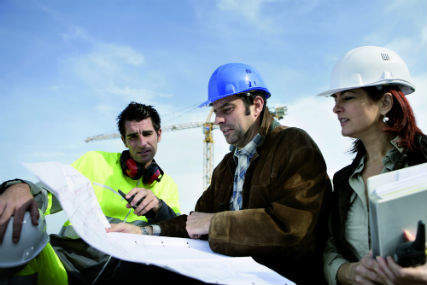
A total of 582 event reports applicable to construction experience were analysed following a survey of three nuclear industry databases:The US Licensee Event Reports (US-LERs); The International Reporting System (IRS) and the OECD/NEA’s Working Group on Regulation for New Reactors (WGRNR).
Many of the events related to management (see also Three decades of NPP construction – Part 1).
Communication
In one event analysed, an inadequate non-safety under voltage/under frequency protection was installed in safety-related equipment because of deficient communication between the plant vendor and the architect-engineer. Another event reports that information about the range of a potentiometer was not given from the testing team to the operating team and, as a result, the output voltage of an emergency diesel generator was lower than expected. Another event report mentioned that openings for equipment ventilation and draining were not installed in 156 terminal block junction boxes as required by the installation specification. The cause of this deviation was the loss of the information about drain openings during communication between the designer and the contractor staff in charge of the installation.
Excellence in communication is necessary to ensure optimal work organization. This concerns verbal communication as well as written documentation (design documentation, installation procedures, test procedures, and so on.). Communication should be done through pre-defined and documented procedures, and submitted to a quality control programme. Moreover, this communication should enable information transfer about the safety significance of components or equipment from the design stage to the contractors and its sub-contractors in charge of the installation of the components or equipment.
Safety culture
Our analysis has showed that the promotion of safety culture, which is a common practice in operating plants, should be ensured from the very beginning of the construction project (that is, before the start of operation of the plant). For this, top management commitment to safety is needed. Each person on the project needs to understand the safety significance of his/her work, to promote personal responsibility.
A significant portion of the reported events gave indications of insufficient safety culture. Many deficiencies revealed that all staffinvolved in the process need to understand the safety significance of their work. This includes the manufacturer’s staff, the vendor’s staff, contractors’ and subcontractors’ staff, the staff in charge of surveillance of activities and the staff in charge of the acceptance of the components. This safety awareness should be given through adequate training, not only for more technically-complex work like welding but even for more simple tasks like anchoring or cable sheathing, especially since sub-contractors may not have experience of working in the nuclear industry.
The following events give examples of consequences of lack of safety culture:
- Partial blockage of emergency core cooling lines by debris from construction stage. Poor level of safety awareness and lack of surveillance of the reactor building sumps during construction allowed workers to throw debris into the sumps.
- Absence of joint treatment between concrete lifts because of lack of preparedness and understanding of the construction code.
- Improper cable sheathing which passed the acceptance stage because personnel in charge of the acceptance procedure were not aware of its safety significance.
Foreign material exclusion policy
Several event reports describe the failure or the potential failure of components due to intrusion of foreign material inside systems: a piece of wood blocked the cooling pipe of a main generator phase, foreign materials (screws, a welding dam) partially blocked fuel channels on different occasions, or were found in a safety injection pipe (plug remaining from the welding operations), a valve failed to close because a loose part was wedged between the disk and the valve body.
These issues emphasize the importance of the application of a foreign material exclusion (FME) policy by all staff present on the site, and its promotion by the management at the plant, from the beginning of the plant construction.
Events have generally been caused either by the absence of sufficient / adequate cleaning and housekeeping (examples of pollution by dust or other construction by-products have been reported), or by the cleaning activity themselves, for example:
- Malfunction of the containment spray pumps due to a screen left in the pump suction after the cleaning operations of the construction stage.
- A valve failed to close because a contactor spring was unintentionally displaced during cleaning activities before start up of the plant.
Management of quality
Licensee management needs to be committed to the implementation of the quality management system and to communicate clearly on the expectations and requirements of the quality management. A significant part of the event reports describes as a root cause a deficiency in the quality process: improper quality assurance at the construction site or in the manufacturing facility, improper surveillance or quality control, improper independent verification, and so on.
A related area is adequate management of non-conformances. In one event, a non-conformity report was issued by the civil work contractor about missing steel reinforcement. One week later, the non-conformity report was closed even though the steel reinforcement was still missing. The surveillance carried out by the licensee at that time did not detect the lack of corrective action for this non-conformity. A couple of days later, a licensee inspector again detected the missing steel reinforcement and asked the contractor to correct the non-conformity. When the licensee’s inspectors’ shift changed some hours later, the information was lost and the concrete was poured in spite of the missing steel reinforcement. This is one event among others where a clear and fully- observed process of management of non-conformances (with adequate definition of roles and responsibilities, adequate documentation and assessment) could have contributed to avoid the event.
Any changes from the initial design, installation or manufacturer procedures should be properly analyzed and documented. Several events demonstrated the consequences of not following such a policy:
- Improper wiring remained uncorrected for years even when detected during the commissioning because, on the vendor’s advice, operating documents were modified to fit the installed wiring without any safety analysis.
- Important safety-significant valves on the containment spray system were found locked closed since the initial start-up of the plant. Visual inspection did not reveal this mistake because they were relying on the stems’ position and those stems were not configured according to design and gave therefore an incorrect indication. In this case as well, the design change was not documented by the valve manufacturer.
There is a need for adequate quality assurance and quality control for the packaging, transport and storage conditions of safety-significant components.
Management of project tasks
During the construction of an NPP unit, task management is particularly complex. Many tasks are correlated and linked to the completion of others, which requires clear divisions of the responsibilities of each party involved.
For example, one event report mentions that the electrical penetration assemblies connected to the containment radiation monitors were not installed with protective heat-shrink moisture seals. This configuration would not ensure post-accident operability. This deficiency was mainly caused by the lack of clear definition of responsibilities between the radiation monitor vendor and the contractor in charge of the corresponding containment penetrations.
Management of temporary devices
Many events are related to deficiencies or failures due to temporary devices used for manufacturing, construction or commissioning of the plant. Some of these temporary devices led to the undetected inoperability of safety systems for years. The number and significance of the reported events show the need for a reliable, separate programme of management of temporary devices. For example:
- A remaining blank flange was forgotten and found later downstream a tank safety valve, in an untested line
- Temporary manufacturing latches or temporary lever for diagnostic checks which were forgotten in breakers and prevented the breakers’ movement, which could have challenged the breakers’ behaviour in case of earthquake
- Cracks in steam generators’ shells developed from welded mounting devices which were removed without any proper documentation.
- The discovery of polystyrene inside the reactor building remaining from the construction stage when it was installed to act as a forming material to prevent the original pouring of concrete for the in-core pit/letdown cooler structure wall from coming into contact with the reactor building liner. During some accident scenarios, it could have melted and been transported to the reactor building sump, leading to the potential clogging of the recirculation sumps.
Management of sub-contractors
The construction of a NPP unit generally involves a huge number of different suppliers, contractors and sub-contractors. This brings additional difficulties for project management.
As an example of this, two recent construction issues can be underlined: a deviation in the concrete composition and missing stirrups in concrete steel reinforcement. The first issue emphasizes the lack of clear distribution of responsibility for the quality control of the sub-contractors, as well as lack of safety understanding and lack of quality control. One possible solution is oversight by a third party, independent from the licensee and the company in charge of the works. This solution seems interesting as the licensee may have no experience of the works under completion. It would of course avoid any potential conflict of interest as well.
Conclusions
During construction, manufacturing and commissioning of a new reactor, deficiencies can become major latent failures over a long time and can have actual consequences on safety when the reactors starts to operate. The study has emphasized the necessity to reduce the incidence of these as much as possible. It has showed also that special attention should be paid to management and organizational issues in addition to the attention given to purely technical tasks.
Marc Noël and Benoit Zerger, European Clearinghouse on Operational Experience Feedback for Nuclear Power Plants, Institute for Energy and Transport, Joint Research Centre, European Commission, P.O. Box 2, 1755 ZG Petten, The Netherlands.
The work in this paper is based partly on research previously reported in ‘European Clearinghouse: Analysis of Construction and Commissioning Events – Topical Report (2010)’, European Commission, Joint Research Centre, Institute for Energy, Petten, Netherlands.