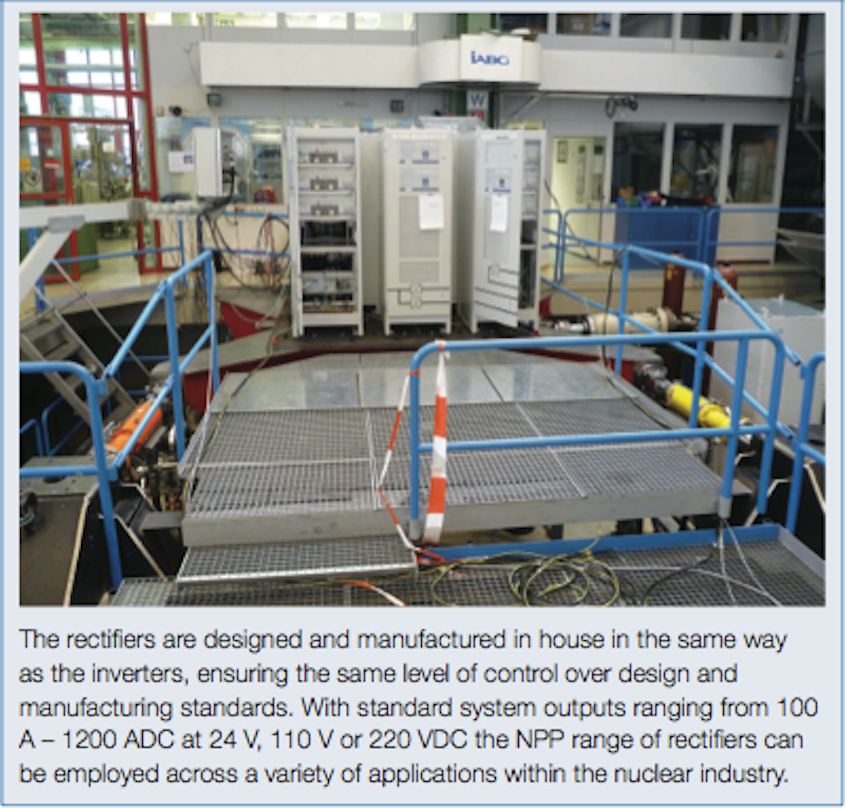
In nuclear power stations, safety is always an overriding concern. Safety can only be assured by the uninterrupted availability of electrical power delivered to the various process, control and alarm systems distributed around the plant, as well as the instrumentation that provides continuous visibility of their status to the plant’s operators.
Providing power conditioning and protection solutions that ensure this level of availability – often in harsh electrical and environmental conditions and usually for widely diverse, application-specific levels and types of AC and DC power – is challenging indeed. It’s a challenge that’s exacerbated because any solution provided has to be supported over a nuclear plant’s operational life of many decades.
On 25th July 2006, a short circuit occurred in Sweden’s Forsmark 1 nuclear reactor. Short circuits can usually be properly managed but this one caused a power failure that almost led to catastrophe. The power outage threw the plant’s control room into a state of chaos; as the power failed, so did two of the plant’s four emergency backup generators. The numbers on the controls became meaningless and it took a full 23 minutes before the workers were able to bring Forsmark 1 back under control.
This type of event, which is not unique in the history of nuclear power generation, highlights the critical need within nuclear power plants (NPPs) for power that is always available and of impeccable quality. Operators must have visibility and control at all times to avoid any possibilities of scenarios like that at Forsmark 1. Meeting such high requirements for power availability and quality place special demands not only on the power protection equipment – rectifiers, inverters, UPSs, DC-DC converters and associated components that delivers it, but also on the equipment’s suppliers.
Nuclear plant power conditioning requirements cannot be satisfied simply by ‘off the shelf’ power products. While such products, if suitably qualified, make an essential starting-point, customisation is often needed in terms of both electrical and environmental protection capabilities, and of meeting each NPP’s particular power requirements. NPPs are designed for lifetimes of approximately 60 years so they must establish partnerships with well-established, stable suppliers to ensure they will enjoy reliable support and parts availability throughout these extended lifetimes.
NPP systems and environments
NPPs contain a wide variety of systems with sensitive electrical and electronic equipment distributed around their sites. Safety related systems and alarms, which are ubiquitous, require AC mains and possibly different DC voltages – 24, 48,120 or 220 VDC. Process control systems comprise different types and sizes of programmable logic controllers (PLCs) requiring AC mains, as well as sensors and actuators operating on 24 VDC. As in any enterprise, data processing equipment is needed for handling administration, purchasing and stock control. This is susceptible to damage from power failures or faults and must be protected to avoid costly disruption and delays. Communications systems must also be protected – especially as part, if not all of their operation, has safety implications.
There are also a number of valves around the plant that must be operated during an emergency. Maintaining power to their actuators under all circumstances is therefore essential. Overall, the entire critical load must be protected from blackouts, brownouts and electrical disturbances including surges, transients, voltage and frequency variations and harmonic distortion.
Irrespective of the power protection equipment required, it must be fit for operation within its target environment. NPP sites tend to provide this in the form of indoor clean, dry rooms with temperature control. However, this is not always the case. We have supplied equipment capable of operating at up to +55°C.
This approach also extends to solving other environmental challenges, particularly ingress, shock and vibration up to seismic levels, through the robust quality of its cabinet systems – which the company completely controls by in-house design and manufacture – as well as that of the power conditioning equipment they house. For some NPP applications, it has packaged equipment into cabinets with IP 42 ratings to better prevent ingress of dust and liquid. In particular, IP 42 guarantees protection against vertically dripping water and sprinkler deluge, which becomes very important if sprinklers near the power protection equipment are activated by a fire alarm. Because the cabinets are built to a flexible design concept, they can be dimensioned to include backup batteries as well as the equipment.
Resilience to seismic shock is often a requirement for the power protection equipment, as it is for the entire NPP. Cabinets must be designed for both the mass of the equipment they contain and the characteristics of the plant’s geographical location. Reinforcement is achieved using diagonal braces or cruciform shapes and increased strength through an increased number of screw fittings.
If these measures are insufficient to meet the demands of the site’s location, or the size of the equipment, those with expertise can produce cabinet systems with welded designs. Design calculations allow for predicted G-force per axis, damping factor, elevation and the installation site; all of these factors can make significant differences. These calculations are supported by empirical strength tests, performed on individual cabinet components, distribution and power supply modules within Benning’s own test laboratories (see Fig.1).
The overall design is then inspected by external test institutes in accordance with international standards such as IBC 2012 (International Building Code), NEBS GR-63-CORE, the GOST standards, IEC, and UBC (Uniform Building Code).
Just as for its cabinets, Benning controls the quality of the power conditioning equipment they contain through in house design and manufacture.
Inverters and rectifiers are designed to an analogue rather than digital topology, so no software is needed for operation. The possibility of common mode failures, in which all systems react in the same way to a triggering event, is excluded; this can be a hazard with software- based systems. The Y2K ‘Millennium bug’ was a notorious example of this type of behaviour.
In manufacturing terms, the electronics uses the same ‘state of the art’ technology as found in all power conditioning equipment currently available, with the difference that over-specified components are used throughout to ensure an extended working life. Additionally, the components are laid out on the printed circuit boards (PCBs) with spacing that prevents arcing across tracks, whilst arcing prevention can be reinforced by suitable PCB coatings if required.
There are, however, further steps that can be taken to accommodate NPP reliability expectations if required. Special, higher EMC requirements can be catered for, as well as an ability to provide very high short circuit currents and thereby provide a high fault clearing capability (to boost protection against the Forsmark type of event mentioned earlier). Furthermore, the blocking of large (dv/dt) input voltage spikes is also desirable.
Other techniques include failure modes and effects analysis (FMEA) to identify potential failures and their impact and identify where changes are needed. Accelerated life testing of components and systems can also be performed.
As the Forsmark incident clearly highlighted, high availability, although essential, is of limited value unless operators always have clear visibility of current equipment and system status. One solution is to use analogue control and monitoring technology such as voltage, current and frequency meters and relay contact signals, to exclude the possibility of common mode software failures as mentioned above. This does not preclude employing digital instrumentation and displays as well, to enrich the information available to operators during normal operation; serial communications and networking with protocols such as Modbus or PROFIBUS can also be used, but should be restricted to monitoring without control.
Compliance with international and locally prevailing standards must be factored into any power protection design. The IEEE standard for qualifying category 1E material is particularly important for safety-related areas, while meeting applicable legislation for EMC radiated emissions and susceptibility is essential in all applications. Also essential to all NPP applications are the safety standards of
the Nuclear Safety Standards Commission (KTA); these specify precautions, using the latest available science and technology, against damage arising from building and operating nuclear power plants, in order to meet specified protective goals. DIN 41773 is applicable to equipment used for charging lead-acid batteries.
Practical rectifier and inverter examples
In practice, power protection and conditioning within NPPs is typically handled by inverters and rectifiers rather than complete UPS systems. This approach provides the flexibility required to efficiently manage the range of AC and DC voltages found throughout nuclear sites. We can look at actual rectifier and inverter examples to exemplify nuclear plant operators’ expectations of and priorities for their power protection equipment.
Benning, for example, offers both single-phase and three-phase static inverters with wide power-handling capabilities. Ratings
from 5kVA to 400kVA are possible, with input voltages from 48 V to 220 V. The inverters use electronics based on well-proven IGBT technology to generate isolated, regulated sine wave outputs with low distortion, contributing to good dynamic behaviour under load changes.
If DC supply is lost, the inverter will automatically transfer to bypass operation via the static bypass switch, ensuring uninterrupted AC supply to the connected loads. A manual bypass switch is also integrated for maintenance purposes.
These inverters are designed and manufactured according to the quality procedures for 1-E NPP applications and in accordance with KTA guidelines. They are built into all-welded seismic rated cabinets, with analogue control circuits, overrated components and convection cooling, eliminating fan failure issues. These measures facilitate a very long operational life for the inverters, with high MTBF ratings. Digital instrumentation and networking capabilities are also provided, delivering real-time status information to operators.
In house design and manufacture, as well as assuring quality, allows for bespoke designs to be configured, offering addition or removal of components, upgrading of system IP rating and changes to cabinet layout and dimensions.
The inverters can be complemented with rectifiers offering comparable standards of quality, reliability and longevity. Similar construction guidelines, with all welded seismic rated cabinets, analogue control circuits, overrated components and convection cooling, are followed. Wide operating temperature and input voltage ranges ensure reliable operation in the harshest environments.
The rectifiers can be used as direct feeding power supplies, or battery chargers for either Lead-Acid or Nickel Cadmium batteries. Their low DC ripple and temperature-compensated DIN 41 773-compliant charging characteristics (Fig. 2) maximise battery life and performance, extending the useful working life of the batteries.
Conclusions
Not surprisingly, safety and therefore power availability to facilitate continuous monitoring and control, is the main concern – and availability applies not only to the power equipment itself but also to the instrumentation that provides visibility of its status. This availability must be sustained through harsh environmental conditions, including possibly seismic disturbances.
Suppliers must also be able to offer solutions customised to each NPP’s particular requirements; this not only ensures that tough environmental and electrical challenges can be overcome, but also that highly specific levels and combinations of DC and AC, single-phase and three-phase power distributions can be handled economically and flexibly. Flexibility is promoted by using combinations of inverters and rectifiers rather than relying on monolithic UPSs.