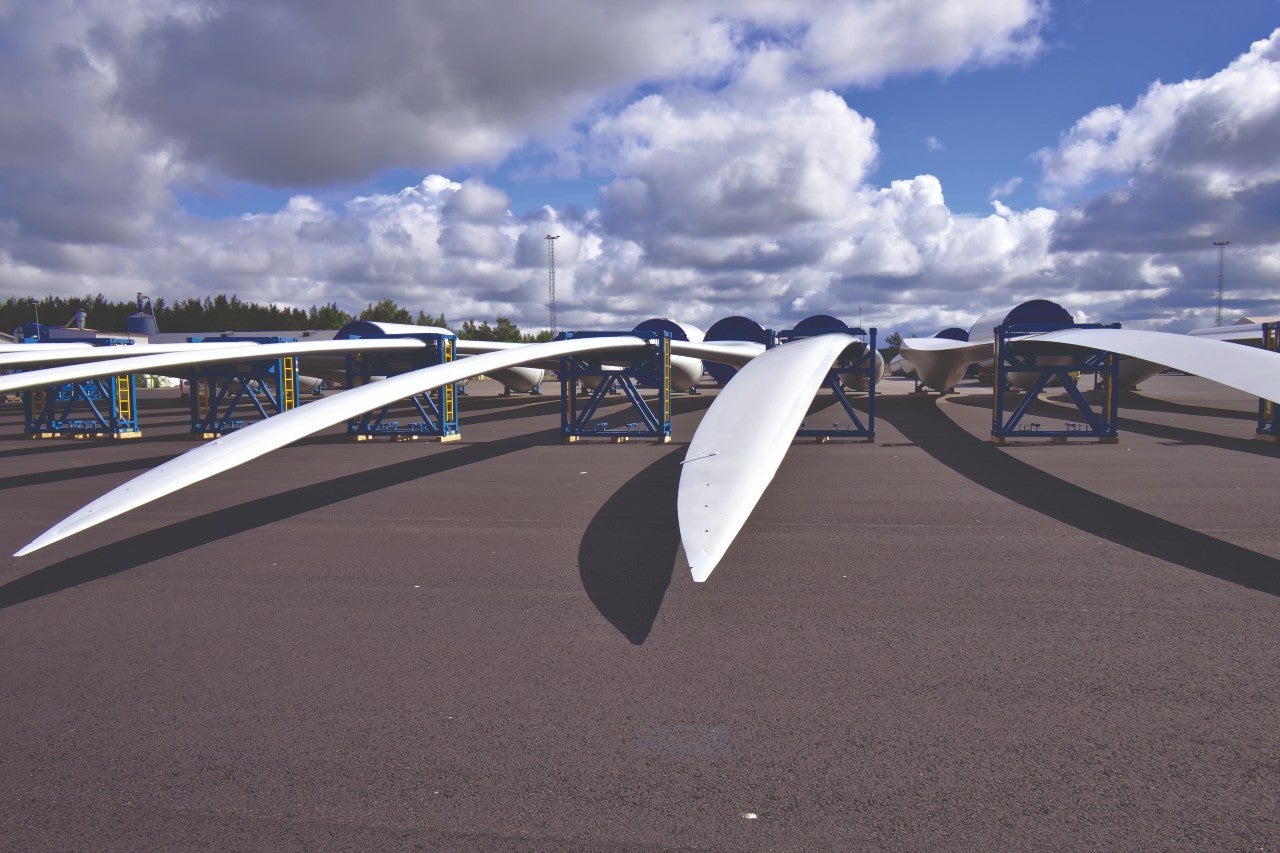
From starting 2020 on a high, the wind industry has – inevitably – found itself scrambling to adjust to Covid-19 and all its consequences over the past 18 months. And from disrupted supply chains and delayed projects, there’s certainly plenty to chew on – even if, over the long term, the industry’s future still looks cheery. Andrea Valentino chats to Ken Kaser and Steve Dayney from Siemens Gamesa, and Shashi Barla, a Wood Mackenzie analyst, about how the wind industry has fared in the age of Covid, what that has meant for industry supply chains and how its geographical make-up might change.
It was all going so well. Glance at industry reports in the months before Covid-19, before anyone had heard of lockdowns or herd immunity or furloughs, and you’d have thought that wind energy was in for a bumper year. As work by Mordor Intelligence noted at the tail end of 2020, the industry was expected to grow by 7.9% every year to 2025 – optimism equalled if not surpassed by insiders themselves. Writing for S&P Global in December 2019, one analyst wrote of “swelling” wind pipelines, with another specialist in January 2020 boasting that, in the US alone, three-quarters of this year’s new generating capacity would be renewable.
Nor were these predictions merely wishful thinking. On a warming planet – and one where wind energy enjoys 20% more efficiency than green alternatives like solar – it’s no wonder that investment in wind energy quadrupled over the first half of this year. The irony, of course, is that, right now, all this enthusiasm risks going nowhere. With the international economy struggling to recover, and strict restrictions still in place, this most global of industries has struggled to get its supply chain in order since early 2020 – with many projects delayed or postponed.
Even so, the situation is far from hopeless. With so much at stake, for their account books if not the planet, it’s no wonder that companies have been eager to shift to the new post-pandemic reality, tweaking some elements of their supply chains and reforming others. Whatever turbine operators and their suppliers are doing, though, one point seems certain: the traditional wind power supply chains that existed before the pandemic are probably gone forever – with significant implications for the industry at large.
Delicate operation
How are wind turbines built? The answer: carefully. Even a single wind turbine, let alone a whole farm, is a monumental feat of engineering – one requiring seamless collaboration between businesses, hauliers and officials across hundreds or thousands of miles. “A robust supply chain is critical to deliver the right products at the right cost level at the right time,” says Ken Kaser, senior vice-president of operations for Siemens Gamesa’s Offshore Business Unit. “The massive sizes of offshore wind turbines and high cost-of-entry into the industry require solid, reliable suppliers.”
Shashi Barla, an analyst at Wood Mackenzie, makes a similar point. With the turbines themselves absorbing the majority of the total cost of a new farm, he explains that it’s vital for stakeholders to get a good deal on logistics. That’s especially true, he adds, when it comes to economies of scale. “To reduce costs, companies are launching bigger turbines,” he says, something that would be impossible without delivery efficiencies and timely arrivals. Certainly, the statistics seem to support him. According to a Wood Mackenzie study last year, for instance, global wind power supply chains are expected to generate up to $600bn of revenue every year between now and 2028, a total uptick of over 35%.
An impressive figure, yet also one that starts to explain why the industry has had so much trouble of late. With facilities stretched across continents, and impressive growth in emerging economies like China and India, wind energy logistics is big business. But that same global reach can quickly collapse the moment borders begin to close. Consider Kaser and his colleagues at Siemens Gamesa. With factories in Denmark, England and Germany, and plans to open new sites in France and Taiwan, a lockdown in just one of those spots can bring the whole supply chain to a grinding halt, something Kaser admits “created challenges” early on in the pandemic.
There are more specific challenges too. Even before the pandemic struck, there was a shortage of certain critical turbine components, including the roller bearings that connect to their gearboxes and, ultimately, allow the turbines to keep spinning. That naturally puts manufacturers and operators in a tricky position – especially, Barla adds, given that the trend has been to make bigger turbines, needing more and more parts. Work by the US Energy Information Administration, for its part, suggests that these problems are affecting the completion of new turbines in the field, with 1.2GW of wind turbine projects “citing the pandemic’s mitigation factors as a cause for delays”.
Time on wind power supply chains is time well spent
Between planning and construction, battles with regulators and fending off angry residents, it takes about seven years for a new wind farm to actually start spinning. That may be frustrating under normal circumstances, but these time lags have actually proved incredibly useful over recent months. “Given the long project times we work with in offshore wind,” Kaser explains, “we are accustomed to thinking ahead and mitigating long-term risks. The same sound fundamental planning and risk-management practices required for successful projects benefitted us in these Covid-19 times.” Indeed, Kaser adds, though there were challenges early on, no Gamesa deliveries have been affected by the pandemic so far.
Not that Siemens Gamesa has quite been able to carry on as normal. Like every company on earth, big or small, it’s had to change how it does business. That includes boosting cleaning in factories and encouraging staff to work at home, even if Kaser notes that “keeping cohesion” among teams scattered in different neighbourhoods can be tough too. When it comes to supply chains in particular, meanwhile, equipment manufacturers have looked to diversify their options. As Barla notes, that’s especially true in the onshore market – for turbines destined far from shore, there are fewer options. All the same, companies are looking further afield for the technology they need, with South East Asian countries such as Malaysia and Thailand primed to build more extensive power units and semiconductors.

More broadly, manufacturers and operators are reexamining the human side of the supply chain too. Though we tend to think of the field as a purely technical one – getting springs and motors and blades from place to place – what happens if your flesh-and-blood engineers are locked down at home? Once again, Kaser suggests, his team can borrow from earlier experiences, particularly when it comes to remote monitoring of sites. “Siemens Gamesa has had advanced remote monitoring for many years,” he says, explaining that globally his company monitors over 10,000 turbines every single day. And given 85% of faults can be fixed remotely, this puts the company in a strong position – whether future lockdowns prevent staff from travelling to a site, or if social distancing rules preclude them from sitting on a cramped maintenance vessel.
If the competition is even half as organised as Siemens Gamesa, in other words, it seems clear that the wind industry isn’t quite as lost as you might imagine. Not that intrepid executives such as Kaser can do everything alone. As his colleague Steve Dayney – the North American head of offshore – says, cooperation with national and local governments has been instrumental in surviving the past year relatively unscathed. Getting the industry back on its feet certainly required a strong collaboration across the board. “Whether in China, India, Germany or Morocco, we have relied on their guidelines for health and safety to help us keep our employees safe,” Dayney says. The same is true in the US, Dayney adds, explaining that from slashed red tape to new port infrastructure, “We appreciate the support of the [government] on its efforts to simplify and streamline the development of major projects.”
The world keeps spinning
What, then, for the future of the wind energy supply chain? Given how well his company’s fared so far, Dayney is unsurprisingly upbeat, especially when it comes to growth. “Siemens Gamesa is ready for the US offshore market, and we see a significant construction market developing from 2022 onward, and we plan to use our unparalleled experience to make it a success.”
Shashi Barla makes a similar point, suggesting that companies are busy expanding their wind power supply chains in anticipation of future pandemics. “Companies are expanding the offshore supply chain into new geographies. To a certain extent, Covid-19 is a blessing in disguise, as they are forced to switch up the supply chain.”
Beyond where they procure components, meanwhile, Kaser wonders if the shocks of the past year will push companies to keep more in stock, just in case disaster strikes again. “On the inventory side, we believe that many industries in general may now need to rethink their approach to keeping minimal stock on hand and relying on just-in-time deliveries. The crisis has driven the risks of this way of operating home.”
One would hope that the wind industry would absorb these lessons sooner than most. With so many jobs on the line – to say nothing of the future of the planet at large – it would be a pity if the optimists were knocked back yet again.
This article first appeared in Issue 1, 2021 of World Wind Technology.