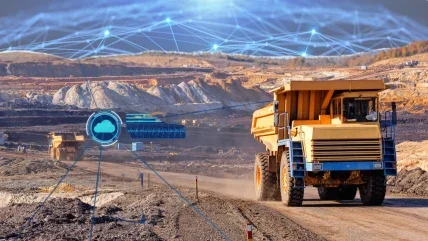
In response to these conditions, many mining enterprises have ramped up investments in digital technologies, aiming to enhance performance. However, the expected outcomes often fall short, as companies reevaluate dated strategies and solutions. Given the potential in a connected enterprise, there are some key areas of focus that can help miners achieve sustainable success.
Turn siloed data it into useful, timely and accurate information that feeds integrated operations and supports decision-making.
- Companies use less than 1% of available data effectively
- Business decisions are made based on unreliable information
- Operations focus on short-term incident resolution rather than continuous improvement
- Data is isolated within in-house applications
Data management challenges for mining industries
So, why miners still struggle to turn data into useful information essential for decision-making?
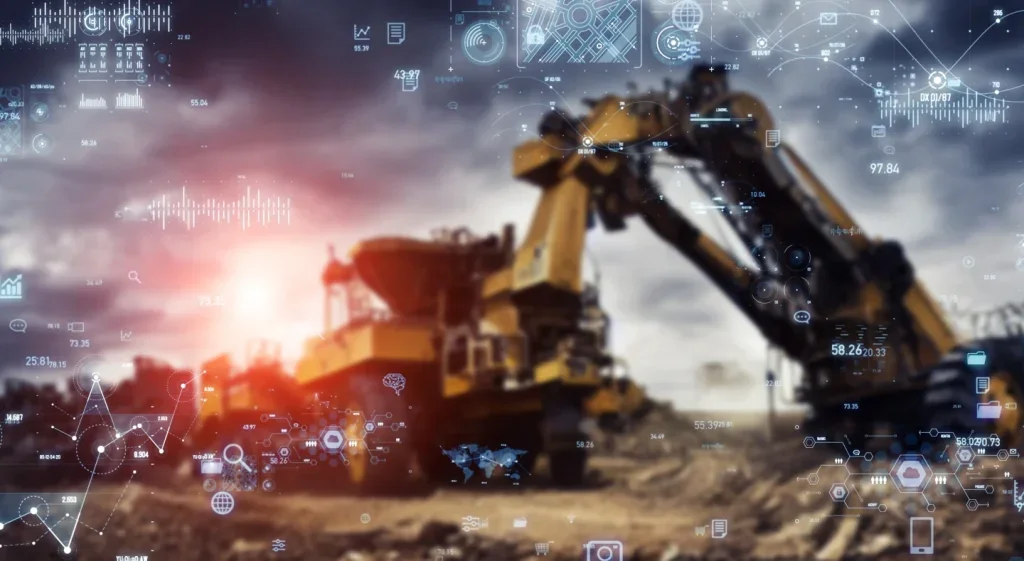
Measurement inaccuracies
The mining and minerals processing sector presents a unique set of challenges that distinguish it from other industrial sectors. At the core of these challenges are inherent measurement errors throughout the value chain. This imprecision leads to a cascade of miscalculations in inventory levels, flow rates, material losses, balances, and overall performance metrics. To mitigate these errors, the industry employs reconciliation and adjustment processes. These processes require solutions that not only facilitate such adjustments but also ensure clear documentation of both the original and modified values. Additionally, these solutions must provide transparency regarding who made the changes and when they were made.
Data availability
With widely distributed processes, networks or power outages may be common. In this event, data is collected and buffered locally before being uploaded to servers once the network is available again. The challenge for operational data users is to identify and correct any calculations or results that may be omitted from historians during outages.
Data source from many different systems
Information systems pull data from many different sources, including near real-time data in historians and control systems, and less real-time systems such as laboratory information systems (LIMS). The time stamp of data in these various systems becomes very important. While LIMS data may only become available a day or more after the sample was taken in the field, it still needs to be accurately correlated with the truck, train, flowmeter, or belt-weight that supplied the data.
Data validation
Many source systems will have their own data validation, correction, and management processes. This means data, which has already been introduced into calculations (e.g. from a week ago), may be changed at the source, modifying results used in ongoing critical operational decisions. Fleet Management Systems are notorious for this, not only changing the time of an activity, but also changing the load and unload locations, resulting in different stockpile balances and weighted grades in different locations. This is also the case for LIMS, where tests can be resampled and results modified, causing altered data to populate in historical records.
The challenge is to detect data that has changed at the source and automatically reprocess any dependent results, including stockpile balances, weighted-grades, yields, recoveries, efficiency KPIs, and throughput rates.
Manual data entry
In almost all mining and mineral processing operations, there will be some data, which is not available electronically and, needs to be manually entered by operators. This could be by field staff during operator rounds on mobile devices, or control room personnel on desktops. Either way, this process needs to be simple and intuitive, notifying appropriate personnel when a scheduled inspection is required.
Defining a best-in-class Mining Operations Management (MOM)
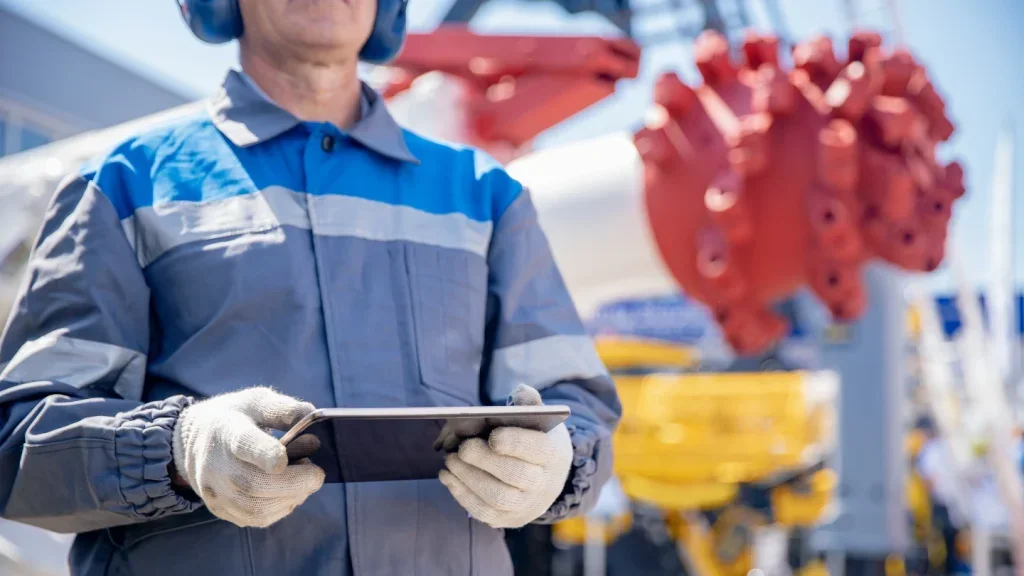
What is a Mining Operations Management solution?
Simply put a Mining Operations Management (MOM) solution connects disparate systems and aggregates data – and delivers a single version of truth by providing information in the same context across the mining operation. The integrates and models data from your traditional operations and business systems. Then delivers fit-for-purpose applications designed for mining that interact, share and cooperate on the same platform to deliver new insights.
Design and Operation
Instead of creating dashboards, templates, and forms that require heavy coding and product knowledge, a MOM solution delivers seamless visualization and data entry, is tailored specifically for each module, and can be updated by operations personnel.
Integration
Any MOM Solution needs to be able to connect and integrate databases from different systems in a seamless easy way, rather than employing strategies that use generic SQL procedures and dated REST API Web Services of varying complexity.
Genealogy
One of the major issues is the use of Manufacturing based models that take hours to reprocess. Good quality data is not available until that reprocessing has finished (one or more days). A MOM solution delivers a genealogy component.
Data Modeling and Corrections
Often systems store the source value in different “modules”, resulting in duplicate data storage and complex management when correcting or reconciling data.
A MOM solution uses integrated data from a single source for all application data across all models within a module. This means that data changes are reflected across all models and calculations simultaneously.
Modules built for mining
A MOM solution should also offer a rich collection of out-of-the-box / fit-to-purpose modules focused on mining. Some standard modules might include Production Reporting and Inventory and Storage Management, among others.
Rockwell Automation, a global leader in industrial automation and digital transformation, has helped miners to improve processes and achieve operational excellence throughout our 100-year history. From our core range of hardware products, which enable process and power integration, to enterprise software solutions that deliver continuous control at scale. Continuing this trend of empowering customers with technology that makes an impact, the Mining Operations Management Suite from Rockwell Automation unites best-in-class attributes for MOM solutions with a powerful and differentiated list of out-of-the-box features that set us apart.
Extensive mining-dedicated modules from Rockwell Automation
Agile and flexible development of new user-created modules with easy integration for future users is standard inour MOM suite. Some of the out-of-the-box modules that are critical to miners and unique to Rockwell Automation’s solution are:
OEE / Asset Utilization KPIs
This module allows KPI benchmarking of performance over time and provides a clear indication to which plant areas and equipment are performing well and which are causing production losses Not all process areas contribute equally to aggregation: the solution aggregates the proportion of time & losses intelligently.
Downtime / Loss Accounting
Our module identifies the business impact of planned and unplanned stoppages, as well as the impact and cause of rate losses and systematic causes of failures.
Short Interval Control
A brand-new module that factors that impact performance, health, and quality and are measured against known boundary thresholds then alerts operators when the circuit is not functioning as required. This allows operators to make meaningful changes within a shift to improve overall productivity.
Production Reporting
Automated reporting of actual feedstock blends, throughputs, consumption of reagents, flocculants, and outputs in the context of where they are consumed, produced, recovered or recirculated.
Metal Reporting
A critical module that aligns sample results with material movements to calculate the constituent quantities of the various elements within the overall ore flow. Recoveries and losses can be calculated separately for each mineral within the ore body.
Statistical Process Control (SPC)
This module applies statistical methods to identify quality exceptions and deviations before reaching out-of-specification limits.
Inventory Management and Storage Balances
Reporting the net balance in stockpiles, stockpile partitions, silos, tanks, and other storage vessels based on metered additions, depletions, and survey adjustments. Tracks the grade from source to destination, allowing predictions of loadout grade based on source stockpile ratios before the lab results are available. Materials and grades can be tracked by either physical or virtual models.
The MOM suite from Rockwell Automation boasts powerful single data modeling and data corrections. The MOM suite stores data from various sources with full transparency as to what data has been manually manipulated. Our robust data collection strategy and comprehensive product capabilities handle independent systems with high data availability in differing time-horizons, offering data reprocessing with little to no user intervention, creating a single source of truth for operational and enterprise decision-making.
We offer a responsive, modern web interface, which detects the device type, and automatically switches from desktop to mobile mode. The system is designed to provide self-service facilities for mobile field operators, field technicians, and other remote personnel.
The MOM suite offers modern connectivity with ERP systems for production reporting, maintenance systems and enterprise-wide reports, such as Power-BI. Our solution delivers genealogy specially designed for bulk-commodity handling, relating downstream material movements to upstream sources — from ship to mine.
Rockwell Automation’s MOM suite was conceived and designed to transform your mine with enabling technology that takes flexibility and performance to new heights. Make the most of existing data and transform decision-making from day one with a suite that is easy to deploy, maintain, and scale, with out-of-the-box features developed for mining.
For more information about the Mining Operations Management suite from Rockwell Automation visit rockwellautomation.com or stop by our booth 6113 at MINExpo 2024.