
Dual Fluid was originally a German nuclear technology start-up, but it decided to become Canadian, and was incorporated as a public company in Vancouver in 2021 to better position it to benefit from Canada’s favourable disposition towards SMR development.
“The Canadian government promotes SMRs as a technology of the future,” says Dual Fluid, “while the population predominantly sees nuclear power as an opportunity.” Also, “the country is experienced in nuclear technology and, unlike Germany, can look back on uninterrupted expertise” and “last but not least, there is an internationally recognised nuclear licensing authority.”
LWRs: an inadequate technology
The light water reactors commonly used worldwide are inefficient, they can only convert about 1% of the natural uranium produced into electricity, argues Dual Fluid. In addition, the nuclear fuel is burned at low temperature, which makes “interesting chemical applications” impossible.
How did this inadequate technology prevail over more promising designs that existed in the middle of the last century? The answer is found in its military advantages, argues Dual Fluid: reactors with fuel rods are well suited to powering submarines, plus they can provide plutonium for nuclear weapons in an uncomplicated way. Other concepts that were known to be more suitable for civilian use were dropped. The fact that we are still using the same LWR technology several decades on is attributable to the immense energy density of the fuel: it provides so much energy that even inefficient nuclear power plants are profitable.
Of the early designs that were not developed commercially, two stand out: one with liquid fuel; one with liquid lead cooling. In the 1960s, the USA successfully operated an experimental reactor with liquid fuel (molten salt reactor) that was able to make better use of the fuel. However, since the fuel salt also transferred the heat, the power density was limited because the two functions are difficult to reconcile. Russia built a reactor with high-performance liquid lead cooling in the 1970s for its submarine fleet. But these reactors used fuel rods, making fuel supply and recycling difficult.
The Dual Fluid concept is a fast reactor that aims to combine the advantages of the molten salt reactor with those of a lead cooled reactor in a completely new design.
The key innovation of Dual Fluid, as the name suggests, lies in using two liquids in the reactor core. There, liquid fuel can develop its full power, at around 1000°C (compared with 320°C for a typical LWR), while liquid lead handles the heat transfer.
High power density
The principle is completely new in nuclear technology, says Dual Fluid. The decisive advantage is the high power density, which is due to the compactness of the system and the high operating temperature.
The fuel can circulate as slowly as required for an optimum burn-up rate, while the coolant can circulate as fast as required for optimum heat removal. As a result, undiluted liquid fuel – a metallic actinide mixture – can be used, significantly increasing the amount of fissile material in the reactor core. The compactness of the core reduces the amount of structural materials required, which allows the use of expensive, high-temperature and corrosion-resistant materials.
Liquid lead as a coolant dissipates the heat without slowing down the neutrons in the reactor core.
High power density goes hand in hand with high efficiency: a small Dual Fluid core rated at 300 MWe is eight to ten times more efficient than current LWRs. With larger cores, power density and efficiency increase further.
Because Dual Fluid, as a fast reactor, operates with a high neutron excess, the reactor – in combination with the Dual Fluid recycling plant – can fully utilise any fissile material, including thorium, natural uranium, and nuclear waste from current reactors.
Nuclear power redefined
The principle of separate cycles for fuel and coolant “completely redefines nuclear power”, Dual Fluid believes. In combination with the Dual Fluid recycling plant, all the fuel loaded is used productively, without the need for a final repository.
Application of the Dual Fluid principle is not confined to SMRs, but the first realisation of the concept is expected to be a small modular reactor, rated at about 300 MWe, the DF300.

In the DF300 modular power plant, the fuel is delivered to the power plant in a sealed cartridge. There it is heated and pumped in liquid form into the reactor core, where it produces heat for around 25 years. The spent fuel is then returned to the cartridge and transported for recycling.
Larger cores, such as in the DF1500 power plant, – 1500 MWe/3000 MWt – have a higher fuel throughput and can be combined directly with a Dual Fluid recycling system. This enables permanent fuel processing on site.
The Dual Fluid recycling process differs fundamentally from ‘conventional’ fuel reprocessing based on PUREX wet chemistry. In the Dual Fluid recycling plant, the spent fuel is first converted into liquid salt form and then separated into its components using a distillation process that is already established outside the nuclear industry. All fissionable materials are then mixed with fresh fuel and returned to the reactor core.
This recycling method, based on pyrochemical distillation, enables the complete utilisation of any fissionable material, achieving, for the first time, a truly circular economy in the nuclear fuel chain, says Dual Fluid.
In addition to electricity generation, the DF1500 power plant, with its 3000 MWt of heat, is particularly suitable for energy-intensive heat applications such as the production of hydrogen and synthetic fuels. “Green” hydrogen production today involves high energy losses, whereas a strong nuclear heat source opens up the possibility of high temperature steam electrolysis (HTE), which is more efficient than current processes. Hydrogen production via HTE could undercut the current cost of green hydrogen from wind power many times over and is estimated to be cost-competitive with methane steam reforming, Dual Fluid estimates.
Energy return on investment
The energy return on investment (EROI) for a power plant is the ratio of the energy gained to the total amount of energy expended over the complete life cycle (including construction, operation, fuel, decommissioning):
EROI = Eout / Ein
Fossil fuelled power plants achieve an energy return of around 30. Solar and wind, including storage, achieve single-digit numbers.
While an energy return of 30 made the industrial revolution possible and is still sufficient to supply an industrial country today, a return to less efficient technologies could amount to a step backwards, Dual Fuel argues: energy will become more scarce and increasingly expensive, potentially leading to declining standards of living.
Modern, people- and nature-friendly, societies must aim to provide reliable energy in large quantities for little money and with a small ecological footprint, Dual Fluid believes, and “a high energy density fuel can achieve that.”
Today’s light-water reactors have an energy return of around 100, which means that they outperform fossil-fuelled power plants by a factor of three. But what sounds good actually indicates underperformance – because nuclear fission releases not three times, but millions of times more energy than a fossil combustion process, Dual Fluid points out.
Why does today’s nuclear power fall so far short of its potential?
A look at the energy expenditure involved in a typical LWR shows that 80% of it is accounted for by the provision and disposal of the fuel – ie, mining and refining of the uranium as well as the production, recycling and disposal of the fuel elements. This is high because today’s reactors can only turn a negligible proportion of the mined uranium (around 1%) into useful energy. The rest of it, mostly mixed with fission products, must be disposed of as nuclear waste.

Power generation with today’s LWRs is, therefore, not a high-yield system. High investment costs and regulatory requirements completely offset the energy advantage over fossil-fired power plants. On the whole, the potential of nuclear fission remains mostly unused, Dual Fluid argues.
A new generation of reactors (“Generation IV”) may achieve gradual but not fundamental increases in efficiency. This is because either the concept of fuel rods is maintained, or the concepts build on older liquid-salt reactor designs. In the latter, the same liquid both carries the fuel and provides heat removal, leading to suboptimal results for both functions. (Moltex Energy’s design is an exception to this. It opts for liquid fuel contained in solid fuel rods.)
The Dual Fluid reactor design — which its developers describe as “Generation V” – with concentrated liquid fuel and lead cooling, combined with the recycling of the fuel, reduces the energy expenditures related to the fuel to a fraction. Further efficiency gains result, as already noted, from the relative compactness of the system, due to the high power density.

Overall, the energy expenditure for a DF300 power plant drops to a tenth of that for a typical LWR, and this inevitably lowers costs.
The energy return increases, depending on the size of the reactor, to 800-1000 for the DF300 and around 2000 for the DF1500.
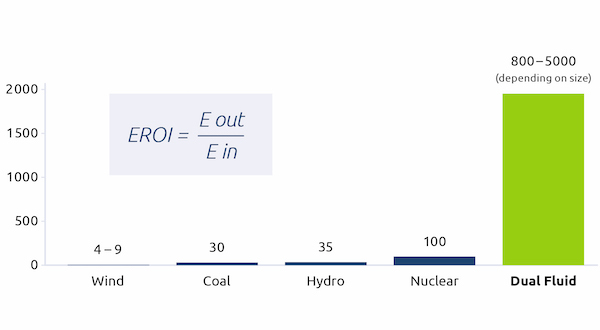
Material issues
The material separating the two fluids of the Dual Fluid reactor must have sufficient thermal conductivity and corrosion resistance, both for lead and for the fuel, which is a molten liquid metal. Compared to the conditions in thermal reactors, there is a wide choice of materials for the structural wall mainly because of the low neutron capture cross sections for fast neutrons. Materials that are suitable in principle have in fact existed for decades, but they contain rarer and more expensive chemical elements. This may be a problem for conventional reactor technology and for modern molten salt concepts since they require large quantities of structural materials due to relatively low power density. This does not apply to Dual Fluid and the entire spectrum of modern industrial materials can be used, the company says, noting that even noble metals can be used as components of the alloys with little impact on the overall cost of the system.
Examples of such materials are the alloys of refractory metals or highly corrosion resistant ceramics such as silicon, titanium or zirconium carbide, which have been increasingly used in industry in recent decades for applications under extreme conditions. In addition, coatings with substances such as yttrium oxide, which is resistant to pure uranium up to 1500°C, are also possible. Since the temperatures in the reactor core are significantly lower than this, and moreover the fuel does not consist of pure uranium but of a uranium-chromium mixture, the identification of the most suitable material represents a “solvable development task”, says Dual Fluid.
Safety features
The most important safety feature of Dual Fluid is the reactor´s instantaneous self-regulation, made possible by the very negative temperature coefficient. If the temperature increases, the nuclear fuel expands. As a result, the reactivity immediately subsides and the temperature drops.
The reactor is thus completely self-regulating; a power excursion such as that which occurred at Chernobyl is ruled out.
If the system nevertheless heats up beyond the normal operating temperature – “conceivable only due to incorrect fuel composition” – melting fuse plugs provide additional protection.

The fuse plug is an actively cooled section of the fuel line near the lowest point. The fuel is actively cooled there from the outside, so that it freezes locally and closes the downstream outlet. If the fuel overheats, the frozen fuel plug melts and the liquid drains downward (due to gravity) into subcritical tanks. The chain reaction stops immediately and the decay heat is removed purely passively (ruling out accidents where decay heat is not removed (eg, Fukushima)).
This simple control system concept cannot be compromised and has already proven its worth in the US molten salt reactor experiment of the sixties, Dual Fluid observes.
For effective protection against violent impact and earthquakes, the nuclear part of the plant would be located underground in a thick-walled bunker. Even in the worst possible accident scenario – a leak associated with the fuel cycle – no radioactive material would escape to the outside, since there is no significant pressure and nothing could explode.
Route to serial production
Following around ten years of groundwork done principally at the Institute for Solid-State Nuclear Physics, Berlin, the Dual Fluid technology is estimated to be at TRL3. The next step is component testing.

Academic partners are pursuing analyses of the stability of the system as a basis for licensing.
The seed funding round was successfully completed in June 2021.
If everything goes to plan, the hope is to produce a prototype within a decade and start series production soon after.
This article first appeared in Modern Power Systems magazine.