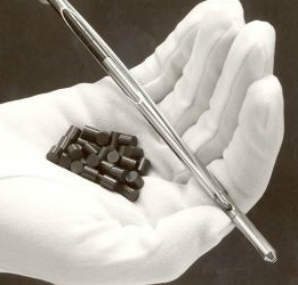
Standard fuel comprises uranium dioxide ceramic pellets sealed in a zirconium-alloy cladding tube. This fuel-form serves the industry very well, however, it is recognized that new fuel materials and design features could provide greater levels of accident tolerance.
New types of nuclear fuel incorporate various safety enhancement features, for example, more inert cladding, or a higher thermal conductivity ‘fuel-meat’ (pellet). To assess the overall safety level for a prospective new fuel it is necessary to consider the fuel- meat’-cladding-coolant system, sometimes referred to as the ‘fuel system’, in its entirety.
The OECD Nuclear Energy Agency (NEA) has been continually assessing and revising safety criteria for standard nuclear fuel. An updated technical review of these criteria was published in 2012. The NEA document is exclusively focussed on uranium oxide fuel with zirconium alloy cladding. Within this domain it provides comprehensive coverage of the safety-significant considerations for such fuel. It also provides a good basis for describing safety issues for nuclear fuels more generally.
The various NEA criteria can be sorted according to five broad groups of factors that must be addressed when assessing the safety of a fully-deployed fuel assembly:
- Neutronic design parameters (for example,reactivity coefficients)
- In-core behaviours and changes (for example, corrosion, crud deposition)
- Mechanical factors (for example, seismic resistance)
- Activity inventory (that is, the amount of dispersible radioactivity within the fuel)
- Other factors (in particular, thermal-hydraulic safety credentials).
While all safety attributes are important when refining standard nuclear fuels, it is the second group of factors concerning fuel behaviours that is most useful in any comparative assessment of safety credentials for various new types of LWR fuel. Numerous changes are induced in nuclear fuel due to the rather harsh thermal, chemical and radiation environment in which it operates. Ultimately, the concern is the release of radioactive material to the environment. It is the fuel-meat itself and/or its cladding that
provide the primary barriers to this end-point — hence the safety significance of the degradation experienced by these parts of a fuel during in- core life and throughout long-term storage.
Prerequisites
Below are several fundamental fuel attributes essential to the viability of the fuel.
Safe neutronic and thermal-hydraulic operation is so fundamentally important for all nuclear fuel that it can be assumed that any new fuel will have cleared this requirement before further development. Fuel components should have adequate resonances in the epithermal neutron energy range to ensure sufficient Doppler effect for the core to be intrinsically stable in fast reactivity accidents. Excessive neutron capture should be avoided to limit reactivity penalty and to minimize risk of positive void coefficient or positive moderator temperature coefficient. Designed power ratings should be such that sufficient margin is maintained to the level where the cladding surface loses thermal conductivity (through dry-out). It is assumed that new fuel designs conform to national criticality safety regimes.
Similarly, a fuel design must not contravene national spent nuclear fuel management strategies in the country where it is used. In any case, it should be possible to demonstrate that a new nuclear fuel form is suitable for permanent disposal in an underground facility, and also in interim dry storage conditions. All such conditions are assumed to be met at the broad policy level. Technical fuel behaviour issues relating to geological disposal need to be considered for new nuclear fuels.
Finally, fuel must be robust at an assembly level, as well as at the fuel-meat-cladding- coolant level. A fuel structure has to be able to absorb sizable impact energies without allowing breach of the fuel rods themselves. NEA criteria specify such resistance in the form of seismic loads, among other such forces. For the purposes of developing new fuel technologies with advanced claddings and fuel matrix systems, it can be assumed that the mechanical design for any new fuel will be readily achieved such that impact resistance criteria are met.
Behaviour: normal conditions
All fuel must demonstrate high safety margins in both normal operating conditions and during Anticipated Operational Occurrences (AOO). This is a key principle for a new fuel type and it is split into two statements. The first states the obvious expectation that fuel retains its full integrity in these situations, and a second expresses the expectation that its behaviours should be steady and predictable, in recognition that fuel does undergo considerable change throughout its in-core life. The tolerance on activity release from a fuel in the case of AOO is related to the probability of this transient occurring: the lower this probability, the higher the tolerated release.
Fuel cladding undergoes chemical transformations in the high-energy core environment. Oxidation and hydriding reactions are notable for metal claddings like those of zirconium alloy. The reactions have safety significance because the oxide and hydride products can compromise the strength, corrosion resistance and heat transfer properties of the cladding barrier. Also, chemical reactions may produce combustible products (for example, hydrides). Developers of fuels with cladding that is not susceptible — or has reduced susceptibility — to damaging chemical deterioration can claim a significant safety margin benefit. Resistance to oxidation needs to be considered separately to hydriding resistance. The extent of cladding interactions with a number of
key reactive species needs to be taken into account, including those associated with water radiolysis, as well as corrosion products suspended in the coolant.
Fuel cladding loses ductility when strained beyond an elastic limit (for zirconium alloys this is ~1% strain in the circumferential direction and 2.5-3.5% axially). The strain results mainly from stress imposed by pellet swelling but there are also thermal expansion and fission gas pressure terms. Strain limits are established according to the specific fuel environment and design burnup (and may even be beyond the elastic limit). Irradiation-induced processes cause zirconium alloy fuel cladding to gradually lengthen while operating in-core. This growth is tolerable, but should not be excessive and it must not result in interaction with fuel structure components at either end of the fuel assembly. Cladding also has fatigue limits that dictate the number of power ascension cycles or local power changes (associated with control rod movements) that a fuel can safely undergo before the probability of failure exceeds an acceptable level. New fuels can be credited with safety margin benefits if they use claddings that are demonstrably more able to accommodate these slow dimensional changes.
Fuels with free-standing claddings (as for example LWRs) should be resistant to collapsing onto the underlying fuel due to system/coolant pressure, especially as induced by neutron flux effects (and associated heating). Resistance to collapse is a function of the strength of the cladding material (including that deriving from its thickness) and is also dependent on the initial internal pressure for the new fuel design. (The response of cladding creep is related to that of rapid collapse, however, creep takes place over much longer timeframes and can be beneficial to the heat-removal properties of the fuel system if it occurs in a steady, predictable manner, and does not lead to unacceptable PCMI, pellet-clad mechanical interaction). For this reason it is preferable to treat in-core creep separately as a distinct response in a fuel safety assessment.
A pellet-based fuel operating under normal conditions should reach its end-of-cycle life with an internal gas pressure that does not challenge the ‘lift-off’ limitations of the cladding material. In other words, the gap between the pellet and the cladding wall should never increase by ‘ballooning’ of the cladding tube due to excessive fission gas pressure. The probability of cladding lift-off can be reduced by: (i) reducing the release of volatile fission products from the fuel-meat material, and (ii) using a high-strength cladding material. Pellet-based fuel undergoing a rapid power ascent will suffer stress from the impact of the expanding pellet and gases against the inner cladding wall. This stress should be minimal, manageable, and not threaten to breach the cladding at any time throughout the life of the fuel. The effect is of concern mainly during reactivity insertion accident (RIA) scenarios, however, it can be relevant for high burnup fuel under normal power operations. High burnup fuel contains significant amounts of fission gas (mainly in the pellet rim) and may have lower cladding strength (due to oxidation) or higher brittleness (due to hydride precipitation). Resistance to PCMI can be derived from a lower thermal expansion tendency on the part of the fuel material, softer pellet material, a lower fission gas inventory, or higher cladding ductility. Fuels incorporating material with these properties can claim some safety margin credit against PCMI damage.
As the fuel operates in normal or AOO conditions it should manifest either minimal chemical interaction between the fissioning fuel material and the cladding and/or the chemical interactions that occur between the fissioning fuel material and the cladding should be demonstrably benign in terms of threatening cladding integrity. Chief among the chemical mechanisms known to cause zirconium cladding damage is stress corrosion cracking (SCC).
Explicit consideration of the fission product retention capabilities of the fuel-meat/matrix should be taken due to the key significance of the changes that take place in the fissioning part of the fuel as a result of fission product deposition.
Fuel rods should be highly resistant to ‘fretting’ wear between cladding tube and fuel assembly contact points, and between the cladding tube and foreign debris material that may be trapped by a structural member of the fuel such as a spacer grid. Such wear results from flow-induced movement and the resulting friction between the contacting surfaces. In general, the occurrence of this type of degradation is being reduced by better reactor operation practices (mainly through foreign material controls) and via novel grid, spacer and nozzle designs.
‘Cruds’ are complex materials deriving from dissolved and suspended substances in the aqueous reactor coolant that may deposit/precipitate on cladding surfaces if water chemistry, local temperature and flow turbulences allow. This typically occurs near the top of the fuel where it is associated with (sub-nucleate) boiling. Cruds form a porous layer that can capture boron from the coolant, inducing local flux depression (‘Crud Induced Power Shift’) which in turn can cause local burnup shadow, fuel reconditioning and rapid power ramps if the crud is dislodged. Although the source of crud is not within the fuel-meat, nevertheless, its build-up can depend on the material properties and local heat flux of cladding surfaces where deposition is most likely.
(See also Part II: accident and storage conditions)
Based on the report ‘A Framework for Assessing the Safety of New Nuclear Fuels’ prepared by the World Nuclear Association Fuel Technology Working Group. This article was originally published in the January 2014 issue of Nuclear Engineering International.