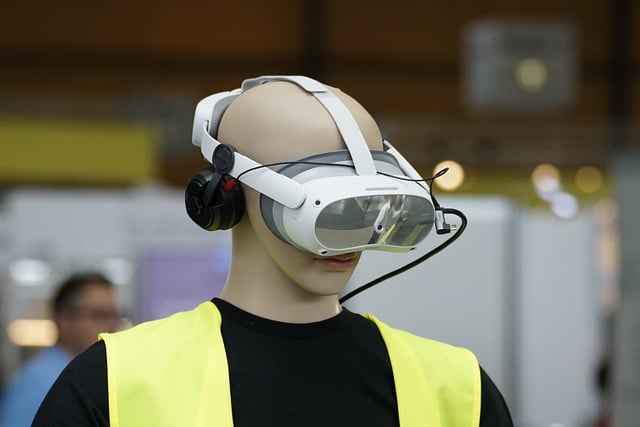
If there was ever any doubt mining is a high-risk sector in terms of health and safety, you just need to look at the statistics. According to the US Bureau of Labor, the fatal injury rate for the overall mining industry in 2021 was 14.2 per 100,000 full-time equivalent workers – more than three times the rate of private industry. This is why skills and training within the sector are paramount; people must be competent at the tasks they are doing before they are allowed to do them. The risks are simply too high. Operating heavy machinery and equipment, and also working at heights or in challenging underground conditions, are just some of the health and safety risks miners will encounter. There are established training programmes to build competency in these operations, including classroom teaching, online and on-the-job training, as well as toolbox talks that provide a communication forum between supervisors and workers to reinforce safe work practices. But, increasingly, miners are eyeing adding another medium to the mix: virtual reality (VR) technology.
More accessible than ever
VR immerses users in a fully digital environment through a headset or surrounding display, while the virtual surroundings can be computer-generated or filmed in 360-degree video. The main attraction of the technology is that it can expose trainees to real-world working conditions without the associated risks – a big bonus in the mining sector. However, miners are discovering it offers many other benefits. The use of VR for business-led applications has been going on for over a decade. During this time uptake has been nascent, but this is rapidly changing due to the decreasing cost of hardware, which has in turn become lighter and more comfortable. In addition, field-of-view, resolution and software have all dramatically improved, creating a more sophisticated and authentic experience. The basic requirements for the technology are now minimal: only a headset with wireless connectivity and a stable high-speed internet connection is needed.
Within the mining sector, Rio Tinto has become one of the technology’s biggest adopters. In 2019, the company launched LEARN+, which it describes as ‘a single user-friendly interface’ providing access to augmented and VR learning experiences. Twelve months after its launch, it said 52,000 employees had engaged with the platform. Off the success of the LEARN+ platform, as part of a recruitment drive, Rio Tinto employed Viewport to develop an app that uses VR to place trainees in the middle of a vibrant, scaleddown mine site to give them an authentic experience of the mining environment. The videos included a variety of vehicles likely to be found on a typical mine site, including dump trucks, an ore-hauling train and support vehicles. The VR video was filmed on location at Rio Tinto sites located at Paraburdoo, Karratha.
And Rio Tinto is not alone. Anglo American is also using VR and in 2023 engaged enterprise extended reality company Immerse’s digital platform to host, manage, measure and distribute almost 50 apps from seven content creators to its globally dispersed staff. In fact, industries with high-risk environments, like mining, have been early adopters of the technology due to the “critical importance of effective training for safety and operations”, according to Tom Symonds, CEO and co-founder of Immerse.
Normet, an underground mining technology provider that works with Codelco, among others, has been using simulators to train mine workers on how to use its equipment for about 15 years. Around six years ago, it decided to integrate VR to its programmes and now uses the technology on two underground process training courses: concrete spraying and rock scaling. To build the VR application, the company fed digital twin data of both types of equipment – this is essentially a 3D digital model of every single component of a machine, such as hydraulic cylinders and tyres – into the VR simulators so miners are trained on simulations of real machines. “This creates a digital learning environment that reflects real life,” explains Harri Sonninen, global product manager at Normet, who has been responsible for driving the use of VR at the company. “The machine in the VR will react in the same way as it would in real life.”
This is a technique also used by Rio Tinto, which uses digital twin technology of standard autonomous trucks, trains and drills used across its mines in the Australian Pilbara for its virtual reality training applications.
Enriching the learning experience
Taking the physical world and digitising it in this way offers opportunities to address some of the shortfalls of traditional training, says Hayden Morison, director of sales and marketing at Australian-based Next World.
“In traditional learning, students can be exposed to a 300-page PowerPoint presentation to which they often become disengaged, resulting in low knowledge retention and learning gaps that could on a worksite potentially cost them their life,” he says. “Whereas, using a VR headset, a trainee can experience what it’s like to work at heights, or in a confined space, and practise operating heavy machinery and equipment in a safe and controlled setting – meaning they can also experience the consequences of poor safety without coming to harm.”
In this way, Morison says the emotion of falling or vertigo, for example, is coupled with the learning content to foster a care factor association that helps drive long term behavioural change. This is backed up by a PwC report on the utility of VR in training, which states that scientific research shows an action-oriented experience inside a simulated environment – learning by doing versus engaging in passive processes like watching videos – drives better learning outcomes. In addition to this, digital systems allow for more in-depth trainee behavioural analysis. For example, Next World offers an analytics platform that can analyse data collected in an active headset, such as trainee reactions and focus, which is then downloaded onto the cloud to create a profile for each student.
“This can show if a student panics when dealing with a fire or heights, as well as measure their cognitive understanding of the subject,” says Morison. “This can indicate if they need more training or to possibly be transferred into a different role. The data is putting the power back into the organisation.”
Time and cost comparisons
The PwC report also highlights the cost and time saving associated with VR training, something that is attracting miners to use it. It notes that learning with VR is the most cost-effective way when it’s done on a large scale. At 375 learners, VR training achieved cost parity with classroom learning. At 3,000 learners, however, it become 52% cheaper, according to the consultancy. This is because skills training and development can be delivered quickly: PwC claims to have covered 1,000 people in a day in VR.
Morison explains what is behind this cost saving. “Instead of sending a trainer and a student to a site – where risk assessments and equipment are needed, as well as student and staff briefings – then performing the task, with VR you’re done in 20 minutes and it’s completely scalable.”
He describes Next World, which is currently working with Komatsu, Caterpillar, Anglo American and Fortescue Metals, among others, as the ‘Netflix of VR safety training’ because it offers a subscription model where firms can have on-demand access to the courses they need. The courses live on the headset, meaning no internet access is required, but can be updated or data downloaded through WiFi. The cost per student per month is equivalent to a cup of coffee, according to Morison. Furthermore, Immerse says its customers have found immersive learning allows them to increase training efficiency to achieve a 50% reduction in training time when rolled out company-wide and 76% reduction in worksite accidents after completing VR training.
Reducing environmental impact
One of the less obvious outcomes of adopting VR training is a reduction in CO2 emissions, says Sonninen. In fact, this was a key driver for Normet to shift to VR, as well as its cost efficiency benefits.
“The one-week training sprayed concrete operator course in real life would include around €10,000– 20,000 worth of cement, application materials and operating costs,” Sonninen explains. “This all incurs GHG emissions, particularly the use of concrete, which has high CO2 emissions.” Conversely, the simulator has an upfront cost but once this is paid the only cost is the teacher’s time, he says. Additionally, companies can even save on concrete post training because miners taught with the VR and training expert can produce up to 10–30% less waste on the job, according to Normet’s studies. This marries with the growing incentives to reduce waste and lower emissions in mining, including increased ESG reporting requirements.
Industry uptake
A growing group of miners are beginning to become aware of the benefits of VR for safety training, especially when done at scale. For example, stateowned Mahanadi Coalfields Ltd (MCL) in India has introduced a VR-based programme to provide safety and operational training to its 17,000-strong workforce by 2026. This is part of its plan to drive up coal production to 300 million tonnes by the same year.
At the mining industry’s flagship conference Mining Indaba this year, the Council for Scientific and Industrial Research in South Africa unveiled a newly developed VR technology for training on how to adequately respond to near-real emergency situations, such as underground fires and explosions. Developing the technology was part of its mandate to “deliver people-centred solutions that prioritise the safety of workers in mining environments,” said Sibongile Ntsoelengoe, executive manager for future production, mining, back in February.
VR is not a panacea, however. The experts stress it should be a part of the traditional training framework. “We’re not trying to replace any of the traditional methods completely, but to enhance and enrich the learning experience and make it even better for the student,” says Morison.
What’s more, although the mining sector has been quicker than others to adopt the technology for training, using it still requires a mind shift from organisations and employees. Those new to the technology should be supported and sessions should be short, impactful and well planned, according to PwC.
Sonninen believes that, previously, the industry was not fully ready to use this kind of technology at scale. Normet has plans to bring more simulator options across its training modules and has been waiting for the right time to launch them. “The industry has just got to the level where it is interested in implementing simulated training. It takes time for the sector to understand what the benefits of VR are, there still needs to be more knowledge around that,” he says.
Uptake could be accelerated exponentially, however, by the release of the Apple Vision Pro headset expected early in 2023. “That will see a huge shift in the adoption of VR technology because anything Apple does catches on like wildfire,” says Morison. When this happens, he adds, those that were early adopters, where VR is already part of the organisational culture, will be in a great position.
This article first appeared in World Mining Frontiers magazine.