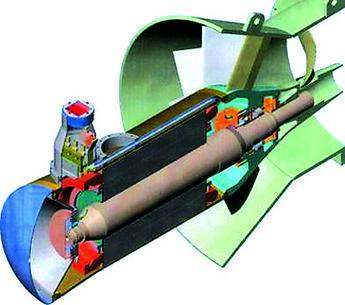
The Nussdorf project was awarded by Verbund-Austrian Hydro Power and its project partners EVN and Wienstrom, to VA Tech Hydro, one of the leading suppliers of equipment and services for hydropower plants and utilities, together with Porr Technobau and Verbundplan as consortium leader. It has sent an important signal concerning the viability of hydropower as a renewable source of energy. The total project value is around r15 million. The plant is due to commence operation in summer 2005.Origin of the canalDuring extensive regulation of the Danube between 1870 and1875 a redevelopment of the intake to the Danube canal in Nussdorf was also undertaken. In 1872 the so-called “Swimming Gate” was designed by Wilhelm von Engerth, a member of the Danube regulating Commission, to control the inflow to the Danube canal and for ice defence. The Swimming Gate was replaced by a movable weir (Schemerl Weir) with a width of 30 m, together with the ship lock, in 1898. The architectural design of the weir and the administration buildings was accomplished by the well known Jugendstil architect Otto Wagner and because of its great architectural value the ensemble is preserved as a historical site. Owing to improved flood control a reconstruction of the ship lock was achieved in the period 1964 to 1966 and in the years 1971 to 1975 two radial gates arranged in tandem replaced the original needle weir. These modifications took into account the total necessary flood control for all Vienna – the project can sustain up to 14 000 m3/s. Operation of the weir Regulation of the Danube canal is accomplished through the Nussdorf weir, and by the ship lock. Admission values are regulated by an operating scheme for the weir and lock –
essentially it is differentiated between summer (April to November) and winter operation (December to March). The current operation scheme provides for a continuous flow of 70 m3/s during winter and up to 225 m3/s during summer, depending on the volume discharge of the Danube river. During the winter months a uniform admission to the Danube canal of approximately 70 m3/s is ensured by the upper gate of the ship lock (weir closed). During summer operation, admission to the Danube canal is ensured by the Schemerl weir, depending on the flow of the Danube (70 – 225 m3/s). In case of flood, admission flow is reduced until it stops completely, depending on the water level at the Sweden bridge (which is influenced by the backwater of the Danube). For design reasons flow through the ship lock is limited to 70 m3/s. In the forebay of the Freudenau hydropower plant the water level in Nussdorf is raised by approximately 4 m. During implementation of the Danube power station at Freudenau (1993 to 1997) it was intended to build a small-scale power station near the weirs at the intake of the Danube canal (Schemerl weir) at Nussdorf. The idea was that the head caused by the banked up waters at the Schemerl weir could be utilised for power generation. However, this project was at the time not pursued because power rates were too low for the high projected investment costs to show adequate economic feasibility, and at the time there was no sufficiently developed technology available to implement turbines close to the weir. An originally proposed alternative downstream of the weir was also rejected, for aesthetic reasons.The realisation of the “Nussdorf small-scale hydropower plant” project became economically viable only after new ‘green power’ legislation had been passed and VA Tech Hydro’s innovative Hydromatrix technology had become available. At this point Verbund Austrian Hydro Power AG (AHP), the successor of Donaukraft, re-initiated, together with EVN Naturkraft and Wienstrom Naturkraft, the process of realising a small-scale hydropower plant. A major feature of the project was its careful integration with the well-known and historic Nussdorf weir building complex. Using the Hydromatrix technology, this historical site would not be compromised.The new plantThe new plant is being built downstream of the existing Schemerl weir in the stilling basin of the lower radial gate. It consists of a 30 m long, approximately 12 m wide and 7 m high over-flow hollow body weir with attached spillway gates, twelve Hydromatrix turbine generator units (TG-units) each in its own turbine chamber and an operations building.For installation purposes a vertical access pit is to be opened up on the weir left bank, integrated into the operations building. To allow installation and, if necessary, replacement of the units the roof of the building can be removed. Each of the twelve units can be switched on and off individually. The concreted draft tubes are equipped with gates, and in order to be able to dewater each turbine chamber individually, each TG unit has its own intake gate. The turbine chambers are closed with removable pressure covers. The interior space of the overflow structure is equipped with a lifting gear on two rails. With this lifting gear the TG units can be lifted and laterally moved and deposited at the vertical access pit. Each TG unit is supported by guide rails, which are located at the intake of the draft tube, allowing easy installation and dismantling. Cables run from the generators to the switchgear, which is located on the left bank in the operations building. All transformers and medium voltage cubicles are located in this building and from there the distribution to the switchgear in Heiligenstadt takes place.In order to be able to adhere to the operating scheme at any time, and after the construction of the power plant, a spillway gate in form of a flap is to be installed on top of the overflow structure. This gate in combination with the flow through the turbine chambers will ensure that the required discharge for the weir operating scheme is released.Hydromatrix TG unitsThese consist of asynchronous generators directly connected to the runner. The stator is designed as a watertight casing box and bolted to the distributor. The guide bearing and the combined guide-thrust bearing at the tail waterside are designed as oil lubricated roller type bearings. For the regular oil change neither emptying of the turbine chamber nor lifting of the TG unit is necessary. The distributor with its fixed guide vanes forms an integral part of the watertight generator housing. The unregulated runner with the hub is cast in one piece made from aluminium bronze. To ensure high efficiency, the hydraulic contour for the runner, the distributor and the draft tube was developed at VA Tech Hydro’s hydraulics laboratory in Linz, Austria.The shaft seal is located at the tailwater side and is designed as a maintenance free face type seal capable of withstanding all operating conditions. The ‘trash rack’ conceptA six-piece circular arc rack is located in front of the intake to the TG-units. Individual racks are fixed to the existing weir bottom and at the crest of the weir, and are bolted together. The debris drawn into the intake of the Danube canal will be disposed of, or passed on, in in a variety of different ways, distinguishing between debris that is collected before• one of the lowered radial gates• the turbine trash rack• the spillway gate. In the first case the upstream radial gate is being used as an immersing wall. Thus the situation regarding debris in the area of the weir will remain as it was originally, that is to say debris collecting before the radial gate can be taken out with a crane and truck as has been done up to now. Debris that is pressed below the existing radial gate either floats to the surface or is collected in front of the rack, which is arranged in an arc of a circle. Six integral trash rack cleaning machines are located at the downstream side of the rack and are well protected. Floating debris comes to the surface and will be discharged over the spillway gate. This corresponds to the original situation – the discharge of trash takes place continuously. Debris at the spillway gate has to be collected in a similar way to that before the radial gate by means of crane and truck. Since a large portion is either collected in front of the radial gate or is continuously carried away with the flow over the spillway gate, only a small proportion of the debris collects in this area so the effort required for retrieval is relatively small. Debris that is pulled to the surface by the cleaning machines and carried along by the flow will be removed on a continuous basis. Shut-of devicesThe intake gates can be individually operated by their hydraulics and make complete locking of the turbine chambers possible. Dewatering of each turbine chamber without impairing the operation of the other TG units can be accomplished by closing the draft tube gates simultaneously. The turbine chambers are divided from the control room by bolted pressure covers. After lowering of the intake and the draft tube gate and emptying of the turbine chamber the pressure cover of each TG unit can be opened for maintenance work. It is also possible to close the pressure cover without the TG unit in place and to control the flow through the turbine chamber and the draft tube respectively with the up- and downstream gate. An air-bladder operated spillway gate will be installed consisting of a steel skin plate with stiffening ribs. Several chambers of fibre-reinforced rubber filled with compressed air support the skin plate. By changing the pressure of the chambers the position of the spillway gate can be changed. Lateral sealing of the spillway gate is carried by the side panels, which are aligned at the banks of the weir. By heating of the stainless steel side panels and introduction of air in front of the skin plate of the spillway gate, icing up and freezing over is prevented. The gate is designed to be capable of discharging 225 m3/s even if three TG units are shut down.
TablesTable 1 Hydromatrix technical data