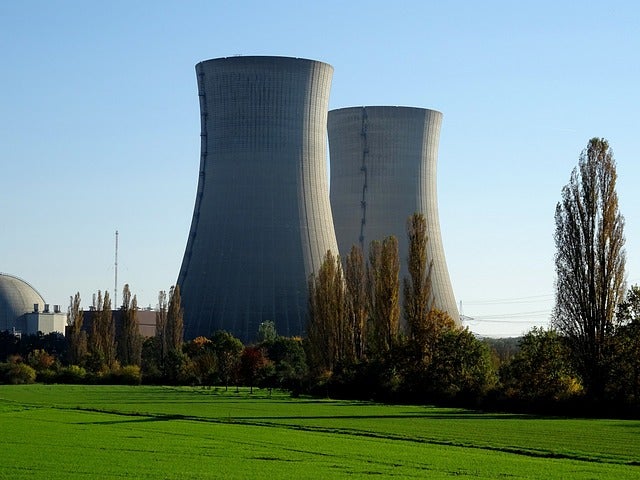
Last year the UK government announced plans to build up to eight new nuclear reactors in the UK. The move is aimed at improving the country’s energy independence and reducing greenhouse gas emissions, as well as creating thousands of new jobs. At present though, the only stations planned or under construction in the UK are EDF’s European Pressurised Water Reactors (EPR), at Hinkley and Sizewell, with two reactors at each site.
The commitment to the nuclear build programme will, it is hoped, not only deliver the generating capacity required. If all the goals in the government’s development strategy are met, nuclear could provide 20-25% of UK electricity needs by 2050. Nuclear development at this scale will also bring significant economic benefits to the UK, including to the supply chain needed to construct these power plants. Successful delivery will also strengthen the perception of the UK supply chain, which will be important given that foreign competition is strong. Indeed, UK firms will face a significant challenge from overseas companies vying for the same work. An expanded and more capable supply chain should be well-positioned to access new home and export markets, and implicit in this is a focus on enhanced quality.
One could reasonably ask what all this has got to do with a medium-sized fabrication business in South Wales. Actually, quite a lot because the transfer of knowledge and enhanced processes gained directly from the experience of working in this ultra-safety-regulated and highly rigorous sector has undoubtedly impacted the quality of delivery in other market sector applications.
The key to knowledge transfer
For obvious reasons, material sourcing and provenance are vital in the manufacture of all pressure systems, but for the nuclear industry especially its importance in the manufacture of components is on a completely different scale. Materials’ cleanliness and welding perfection are prerequisites, but by far the most important factor demanded by principals and Tier 1 contractors in nuclear is safety – for workers and of course end-users.
The Hinkley Point C project, which started in 2018, involves the fabrication of a series of enormous deaerators and feed water tanks, each weighing in at 330 tonnes. So large in fact that they will need to be shipped in sections and completed on-site. These vessels alone have been a three-year labour of love, such is the tonnage and size of each vessel – exceeded in dimension only by the main reactor vessels themselves.
Each once assembled and in place, must be able to withstand 20 bar pressure and temperatures ranging from ambient to 200 degrees. Manufactured in three sections, the first of the two fully assembled 55m-long cylindrical pressure vessels will be completed in the first quarter of 2023, to be installed internally with four ferritic stainless steel deaerator units, and capped with crown and petal dished ends.
Vessco Engineering, accredited with the Fit for Nuclear Standard (F4N) in 2018 and a member of the Wales Nuclear Forum, specialises in the fabrication of pressure vessels, heat exchangers, columns and other similar mechanical structures. Recent commissions range from nuclear processing sites such as Sellafield and power generation sites like Hinkley Point C, through to experimental fusion facilities for STEP (Spherical Tokamak for Energy Production).
So, what is it about the realm of nuclear engineering which raises the game for our work in other sectors? Again, it starts and ends with safety. A culture of absolute perfection literally pervades the entire manufacturing process because, bluntly, the scale of potential harm due to error is incalculable. Everything, therefore, aligns with the regulatory expectations placed on the UK Nuclear Licensees and is shared throughout the nuclear supply chain to support quality improvements. These range from BS EN ISO 9001 and the existing codes and standards within the Nuclear Industry; the Office for Nuclear Regulation’s (ONR) Technical Assessment Guides (TAGs), IAEA’s General Safety Guides (GSG) and a host of others.
At a practical level this has meant the intensity and precision of the documentation is much greater than anticipated, and that in no way underestimates the quality systems with which we were already familiar in our work in, say, the oil and gas sector which has its own inherent risks to manage. Nonetheless, in terms of on-site production processes, the level of scrutiny is also a lot higher. All of this, of course, impacts time and cost, which is undoubtedly one of the key learnings when it comes to estimating for new projects. In fact, so much investment of time and planning and trialling has been necessary for the fabrication of the first HPC vessel that cost-recovery and margin won’t come through until the closing phases of the second 330-tonne structure.
Through this iterative process, we have learnt how to make process improvements, such as how to weld the superstructures better, how to manufacture the dished heads in a different way, how to speed up the fitting and welding of the nozzles, and so on. We have also determined how best we can run different parts of the structure fabrication in parallel, rather than do everything in one long sequence. Given the limited working space within and around some parts of the vessel structures, though, there are only so many pairs of hands that safely can be useful at any one time. We have none of the space advantages that one might have, for example, building an aircraft carrier. The vessel has to be rotated in place during manufacturing so we can have the necessary working space to access all of the surfaces, externally and internally. Thereafter, we can manufacture the internals, concurrently with the main vessel, including the saddles, bringing all of the various elements together at the end.
Building knowledge into savings
Looking ahead, the time taken earlier for the initial designs, development, and procedural documentation can safely be cut back dramatically. In fact, the whole production cycle should be reducible by up to two-thirds of the original cycle, allowing the procedures to be performed in a more time-efficient manner. Going forward, this will enable more cost-effective manufacturing.
All these are valuable learnings which can feed back into the nuclear realm for other manufacturers facing similar challenges. In the case of Vessco that includes the water utility industry, chemicals manufacture and the oil and gas sectors. It has, for example, led to us using experiential data on the length of time it takes to manufacture specific structures and components. All of these learnings will be useful across the supply chain. Importantly, however, it can also add value to other market applications.
Interestingly, one of the downsides of the nuclear sector’s rigour is the pace and resistance to incorporate potential learnings from other industries. For example, synergic MIG welding techniques are superbly suited for delivering neat fabrication quickly, but this is not yet approved for use in civil nuclear. In due course, for the right applications that may come. In the meantime, there’s a good reason why most of the traffic of learning is one-way.
Learning how to prepare for inspection and test plans and incorporating these well in advance in the organisation of workflow, provisioning for the right welding procedures for each application, and building up a library of procedures and techniques for future use, all feed into a compendium of best practice aimed at reducing time and improving quality. Reiterative documented learning in this way eventually reduces 40 days of the process down to fifteen whilst improving the quality, and above all the safety, of the end product. What is also clear is that we are not alone; our experience is being mirrored widely elsewhere across the nuclear Tier 2 and Tier 3 supply chain.
This article first appeared in Nuclear Engineering International magazine.