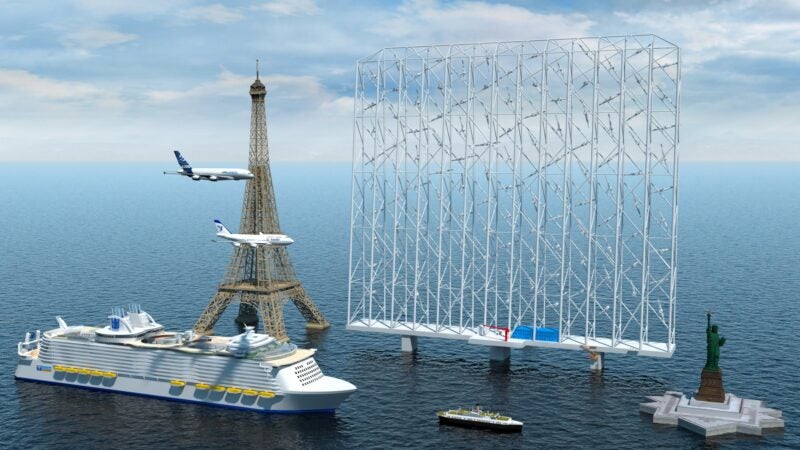
The war in Ukraine has put a sharper focus on the Western world’s dependency on rogue states for fossil fuel. The reality of buying oil and gas from Russia will inevitably precipitate a faster transition to renewables than many in European governments or industry had anticipated.
From there, it follows that wind will play an increasingly important role in accelerating that transition. Harnessing energy more efficiently from precious offshore acreage requires innovative, disruptive technology that can operate in deeper – and windier – waters.
One concept from Norway-based Wind Catching Systems (WCS) is designed to do just that. The company’s Wind Catcher product attracts the eye as well as the wind. The almost 300m2 multi-rotor floater platform system uses 126 individual 30m-wide 1MW turbines, a radical departure from traditional monopile turbines.
WCS CEO Ole Heggheim says the design offers improved efficiency in addition to impressive reductions in operation and maintenance costs. The concept has the potential to produce five times as much power as a single 15MW turbine.
“Standard turbines will pitch up at around 12m per second and hold speed up until about 25m per second, but then they will then pitch out and stop production,” Heggheim says. “Because we have much shorter blades, we will increase production after rated power, which occurs between 17–18m per second, taking out the exponential energy in the wind as it goes up, following the Betz limit [the theoretical maximum efficiency for a wind turbine].”
While standard turbines start pitching at around 700W per metre squared, the company’s Wind Catchers continue to take advantage of the exponential increase, harnessing energy up to 2,000W per metre squared. Additionally, the swept area of one Wind Catcher is 89,000m2, compared with an average 15MW turbine area of 44,500m2, further magnifying production.
One Wind Catcher has the potential to produce 331GWh in a place like Utsira in Norway. In other geographical areas, where there are better winds – such as California or in the Gulf of Lion between France and Spain – it promises to deliver up to 400GWh annually. Compared with traditional monopile turbines, the advantages are clear.
Birth of a new concept
Heggheim and WCS co-founder and Wind Catcher inventor, Asbjørn Nes, moved into renewables from the oil and gas industry, where large floating structures are a staple. As early as 2014, they recognised that wind would need to play a critical role in achieving the renewables targets set down by the European Union and other major economies.
“In Norway at the time, we’d already had a big discussion on the use of onshore and coastal wind power because of environmental reasons and so forth,” says Heggheim. “This being Norway, we already had so much renewable energy, so people were asking, ‘Do we really need this? Do we want these windmills among our nature?’”
These early question marks over the use of turbines on land led to the realisation that the future of wind power was offshore. Even then, nature imposed limitations. “The areas where you can do bottom fix are very scarce,” says Heggheim. “We have been blessed with a lot of areas between Norway and the UK where we have very good wind and very shallow areas.” Unfortunately, there are fewer areas across the world that meet those requirements. “Where you have a good wind, it’s [often] too deep,” he says.
Heggheim and Nes turned their attention to floating wind platforms, a natural progression given their background. However, monopile turbines have obvious limitations compared with floaters. “Eventually, at some point, if you build a larger and larger turbine – it gets higher and higher,” says Heggheim. ”It scales, of course, but at a certain point it’s not going to pay off anymore.”
Resilient, modular and long-lasting
The solution Heggheim and Nes devised was a multirotor turbine on a floating platform. WCS approached the Norwegian engineering company Aibel and the Institute for Energy Technology (IFE) – the Norwegian Institute for Aerodynamics – to test their concept. The positive feedback inspired further development, with patents and formal company registration following in 2017.
“We did a lot of rounds to mature the technology with Aibel and IFE, and funded it to a certain scale,” says Heggheim. By 2020, the potential was clear and the company needed major backers to move it forward. Norwegian companies Ferd and North Energy were brought in as investors and co-owners to inject capital, while Aibel and the IFE were retained as technology suppliers.
Further de-risking in collaboration with Aibel and the IFE, followed and, after logging some 20,000 engineering hours, WCS is now moving into commercialisation. The business model will see WCS provide and oversee the technology, while the engineering, design, construction and installation for customers will be overseen by partners via energy performance certificate contracts.
The resilient nature of the system should appeal to commercial operators with design goals oriented to longer product life cycles that are easier to maintain than monopile turbines, while at the same time generating less waste.
Daniel Engelhart-Willoch, vice president of industry and government affairs at WCS, says the modular design means that a Wind Catcher can be constructed for a 50-year lifetime rather than a 25-year one. “It’s the lifetime of the structure that’s the defining feature – not the lifetime of the individual components that may need to be changed,” he notes.
Other elements of the design aim to address the wind turbine industry’s environmental footprint. The lissome fibreglass blades currently used on monopile turbines are becoming a significant landfill issue. Specialised diamond saws are required to break them down into smaller pieces for transportation and disposal. Already, thousands are being buried each year and given their lack of biodegradability, they will effectively be there forever.
“Our ultimate goal is to produce aluminium blades for 100% [recyclability],” says Engelhart-Willoch. “It’s feasible because we have short blades, but you also have to find an efficient way to manufacture them, so we are working very closely with a big aluminium supplier.”
Increased efficiency and further benefits
Innovations are not limited to the multi-rotor turbine concept. The whole platform has been carefully considered to provide the best use of available space and to remove the need for specialised maintenance, meaning that standard platforms can be used to bring parts and crew. Two on-board elevators will be available for box inspections, maintenance and even quick blade replacement.
“We have an elevator system where you can inspect, maintain and do anything you need to do to the turbine as it is in the sail,” says Heggheim. “Currently, if you have a problem with a blade on a [monopile] floater, there is no technology where you can actually replace the blade from floater to floater. You have to tow it inshore, and that means that you could be out for three to six months depending on the position in the daisy chain – you risk stopping quite a lot of production.”
Engelhart-Willoch also explains that the very large structures act as a self-contained ecosystem – having as much as possible on a single structure means fewer operations, fewer cables and so on.
“We have more than 4,000m2 of available space,” Heggheim says, “So we can certainly be an integrated high-voltage alternating current (HVAC) substation, but also a high-voltage direct current (HVDC) substation when that technology is ready – we don’t need an extra substation. We also have a lot of areas for ‘power-to-x’ and batteries.”
He says that the 50-year life cycle and more efficient operations result in significant carbon savings. The environmental advantages, combined with more efficient use of space, should appeal to government watchdogs when assessing future renewable projects. As each Wind Catcher can replace five 15MW turbines, their acreage efficiency and production improvements are becoming increasingly attractive. “You can see that the regulators want to have more acreage-efficient technology to preserve as much as they can for military purposes, for fishing, for shipping, for everybody,” says Heggheim.
The company is now working with developers on full-scale, reduced-magnitude pilot schemes. “That could be a semi-commercial pilot, but it’s going to be a pilot where we demonstrate the technology and de-risk building at full scale,” says Heggheim.
The project will then move on to a full-scale industrial demonstrator, with one or two Wind Catchers being used on a commercial basis. “I think it’s a great time,” he says. “The world really needs it and we need to do it rapidly. Between the UK and Norway, we have some of the best offshore wind resources in Europe – and we have a responsibility to make them available.”
This article first appeared in World Wind Technology magazine.