
E-fuels such as ammonia and methanol are derived from hydrogen or syngas generated by electrolysis. When the electricity flowing to the electrolyser is from renewable sources such as hydropower or PV solar power, the e-fuels are regarded as renewable, or green.
The first MW-scale green ammonia project was implemented in 1928 in Norway. The Rjukan facility started up in 1928 with 165 MW of power flowing to 150 electrolyser modules generating 27 900 Nm3/h of green hydrogen.
At a similar scale, also using Norwegian hydropower, Glomfjord commenced in 1949. Both schemes used atmospheric pressure and alkaline electrolysis. The hydrogen was converted to ammonia to produce ammonium nitrate, a fertiliser.
In a similar setup to the two Norwegian projects, hydropower from the Aswan dam was used to generate green hydrogen. One facility was built using Demag electrolysers in 1959. It had a total of 203 MW capacity of atmospheric pressure alkaline electrolysers across 288 modules generating 36 000 Nm3/h of hydrogen.
A slightly smaller system was implemented using equipment from BBC Electrolyzer System Oerlikon in 1973. As with the case in Norway, the goal was to make ammonia for fertilisers to increase the yield of local food production.
The revival of green ammonia in the 2020s
Looking to the more recent past, for several years now, attention has focused on green hydrogen as a clean energy vector. The motivation to produce green ammonia from green hydrogen includes the historic reason: the production of nitrogen fertilisers. But the demand for green ammonia and e-fuels will grow as they are increasingly recognised as being cost-effective ways of transporting green energy over long distances.
Conversion of hydrogen to ammonia or e-methanol adds cost at the production location but means that energy-dense liquid ammonia or liquid methanol can be shipped to the end-user location. These fuels are more cost-effective to ship long distances than hydrogen which has a comparatively low volumetric energy density as a compressed gas or liquid.
Ammonia is easily liquefied and has a volumetric energy density about 50% higher than liquid hydrogen. The savings in shipping costs of liquid ammonia, compared to liquid hydrogen, mean that capex and opex savings from the shipping operation can be routed to the ammonia synthesis facility.
One of the attractions of using ammonia as a tradeable energy vector is that it is already a globally produced and traded commodity. Worldwide grey ammonia production is currently around 185 million tonnes per year.
The global merchant market for traded grey ammonia is circa 20 million tonnes per year. 170 ammonia tankers sail the world’s oceans shipping these merchant ammonia volumes across 120 portside ammonia terminals. A typical ammonia tanker can transport 60 000 tonnes of liquid ammonia and a terminal would typically be built to store twice this capacity.
The maturity of the ammonia transportation infrastructure is an attractive reason for considering the use of green ammonia as a traded energy vector. Similar statements could be made in connection with methanol.
Merchant grey ammonia pricing has been influenced by natural gas costs and supply vs demand balance. The pricing volatility of grey hydrogen and the lack of availability of excess capacity for international trade are key drivers for the development of green ammonia to supplement existing grey ammonia production.
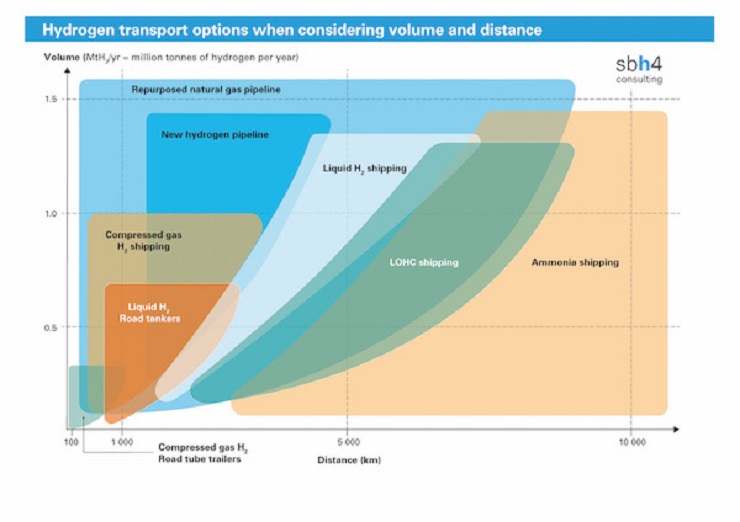
Ocean trade
The concept of shipping green hydrogen into the oceans will become a reality in several major international projects. Within Europe, green hydrogen will be converted to green ammonia in Portugal and shipped to the port of Rotterdam in the Madoqua Power2X project, based in Sines on the western coast of Portugal.
The core of the Madoqua Power2X project will be renewable wind and solar power generation flowing into 500 MW of electrolyser capacity. This €1 billion investment will be capable of producing enough green hydrogen to generate 500 000 tonnes per year of green ammonia.
Receiving terminals, such as the new ACE ammonia terminal in the Port of Rotterdam are being planned to receive the shipments. ACE lies in 16.5m of water depth in a location where 400 m long ships regularly sail and berth.
An intercontinental green ammonia supply chain will also be established from western Australia to Germany. The German LNG terminal at Brunsbüttel, on the North Sea at the western end of the Kiel canal in northern Germany, has recently announced plans to incorporate a world-scale ammonia storage tank in the terminal scheme in addition to the two previously planned LNG storage tanks.
The shipping cost for liquid ammonia over Australia to Germany route is only circa 3% of the total landed cost in Germany. By far the major cost element, at about 65% is the cost of green hydrogen production and the majority of that is related to renewable power generation from wind and solar sources.
For many years, the idea of converting green hydrogen to green ammonia has been in question due to the high costs of reconversion of the ammonia to hydrogen at the destination. Approximately 25% of the energy value of the ammonia is lost through the reconversion process. The cracking technology to perform the reconversion is relatively immature and the equipment is therefore expensive to purchase and operate.
However, as more and more use cases for green ammonia are being developed the need to crack the ammonia into hydrogen is diminishing. In many cases, it is envisaged that locally produced green hydrogen can be used for applications that require hydrogen and a parallel supply chain for long-distance imports of green ammonia will exist to support applications that can use the ammonia directly and avoid the reconversion costs.
Expanding applications
Much of the excitement about using hydrogen is related to mobility. In fuel cell electric vehicles (FCEVs) hydrogen is converted to electrical power using catalysts in a fuel cell. The electrical power then drives the vehicle, like a battery electric vehicle. In mobility applications, the fuel cells are generally of the PEM type due to the requirement to cope with the high-vibration environment. PEM fuel cells prefer hydrogen.
For land-based applications and in some seaborne applications solid oxide fuel cells can be used. They are robust enough to serve in these applications, but they are not as tough as PEM fuel cells. Solid oxide fuel cells can operate with a broad range of feedstocks including hydrogen, ammonia, and liquid hydrocarbons such as methanol or diesel.
A solid oxide fuel cell manufactured by Sunfire will be used on Viking Energy, an oilfield services vessel operated by Eidesvik in support of Equinor’s offshore activities. Viking Energy will use green ammonia which will be produced by Yara at Porsgrunn in Norway. Nel will provide the electrolysers for green hydrogen production. There is also potential to use ammonia in maritime internal combustion engines, but the focus of this project is to prove the viability of ammonia for maritime fuel cell applications.
Ammonia is also being used for thermal power generation by JERA in Japan. A demonstration project is underway on unit 4 of the Hekinan coal-fired power station. This unit has a power generation capacity of 1 GW, one-quarter of the plant’s generation capacity. About 20% of the power generation capacity will be decarbonised by co-firing green ammonia with coal.
Mitsubishi Power is developing ammonia-fired power generation turbines. These will be used in place of gas-fired turbines at power generation facilities in Asia and Europe. At present, LNG is imported largely for the purposes of power generation. In the future, the LNG can be replaced with green ammonia.
Looking ahead, the traded tonnages of green ammonia for power generation are likely to dwarf the traded volumes of green ammonia for existing applications.
This article also appeared in Modern Power Systems magazine.