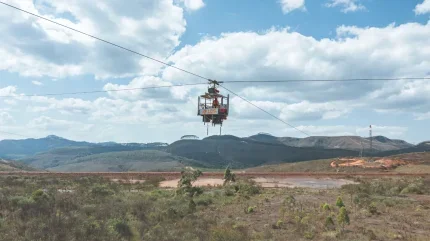
For a significant undertaking in South America, LCS was tasked with developing a cutting-edge personnel safety system utilising winch technology to facilitate secure access to tailings dams surrounding an ore mining area.
To ensure the stability of these earth dams and mitigate the risk of dam failures, routine maintenance and monitoring activities are imperative. Access for personnel to conduct various measurements and repair work at different points is essential. Given the inherent danger of walking in these basins due to the potential for a dam burst, LCS sought a solution allowing individuals to work freely in the danger zone while ensuring immediate evacuation in case of an emergency.
In response to these requirements and leveraging available technologies, LCS pioneered the QXcrane system. This groundbreaking system integrates a cable crane with “SpiderCams,” commonly employed in sports stadiums to capture high-definition video or television footage without ground contact.
Spanning an overall length of 1156 x 556 x 644 x 799 m, the system accommodates a payload of three individuals weighing 125 kg each or material transport of up to 500 kg. Its primary functions include transporting people, ensuring personnel safety, and facilitating the movement of maintenance materials. Comprising four towers standing at approximately 90 to 100m in height, four winches, and operated by a skilled professional, this state-of-the-art system is currently deployed at VALE S.A., with ongoing support from LCS Brazil.
Development of QXcrane
QXcrane has been described as a groundbreaking solution designed for situations where unstable terrain or entering a work area poses life-threatening risks, demanding a safe and efficient access method for workers. In scenarios such as maintenance and monitoring tasks on tailings dams or conventional mining dams, the work area can be perilous for maintenance personnel due to potential dam breaches or earth movements. The QXcrane system provides the ideal answer by allowing safe movement within the work area while ensuring immediate personnel evacuation in case of danger. This system meets the critical need for a personnel safety solution that grants secure access without being situated or supported within the hazardous zone, addressing the challenges of unstable terrains and life-threatening work environments.
The deployment of two QXcrane systems has revolutionized access to previously inaccessible or highly perilous terrains, ensuring the safety of workers in environments deemed life-threatening until now. Operated by an individual in the operator’s basket, workers entering the danger zone are secured with personal safety winches. Connected to towers positioned outside the danger zone by steel ropes, the operator’s basket allows safe navigation and work within the defined area. The system facilitates rapid evacuation in emergencies, such as dam failures or earth movements, with the operator monitoring the entire working area. Maintenance personnel and materials can be efficiently dropped off at any point within the designated terrain, enabling safe execution of repairs, inspections, and remediation work.
Key facts of QXcrane Systems include:
- Access and monitoring of a defined route/area “from above”
- Personnel secured by personal safety winches on the operator’s basket
- Swift evacuation of ground personnel in emergencies
- Lowering of loads or persons at any point using winches
- Suitable for transporting materials, in addition to personnel safety
- Single-person operation in the operator’s basket
- No personnel in the danger zone during system operation
- Operational continuity even if winches fail
- Delivery of an independent recovery system
- Modular design adaptable to site-specific requirements
- Special assembly solution for supports without requiring a large crane
3-D innovation
The patented QXcrane system combines cableway and SpiderCam technologies, resulting in a versatile 3D solution. Four towers, positioned in a rectangle with a maximum diagonal of 1000 m around the defined terrain, support the system. The operator’s basket, connected to the towers by steel ropes, enables safe navigation in all three dimensions within the designated area. Workers in the danger zone are connected to the basket via personal safety winches, granting them freedom of movement while ensuring immediate evacuation in emergencies.
Additional features include:
- Coverage of an area with a diagonal of approximately 1000 m, square or rectangular
- Material transport of up to 500 kg or three persons with 125 kg each
- Winch-controlled lowering of loads or persons at any point within the working area
- Secure operation and navigation in the defined working area
- Perfect fusion of ropeway and SpiderCam technologies
- Navigation in the 3-dimensional space
QXcrane-2D System
For defined work along a route in unstable terrain, the QXcrane-2D system offers an ideal solution. Comprising two towers and an operator’s basket attached to a cable crane, the system ensures safe work and easy operation along the designated route. Workers in the danger zone are connected to the basket via personal safety winches, providing freedom of movement with the capability for immediate evacuation in emergencies.
Additional features include:
- Coverage of a length of approximately 1000 m (with a single tensioning field)
- Material transport of up to 2000 kg or three persons with 125 kg each
- Winch-controlled lowering of loads or persons at any point along the defined route
- Secure working along the designated route
- User-friendly operation and maintenance
Successful delivery
In a significant achievement, Collett has completed the successful delivery of two 160TE inlet valves to the Dinorwig Hydro-Power Station as part of its essential upgrade scheme. Acting on behalf of Rhenus Project Logistics, the Collett Team’s accomplishment signifies a crucial milestone in the ongoing project aimed at extending the power station’s operational lifespan for the decades to come.
Measuring an impressive 5.3m(L) x 4.7m(W) x 3.7m(H) each, a total of six valves weighing 160Te each will be delivered to complete the comprehensive upgrade scheme.
Prior to the deliveries, meticulous planning and preparatory work were undertaken by Collett’s dedicated Project Management and Consulting departments. This involved Swept Path Analysis (SPA) reports, lashing calculations and plans, stability calculations, as well as a comprehensive test run and route studies.
During the test run, a load replicating the exact size and shape of the valves was constructed to ensure the safe transportation of these crucial components.
The first two inlet valves made their arrival at the Port of Penrhyn, situated East of Bangor, North Wales. Under CPA Contract Lift Conditions, both valves were expertly discharged from the vessel using an 800Te mobile crane.
To ensure secure transport, each valve was meticulously lashed onto two 10-axle modular trailers. The journey from the port to the Dinorwig Power Station covered approximately 12 miles, with a travel time of 3 hours.
Throughout the transport, a comprehensive support system was in place, including full police escorts and Collett’s in-house escort vehicles. The loaded trailers were accompanied by three 8×4 ballasted tractor units, two primary and one in support. Special Order BE16 Permits were obtained by Collett’s Permit Team to facilitate the smooth movement of the oversized cargo.
Upon reaching the power station, the two main inlet valves were transported directly to a designated storage area and carefully lowered onto stools. Subsequently, after necessary preparations, the valves were transported into the mountain and offloaded by overhead gantry cranes.
The Dinorwig Hydro-Electric Power Station, located near Llanberis in the Snowdonia National Park, stands as the largest pumped hydroelectric storage facility in the UK. With a maximum power supply of 1728MW and a storage capacity of approximately 10GWh, the station efficiently manages water between the Marchlyn Mawr reservoir and the Llyn Peris Lake to generate power as needed.
This article first appeared in International Water Power magazine.