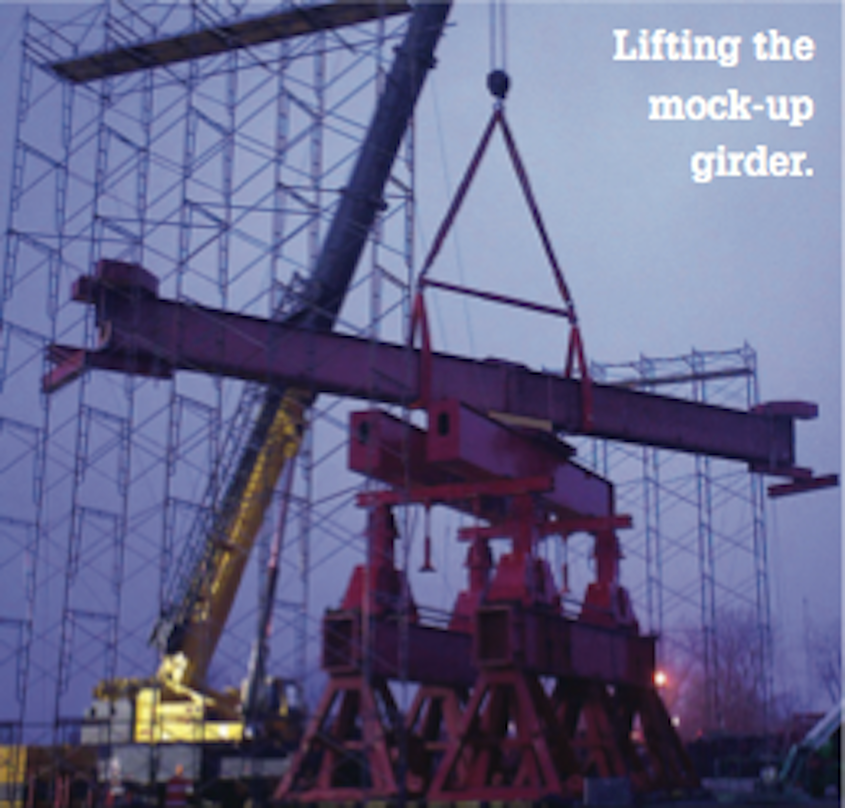
A2.2GW electricity generation plant in the US is saving millions of dollars in maintenance outage costs thanks to a recently installed 250-tonne turbine bridge crane while adjacent turbine generators ran at full power with no down time. Whiting Corporation, which commissioned and installed the crane, said carrying out the installation of the bridge crane while the station was operating not only saved millions of dollars but also a great deal of time prior to an upcoming refuelling outage.
The installation saved $18 million that would have otherwise been absorbed into the community rate base. The savings achieved in time and money were applicable to other turbine, generator and heavy lift applications across a wide range of industries seeking to enhance safety and avoid downtime.
Safety was a priority for the heavy lift at a nuclear generating station in Michigan, which produces enough power for a city of 1.25 million people. The Whiting team constructed an entire hydraulic heavy lifting and rotation test structure off-site in preparation for the actual installation.
The project was achieved using multiple telescoping gantry systems and a hydraulic turntable to safely lift and rotate components for the 250-tonne bridge crane with 60-tonne auxiliary hoist. It also cut the retrofit outage by a week, says Dave Weber, director of Nuclear Services at Whiting Corporation.
Applicable to diverse industries using turbines, the project has won a global award for the operation to rig and lift more than five million pounds of components while adding a second Whiting crane to the plant’s generating room as part of an upgrade to enhance safety while curtailing downtime and potential accident hazards.
The award recognised ‘top industry practice in heavy lifting’ and was made at the 2015 Power Engineering Awards during Power Generation Week in Las Vegas in December 2015.
Workers configured the gantry system as an engineered temporary lift assembly that had never been used in such a manner during power operation. The design was less invasive to the plant structure.
The company said in a statement: ‘The second bridge crane will allow for a reduction in outage duration by as much as seven days in the upcoming turbine retrofit outage alone. All future outages will continue to realise additional costs savings, because a point of vulnerability has been eliminated through the addition of a second bridge crane.’
Highlights of the lifting operation included:
- 290 lifts (86 classified as high-risk) all successfully completed.
- The G1 girder weighed 110,000 lbs (nearly 50,000 kg), the G2 girder weighed 96,000 lbs. (nearly 44,000 kg), and the main trolley weighed 88,000 lbs (nearly 40,000 kg).
- More than 5.3 million lbs rigged and lifted (2,267,961 kg) including 650,000 lbs of test weight.
- Zero safety incidents.
A full-scale mock-up of the hydraulic heavy lifting and rotation structure, which exactly replicated actual lifting conditions, was
used to remotely load test the innovative telescoping gantry system and turntable technology to 125% of maximum load through the entire range of movements, while maintaining levelling tolerances to 0.5%.
Lifting the mock-up girder
The lifting team met the provisions of Subpart 2.15 of ASME NQA 1-2008 quality assurance requirement, stipulating a dynamic load
test equal to 110% of the rate load, instead choosing to proceed with a more conservative 125% rated load test. The trial also exceed
the new ASME P30.1.2014 ‘Planning for Load Handling Activities’ code issued during the project’s planning phase, which was exceeded despite not being part of the initial scope.
Test loads were intentionally taken beyond the operational limits to ensure there was sufficient margin to encompass any of several failure modes that could be encountered during installation. Controls were established to ensure the assembly of the gantry system was identical to that used during the demonstration, with redundant level control, LED levels and
3D Laser Scanning Total Station guidance, time lapse and live video of the entire sequence.
An additional total station and operator was added to monitor the power towers in the reverse operating direction and a communication protocol was established. The system was reviewed for compliance with the new ASME P30.1 and found to be in alignment with this latest code.
“The installation method require collaborative efforts between ourselves as the crane vendor, the utility and the installation contractor to manage the risk by performing a robust demonstration of lifting operations, in addition to independent review of analytical calculations for the temporary engineering lift system," said Weber.