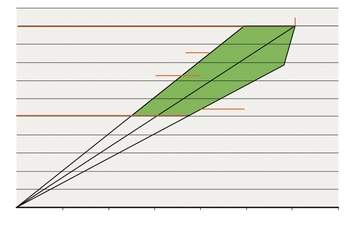
Dalkia France, a subsidiary of Veolia Environnement and EdF, is an r8.6 billion company that focuses on what it describes as energy and environmental optimisation. This translates as provider of energy management services, with a specialist interest in renewable energy solutions, particularly biomass. Nearly 150 of its district heating plants are fuelled by biomass. Of these, Dalkia owns and operates the unit in Pecs, Hungary, which is one of Europe’s largest with an electrical capacity of 50 MW.
Co-generation using biomass as fuel was first employed on a large scale in the Nordic countries in the mid-90s in the pulp and paper industry and in district heating. Metso has supplied ten or more boilers for 80–240 MWe power plants and has recently commissioned or is currently working on several similar boilers for 10–70 MWe power plants in France, Great Britain, Portugal, and Poland.
The Dalkia Facture project
In 2008, Dalkia was selected to build three biomass-fired CHP plants, with a total generation capacity of 122 MWe, amounting to 40 % of the combined 300 MW output of the projects awarded under a tender issued by the French government. The 20-year agreement signed between the parties is part of France’s green energy programme aimed at increasing clean electricity generation, and thus combating climate change.
The largest of the three plants will be built at the site of Smurfit Kappa Cellulose du Pin, one of Europe’s largest paper mills, located in Facture, close to Bordeaux in southwestern France, and is scheduled to start up in October 2010. The bubbling fluidised bed boiler and its auxiliary equipment, ‘from fuel to stack’, that is flue gas cleaning, external fuel handling and plant automation system, will be supplied by Metso (Figure 1). The plant will generate 50 MWe for the national grid and 74 MW of process steam for the neighbouring paper mill. Once completed, the boiler plant, which will use bark and forest residues as its fuel, will be among the largest biomass units in central and western Europe, .
What has turned out to be a fruitful co-operation between Dalkia and Metso started with the conversion of a BFB boiler at the Vilnius district heating plant commissioned in 2006 in Lithuania. This peat- and wood-combusting combined heat and power plant was at the time Dalkia’s largest biomass facility, with a capacity of 60 MWt, and made it possible to sell green electricity at preferential rates.
Metso’s scope of supply includes the HYBEX BFB power boiler with auxiliary equipment, building, electrical equipment and instrumentation, external fuel receiving, storage and conveying systems, as well as an automation and information management system for the whole power plant. Engineering, materials, manufacturing, freight, erection, commissioning, training and start-up assistance for the supplied scope are included, but not the steam turbine plant, balance of plant equipment, and civil works. Dalkia is employing the engineering company Sepoc to manage the overall plant engineering and project co-ordination.
Fuel handling system
A critical part of a biofuel-fired power plant is the fuel handling system. At Facture, the fuel system is designed to receive ready-made wood chips via the receiving bunker, and on-site crushed chips from the fuel preparation plant. The capacity from the receiving bunker is 500 m3/h, the total receiving capacity to storage is 1000 m3/h. The fuel is stored in a covered 15 000 cubic metre A-frame storage facility, which has a reclaiming screw with a capacity of 75–300 m3/h. The traversing screw reclaimer consists of a frame running on rails and a screw with both ends mounted on bearings.
After storage, the fuel goes via the screening station to the boiler silos. There is a second line with a maximum 250 m3/h capacity from the mill’s existing bark storage. The boiler is equipped with two 130 m3 boiler silos and two fuel-feeding lines to assure reliability. From both day silos, located outside the boiler building, there is a single feeding line to the furnace via a chute on each sidewall.
The HYBEX boiler
Histrically, various types of grate-fired boilers have been employed in biomass firing but, as facilities place more emphasis on quality, grate firing has been replaced by fluidised bed combustion. Fluidised bed boilers have a greater tolerance for fuel moisture and type, better efficiency, and lower emission levels. BFB boilers also have the most flexibility in terms of accepting variations in high moisture fuels.
In the BFB furnace, the sand forms a one metre deep bubbling layer on the floor of the furnace. The hot sand effectively dries and vaporises the fuel: the vaporised gases and the fine fuel particles are then burned, mainly above the bed, with secondary air. Only the residual char and larger fuel particles are burned inside the sand bed. The extreme separation of the fuel particles results in very complete combustion, so virtually all the heat energy of the fuel can be utilised, thus maintaining the combustion temperature.
The boiler in this case is designed to generate 47 kg/s of steam at 119 bar and 520°C from feed water at 180°C (Figures 2,3). Its main fuels are paper mill residues (bark, small woodchips, sludge), forest residues (tops, branches, stumps), wood industry residues (bark, sawdust, wood chips), recycled waste wood, and municipal wood residues. Natural gas will be used as a start-up fuel and as an auxiliary fuel in the load burners. The boiler is top-supported, fuel being fed from two silos via feeding lines to four feeding chutes on the sidewalls. Air is supplied as fluidising air below the bed and as secondary air from the front and rear walls and tertiary air from the sidewalls. The superheater has three stages, with the hottest sections made of corrosion-resistant austenitic material. The economiser is made of plain surfaced tubes in three packages. The air heater consists of three packages for primary air and four packages for secondary air.
For NOx reduction, the boiler is designed to be equipped with ammonia solution injection into the furnace, if required in the future.
Hydro beam floor
From the operational point of view, it is essential to keep the bed in good condition. This means that oversize coarse material has to be constantly removed from the bed at intervals. In bed conditions, all sand or other particles bigger than 1.5 mm in size are too heavy to be fluidised. Good fluidisation of the bed is the first requirement for trouble-free operation.
Even though visual evaluation of the fuel can show to some extent whether the fuel is free from incombustible material like sand or gravel, the cumulative amount of impurities fed into the furnace during one day can be significant.
In conventional designs, coarse material was removed from the bed by using separators. The Dalkia Facture boiler is equipped instead with a new Hydro Beam floor, a Metso design of BFB grate specifically made to ensure the effective removal of coarse material. It consists of water-cooled air beams and six coarse material hoppers underneath the beams. This design, with an open space between the beams, provides a region for effective coarse removal that is over 30 times as large as the conventional solution.
Three dry, water-cooled screw conveyors located under the hoppers transport the removed bed material to the screening station, from where good bed material is returned to the furnace and coarse particles are routed to the container.
Flue gas cleaning
In order to control emissions technically and economically, flue gas cleaning solutions must be tailored and optimised for the entire power plant, including its fuel mix. The solutions may include wet or dry flue gas cleaning technologies, or any combination of these. Metso can supply complete flue gas cleaning solutions for air emission control of all kinds of fuels, and for the Facture boiler plant it is supplying a baghouse filter using what it describes as the cutting edge Simatek 3CS technology (Figure 4). The filter consists of four round filter units, each equipped with 400 filter bags. The patented pulse air distributor with its PLC-controlled pulse-jet system differs considerably from other technologies. The bags are cleaned two at a time with precisely the optimum pulsing energy based on a cleaning pressure of 0.3–0.6 bar.
This design delivers low power consumption, so no high pressure air is needed. The cylindrical form of the units results in minimum temperature gradients in the filter chamber and thus a reduced risk of corrosion as well as separation of coarser particles owing to the cyclone effect. The filter is also claimed to work better in humid or aggressive environments, and in the separation of fine, sticky, and hygroscopic dust.
The boiler and flue gas cleaning system are designed so that if in the future the plastic rejects from the mill’s recycled paper were also added to the fuel mixture, the equipment would be ready for it with only minimum modifications.
Process control system
A ‘metsoDNA’ system with advanced controls is being installed for the process control and information management of the entire plant. One of the major features of the boiler automation is its fuel power compensator, which compensates disturbances in the fuel feed to stabilise combustion and steam production. It is based on the estimation of fuel energy input to the boiler. Fast and accurate estimation is produced with a combination of two methods: boiler balance calculation and oxygen consumption calculation. The fuel power compensator adapts the solid fuel feed of the boiler to meet the actual heat demand given by the boiler master controller (steam pressure controller), so the fuel feed to the boiler always matches the master control demand and changes in the fuel quality are compensated before they can be seen in the steam pressure.
The challenges of biomass
The 500 000 tonnes of biomass burned per year, mainly bark and wood residues, will mostly come from the adjacent Smurfit Kappa paper mill and Smurfit Kappa’s forestry service unit. They have a constantly renewing resource in the nearby Aquitaine forest that stretches over an area of more than 1.8 million hectares with an annual yield of 10 m3 per hectare. To make the boiler’s fuel mix more versatile, the boiler has, as mentioned, been equipped with the capability to burn plastic rejects if needed in the future, with only minor changes required.
The combustion of biomass has its challenges. Compared to coal, it has low calorific value and high moisture content which varies through the year and according to the source. These need to be taken into account when dimensioning the boiler for biomass. The ash characteristics also vary greatly depending on the material origin. The ash may cause fouling, bed agglomeration or corrosion. The melted alkali chlorides also cause corrosion in the superheater tubes if the tube material temperature is too high. In the Facture boiler, the secondary and tertiary superheater tubes are of austenitic material and the material temperatures are limited to safe values.