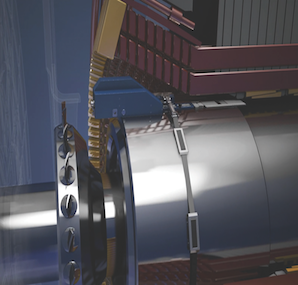
In the past, operators of base load power plants typically adopted a time-based approach to maintenance, generally conducting it at set intervals. While suitable for plants operating in base load, this rigid, interval-based approach is not sufficient for the way plants are operated in deregulated marketplaces such as in Europe and the United States as well as regions where these plants have to compensate for the increasing amount of intermittent renewable generation.
Many of today’s power plants are now being run in cycling or two-shifting operation and at varying loads. This new operating regime places generators and other key plant components under greater stress and has an impact on equipment lifespan.
Consequently,plantownersneedamuch deeper understanding of the condition of their equipment in order to help improve the availability and reliability of their power plants. Ensuring the earliest indication of generator component deterioration can facilitate cost-effective decision-making and efficiently planned maintenance to avoid costly forced outages and emergency repairs.
To achieve this, operators need to have relevant information to be able to make informed decisions on what type of maintenance should be done and when it should be performed. It is imperative that plant operators know the condition of the generator, the risk of failure, and the criticality of the component.
The condition of a generator can be assessed either offline (machine at standstill) or online (machine in operation). Offline, the assessment can be performed with the rotor in-situ or with the rotor removed. Online, the generator can be monitored periodically, where a snapshot of the machine condition is taken and evaluated. Alternatively the machine can be monitored continuously online to evaluate the information received over a period of time and track any deterioration of evolving issues at an early stage.
Most recently, there have been important developments in the area of robotics for offline inspections while the rotor is in place, as well as for continuous online monitoring, as part of GE’s broader and expanding predictive-maintenance portfolio for worldwide power plant operators.
Advances in robotic inspection
A key area where advances are being made is in the development and deployment of robotic tools to avoid the unnecessary removal of a rotor.
Since the introduction of robotic offline inspection with rotor in-situ, the respective legacy GE and Alstom services businesses had developed many iterations of robots which have been produced to inspect a large number of machine types. That technology development process remained intact following GE’s 2015 acquisition of Alstom Power and the creation of GE’s Power Services business.
Two such tools are the DIRIS® Small robot and a lightweight retaining ring scanner.
DIRIS Small robot
GE has been developing robotic tools for generator inspections since the 1980s. In- situ inspections allow fast and reliable assessment of the generator using robotic equipment while avoiding the time and costs associated with rotor removal.
DIRIS Small is the latest generation of robotic toolingandrepresentsamajorstep-changein generator inspection technology. This robot isthefirstofitskindtobedevelopedforuse in small air-cooled machines with cylindrical rotors. The system enables operators to perform a fast and reliable remote inspection of a turbogenerator unit.
The new small robot has two drive units, one that sits on the rotor retaining ring to perform circumferential movements, and an axial drive unit that extends or retracts a thin, flexible, TeflonTM coated band along the length of each slot. A magnetic probe carrier sits at the end of this flexible band.
The DIRIS Small robot (see picture 1) is a precision tool that sends a probe through air gaps (between the rotor and stator) as small as 9 mm to conduct critical testing of the rotor. The robot allows maintenance engineers to access between the stator and rotor to perform several types of inspections. Visual inspection is the most important method of assessing a turbogenerator’s condition.
One of the probes that can be attached to the DIRIS Small robot includes a small video camera, a light source and a mirror to enable visual inspections of areas that are usually inaccessible while the rotor is in place. As the probe carrier moves up and down the length of each slot section, a video recording is made—both of the stator bore surface and of the rotor body surface.
The visual inspection provides a clear, 360 degree view of the inner stator core laminations, stator wedges, rotor surface and wedges, balancing weights and the inboard ends of the retaining rings.
During the video inspection, service engineers look for things like delamination of the core packets, core overheating, foreign objects, contamination, and, on the rotor, locking of balance weights and centering pins, etc.
As part of the in-situ inspection service, stator core short-circuits also are efficiently detected. The stator core consists of stacked laminations, which are insulated from each other. The aim of this construction is to reduce eddy currents in the stator core. If several laminations are short-circuited, eddy currents will occur and lead to local overheating of the core. If this is undetected and not corrected, it can lead to core burning and result in very costlyandtime-consumingrepairs.
The in-situ low flux test of the iron core laminations is an economic and efficient way to detect breakdown of the interlamination insulation. The DIRIS Small robot uses highly sensitive coils to identify faults. Another major advantage is that the robot uses a calibration measurement with simulated faults, which enables fault calculations to be expressed in power dissipation to produce an estimation of the fault severity.
The DIRIS robots used for in-situ generator condition assessment also are equipped with a wedge tightness probe. Due to natural settling and ageing processes of the wedge and winding insulation material, the wedges can become loose. If a certain amount of tightness is lost, the bars will start to vibrate in the slots, which will lead to accelerated ageing of the bar insulation and subsequent failure of the machine.
The wedge tightness probe is basically an accelerometer and a pick-up that checks the tightness of the wedges in the slots. It is also possible to assess wedge tightness on machines with ripple spring wedges.
Importantly, the stator wedge assessment delivers highly accurate and reproducible results and is therefore an excellent basis for trending the wedge tightness. It enables long-term planning for wedge re-tightening or replacement during a suitable major overhaul.
Inspecting retaining rings (TurboRotoscan)
Although reaching within the generator stator–rotor air gap to perform various assessments is important, it also is essential to check the integrity of the generator retaining rings. The rotor has two retaining rings located on the rotor shaft around the field end winding. These are the generator components that are subject to the highest mechanical stress. Stress corrosion cracking (SCC) of rotor retaining rings made from 18% Mn and 4-5% Cr alloy emerged as a worldwide problem for the industry at the beginning of the 1980s.
These cracks can lead to abrupt failure of the retaining ring in running conditions and irreversible damage to the generator. It is therefore important to perform periodic surveillance, particularly in damp or polluted environments.
Retaining rings of the latest generation are fabricated using 18% Mn and 18% Cr steel. This alloy, with higher chromium content, is less sensitive to stress corrosion under normal operating conditions, but it is nevertheless advisable to perform periodic surveillance on this type of retaining ring.
A lightweight retaining ring scanner, a morewieldy,100kg,versionofearlier700 kg scanners, has been developed to test the condition of the rotor retaining rings. Retaining rings are subject to extreme mechanical stress during operation of the generator, and resulting SCC can lead to abrupt failure of the rings and irreversible damage to the generator.
Specifically, the retaining ring scanner detects stress corrosion cracks at the inner and outer surface of the retaining ring on a wide range of OEM and third party turbo- generator models.
The original retaining ring scanner was dedicated to large steam and nuclear generators. The new lightweight version (see picture 2) has the ability to fit in air gaps between retaining ring and stator as small as 20 mm.
Traditional methods such as dye penetrant testing and ultrasonics require the rotor to be pulled from the stator, which can take days.
The lightweight computer-automated scanner is mounted directly on the retaining ring in the air gap between stator and rotor. It uses phased array ultrasound probes and eddy current testing to detect and characterise flaws in the retaining ring.
The Alinta Energy experience
The ability to look at the retaining rings as well as the rotor and stator without removing the rotor has delivered significant time savings at numerous projects — one of them being at Alinta Energy’s Pinjarra power station in Australia.
At the Pinjarra plant, a generator condition assessment package combined in-situ inspection of the air gap with TurboRotoscan to inspect a Mitsubishi generator.
Robotic equipment was used to inspect the generator air gap by performing visual, low flux and slot wedge assessments according to the standard in-situ inspection service. TurboRotoscan (using the new automated lightweight retaining ring scanner), was included in the offline inspection programme to perform critical ultrasonic checks of the inside and outside surfaces of the generator’s rotor retaining rings.
The project, completed towards the end of 2014, would normally take about 3-4 days for removal of the rotor and another 5-7 days to align and reinstall the rotor. The use of the two robotic tools at Pinjarra allowed the overall inspection time to be cut to less than half the normal time.
Following up on the successful Pinjarra station inspection, GE’s Power Services business and Alinta Energy in March 2016 announced an agreement to deploy the combined robotic in-situ inspection programme to assess the condition of 19 additional generators at seven of Alinta Energy’s gas-fired power plants in Australia and New Zealand. The generators were manufactured by GE, Alstom, Mitsubishi and Brush.
Endorsed by Alinta’s insurance company as a best practice for gas power plants, the robotic tools will alert Alinta Energy to potential generator issues and give the utility time to evaluate its options. The expanded inspection initiative was developed through GE’s legacy Alstompowergenerationbusiness,whichit acquired in November 2015.
“We worked closely with GE’s team and our insurance company to demonstrate the benefits of the DIRIS and TurboRotoscan technologies for ensuring effective generator inspections,” said Gareth Williams, manager, engineering services, power generation, Alinta Energy. “Proving the technology’s reliability was important because the generator monitoring system shows us the current condition of the generator and indicates any issues or early warnings of failures. It also provides us with greater flexibility as the inspection work can be done while the generator rotor remains in place. The biggest win for us was the ability to use this technology on non-GE units and apply it across our whole fleet. This makes such inspections quicker and easier to perform and is endorsed as a best practice by our insurance company, which indicates that most generator claims arise through rotor removal and replacement activities.”
“Predictive maintenance activities are essential to reduce costs and increase gas power plant reliability and efficiency,” said Anders Maltesen, general manager of GE’s Power Services business for the Asia-Pacific region. “With our expanded inspection technologies in our services portfolio, we now offer total plant solutions to operators around the world, whether their equipment comes from GE or other OEMs.” The 19 additional generator inspections at the Alinta Energy sites were scheduled to begin in April 2016 and will continue until 2020.
Health monitoring
While offline inspection is required, there also are tremendous benefits in online monitoring and in particular the adoption of a continuous monitoring approach. GE’s Generator Health Monitoring (GHM) offering is a combination of the two legacy products from GE and Alstom. Through the integration of both technologies, customers can now benefit from an even more complete portfolio of GHM solutions.
With GE’s focus on software solutions, further developments can be expected in the near future.
Periodic online monitoring
Assessing a machine’s condition from the evaluation of periodic snapshots is a useful tool. Using the GOLD® service, stator and rotor insulation conditions can be monitored through partial discharge, rotor shaft voltage and rotor flux measurements to determine whether there is any deterioration. This service includes two visits by a GE diagnostic engineer each year. The collected data is analysed and a detailed report including recommendations provided.
Continuous online monitoring
Continuous online monitoring is a proven way of saving time and money.
A permanently installed data acquisition unit continuously collects data relating to a combination of or all of the following generator parameters: partial discharges; rotor flux; rotor shaft voltage; and end winding vibrations & temperatures.
The fully integrated GHM platform is a modular system with a user-friendly, web-based interface that allows on-site monitoring and regular expert reports.
For an increased level of assurance, a permanent remote data link to a monitoring centre is recommended. The service includes weekly checks by experts, allowing early identification of any evolving issues.
In one example, a team was called in to remove a copper oxide build-up from several flow restricted stator bars. The build-up was found as a result of testing performed during an outage. This resulted in a two-week extension of the outage. An investigation showed that continuous online monitoring would have revealed the problem six months earlier. Early recognition of the issue would have given the plant owner time to organise and put a service team in place to perform a CUPROPLEX® cleaning of the stator bars and cooling water system online instead of extending the outage.
In another case, the GHM system picked up a fault on the rotor insulation, which was slowly deteriorating. Increased monitoring of the machine allowed the operator to run the machine in a manner that would allow it to last until the next planned outage period, when the rotor could be swapped with a spare.
While there are other parties that can perform condition monitoring, GE’s capabilities, enhanced by the Alstom acquisition, as an OEM supplier and service provider for other OEM equipment — as well as an implementer of turnkey projects — enables it to configure, supply, install and service all major power plant equipment and brings another level of expertise to the table. Having such in-depth knowledge of the overall plant offers operators more accurate analysis and evaluation of potential problems.
Furthermore, it offers operators the opportunity to move from time-based to condition-based maintenance.
Future developments
Both offline inspection and online monitoring will continue evolve by using experience gained in the field to update equipment and software. For example, lessons from end winding vibration and partial discharge monitoring are being fed back into the programmes to improve the respective GHM modules and allow enhancements or additional features in the future.
In the area of in-situ inspection, GE is currently focusing on innovations for wedge tightness assessment probes for ripple spring wedging and the next generation of air-gap robots.
Meanwhile, the advent of the Industrial Internet and the growing use of big data analytics is bringing new possibilities to generator condition assessment. GE is implementing these latest advances to move further into the realms of automated generator lifetime management for operators, benefiting from the company’s PredixTM platform for the Industrial Internet and its Asset Performance Management (APM) suite of cloud-based software and services that increase asset reliability and availability while reducing unnecessary maintenance (see pp 20-22). Ultimately, such an approach will help to identify issues faster and speed up the process of generator condition assessment to save plant owners time and money.