered to fresh. Specific weak layers were also identified on these geologic sections. Based on the geologic sections, the design foundation level for the dam was developed.
The design foundation level was selected to provide a surface that balanced the amount of time and treatment required to prepare the foundation for RCC placement with the amount of rock that would need to be removed and replaced with RCC. The foundation level was chosen so that rock that was classified as ‘distinctly weathered with seams’ was removed from the dam foundation. It was judged that it would take too much time and treatment to prepare this rock to provide a competent base for the dam and it would be removed. Distinctly weathered rock without seams was generally left in place in the foundation because it provides a competent foundation for the dam. The dam is generally founded on distinctly weathered sandstone in the abutments and on slightly weathered to fresh sandstone in the primary spillway section. Photos of foundation preparation at the right and left abutments are shown in figures 3 and 4.
Through the development of the geological sections, the orientation and dip of the typical bedding at the site was identified. The sections also showed that any weak layers identified at the site generally followed bedding. The slope of the foundation at the left abutment is generally consistent with the bedding dip and dip direction, and the right abutment forms a stepped profile.
Using the geologic sections, it was possible to look for potential interpolations of similar weak seams between boreholes in 2D (along sections) and 3D (between sections). Potential planes of weakness were identified between groups of boreholes and surface exposures. A total of eight surfaces of potential weakness were identified at the site, and these surfaces were named surface A-H. Their location relative to the dam is shown in Figure 5.
Stability analyses were undertaken along each of the surfaces identified. Surfaces A and C are located deep below the foundation and were left in place. During construction it was found that surfaces D, E, G, and H were identified at approximately the anticipated locations in the right abutment and spillway section. These surfaces were treated in accordance with the plan developed during design. Surface B was identified in the left abutment, and the foundation in this area was initially blasted to the design level and the presence of Surface B was confirmed. The geometry of Surface B was slightly different from the geometry used in the design, so based on actual survey, additional stability analyses were undertaken. Based on this analysis it was determined that Surface B needed to be removed over the majority of the footprint of the dam. An additional blast was done to remove the rock above Surface B, figure 6 is a photo of the surface after the additional rock removal.
The design also includes a grout curtain to seal potential seepage paths in the foundation. The double line grout curtain is being installed using the GIN method, and grouting is generally being performed from the approved RCC foundation level. In the abutment sections the grout curtain is located in the footprint of the dam and is being done in advance of RCC placement. In the primary spillway section of the dam, grouting is being done from an overbuilt RCC plinth upstream of the heel of the dam, allowing RCC placement to proceed independently of grouting.
River diversion and dewatering
Flows in the Teviot Brook are similar to those in many Australian rivers and streams, where there are periods of low flows, punctuated by high flow events. Taking this flood risk into account, the final diversion arrangement consisted of a 6m high cofferdam which was designed, with reno mattresses, to be overtopped and had a sheetpile cuttoff down to foundation rock through the more permeable alluvial materials in the main river channel.
The river has been diverted into a buried steel conduit for the duration of construction. The diversion pipe consists of a 2.4m diameter steel pipe, which is concrete encased under the foot print of the dam. The capacity of the diversion is approximately 25m3/sec. In the event the cofferdam is overtopped during the first year of construction, various design measures have been adopted to control the flow into the dam excavation area, minimising the clean up and ensuring rapid dewatering.
In addition, a series of dewatering wells are provided to dewater the alluvial material and rock in the foundation area, so as to minimise the ground water inflow into the 15m deep excavation.
Dam section and design
Analyses performed for the dam included static and dynamic stability analyses. Stability analyses were performed along RCC lift joints within the dam, along the RCC/Rock interface, along typical bedding planes in the foundation, and along specific defects identified in the foundation. A finite element model was developed to estimate stresses in the dam during an earthquake, and seismic deformation analyses were performed to estimate displacements during an earthquake.
The dam section was governed by stability analysis along bedding planes and specific defects in the foundation. Shear strength properties for the RCC/Rock interface were developed using the Barton criteria for rough surfaces. Shear strength properties for bedding planes were developed using a combination of the Barton criteria and measured roughness values. Shear strength properties for weak layers in the foundation were developed using direct shear testing. A section with a crest width of six meters and a downstream slope of 0.8H:1.0V was selected based on the analysis. A typical section for the primary spillway shown in Figure 7.
Design features at the dam include a 400mm thick layer of conventional concrete facing, a drainage gallery, crest to gallery drains, foundation drains, and reinforced concrete crest sections. Typical monolith joints in the RCC are located at 30m spacing, with intermediate joints in the facing concrete at 7.5m spacing. The thermal analysis indicates the monolith joint spacing can be adjusted, so the actual location of monolith joints are being adjusted to suit foundation conditions.
Spillway
The spillway at Wyaralong dam is required to pass the probable maximum flood, which has a design inflow of around 7680m3/sec. Various spillway options were investigated during the value-management phase of the project, including combinations of primary, secondary and tertiary spillways located both within the dam section and remote from the main wall.
The adopted arrangement comprises a centrally located, un-gated primary spillway with a smooth downstream face. A 25m wide stilling basin is located at the base of the primary spillway. The design also incorporates a stepped faced secondary spillway on the left abutment of the main wall, which is designed to operate at floods less frequent than the 1 in 100 AEP event. Flows over the secondary spillway are directed along the toe of the secondary spillway in a concrete-lined apron channel to the main stilling basin. For flood events greater than the 1 in 2000 AEP event, the capacity of the secondary spillway apron channel is exceeded and flows spill out across the left abutment towards the river channel.
Extensive investigations were undertaken during the design phase to assess the behaviour of the spillways, with particular attention to the erosion potential of the left abutment for flood events which exceed the secondary spillway apron channel capacity. Two physical model studies were conducted, comprising:
• 1 in 80 scale model of the dam
• 1 in 30 scale model of the primary spillway, used to assess the performance of the fishway, outlet works and stilling basin under low flow events.
The hydraulic models indicated that the spillways and stilling basin perform as intended up to the PMF event. The 1 in 80 scale model is shown in Figure 8.
Results from the model studies for flow over the left abutment for flood events greater than the 1 in 2000 AEP were used in an analysis of the erosion potential of the left abutment. A decision model was developed to assess the acceptability of the design with regard to erosion potential. The decision model took into consideration scour potential based on geological and hydraulic characteristics, likelihood of occurrence, storm duration, and impacts on dam stability if a scour hole develops at the toe of the dam. The conclusion of this assessment was that erosion was judged to be acceptable and the dam will remain stable should a deep scour hole develop.
In order to provide an additional level of protection against scour holes undermining to toe of the dam, a grid of passive anchors were adopted throughout the reinforced concrete apron and stilling basin slabs to ‘stitch’ the concrete slab to the rock and provide additional resistance across rock joints.
An ogee profile was adopted for the crest of the primary spillway with an elliptical curve on the approach to the crest. The secondary spillway crest has been designed as a broad-crested profile, however top forms used in construction of the primary spillway will be reused on the secondary spillway to provide an elliptical curve approach to the crest. Smaller step heights and lengths beyond the secondary spillway have been adopted to provide a transition into the large 1.8m high steps. This arrangement will ensure that flows over the secondary spillway do not pull away from the steps, thus providing improvement in energy dissipation over the steps.
RCC mix design & placement
The proposed mix design is an 85:85kg (cement:fly ash) mix, using sandstone aggregate quarried on site. With specialist advice from Dr Ernie Schrader, this mix was selected as the result of extensive laboratory testing during the design phase of the project. The sandstone aggregate has delivered improved performance due to its stiffness properties, despite presenting some initial challenges for the design team. Early petrographic analyses and tests on the sandstone indicated that it was cemented with clays, potentially of a swelling nature, providing some concerns with the long-term durability and suitability of the aggregate for RCC. Additional petrographic analyses and numerous durability tests were undertaken on cores of sandstone and RCC samples, including wet-dry cycles, soak tests in ethylene glycol, heating and cooling cycles, breakdown tests and abrasion resistance tests. Results indicated that the RCC mix performs remarkably well, with the exception that erosion testing on the samples suggested that a more erosion resistant aggregate is required for the faces of the spillways. Basalt aggregate is being locally imported for use in the conventional concrete facing to address this aspect.
The bulk of the RCC is being placed during night shift over the winter months. Mass gradient and surface gradient thermal analyses indicated that even without forced cooling, the use of sandstone aggregate will minimise the risk of cracking. The main contributing factor to the excellent thermal properties of the RCC is its high tensile strain capacity, which allows the mix to ‘stretch’ more than most concretes without cracking. The mix also has a low modulus of elasticity (~9GPa). The high tensile strain capacity and the low modulus are a direct function of the use of sandstone aggregate.
The RCC is being mixed with an Aran pug mill, capable of producing 400m3 per hour. The RCC is being delivered to the dam site with 40t articulated trucks to enable it to be delivered directly down the left abutment foundation. These trucks have ejector bodies with a spreader box fitted to their rear. The specially designed tail gate sections of the ejector trucks prevent RCC segregation. The delivery from the pug mill to the dam is via a concrete lined ramp, following the secondary spillway apron profile which is at a slope of 1 in 6.
Two trial sections have been constructed for the project, one was constructed with the 85kg:85kg mix and the second test pad was constructed with a 75kg:75kg mix. The first trial section was built to evaluate the water tightness of lift joints and to serve as a practice and training area. The second trial section was constructed to evaluate the RCC mix with less cementitious content.
At the time of writing RCC was being placed in the spillway section of the dam and progressing upward into the abutments. Figure 9 is a photo of the placement area.
Intake works and outlet works
The outlet works are located on the right side of the primary spillway and comprises a wet well rectangular intake tower on the upstream face of the dam with selective withdrawal capacity, a DN 1750mm MSCL main outlet conduit that passes through the base of the dam, and outlet works valve pit at the toe of the dam. Two vertical submerged discharge valves of DN 600mm and DN 1200mm are located in the outlet works valve pit, and discharge directly into the spillway stilling basin. Butterfly guard valves are provided upstream of both discharge valves.
The outlet works and fishway are capable of making regulated releases in accordance with the water resource plan. The largest regulated release flow required is 2.33m3/sec. The outlet and fishway combined has been designed to release 165ML/day with a reservoir level 2.0m above dead storage level. The outlet capacity has also been designed to allow the storage to be drawn down from full supply level to 10% of the storage over a maximum period of 100 days with median inflows.
The 2.8m by 6.6m intake tower will ultimately be attached to the upstream face of the dam with passive anchor bars, however it has been designed to be stable as a free-standing tower during the construction phase to enable its construction to precede the RCC placement. Detaching the construction of the intake tower from the RCC placement has allowed increased flexibility in the construction program.
Fishway
Fish passage was required to be provided as part of the design of the Wyaralong Dam project. The design criteria, options and evaluation of options were developed through a series of workshops, which included all the relevant stakeholders. Due to the extensive operation range for both upstream and downstream fish movement, and due to the fact that the fish density is relatively low in the river, the preferred option adopted was a bi-directional fish lift. With this design a single fish lift is used to provide fish movement in both the upstream and downstream directions. This design has significant operational flexibility. It is envisaged that the fish hopper will be in the upstream attracting position most of the time, attracting fish for downstream fish movement. However, the same attraction flow used for attracting fish in this upstream position will also be attracting fish into the trapped area for moving fish upstream. Extensive hydraulic modelling was undertaken to ensure appropriate attraction flows during all of the design conditions.
Jared Deible, Senior Project Engineer, Paul C. Rizzo Associates, Inc., 500 Penn Center Boulevard, Suite 100, Pittsburgh PA 15235 USA. Jared.Deible@rizzoassoc.com
Richard Herweynen, Principal Dam Consultant, Hydro Tasmania Consulting, 89 Cambridge Park Drive, Cambridge, Tasmania 7170. Richard.Herweynen@hydro.com.au
Colleen Stratford, Dams Consultant, SMEC Australia, 71 Queens Road, Melbourne, VIC 3004. Colleen.Stratford@smec.com