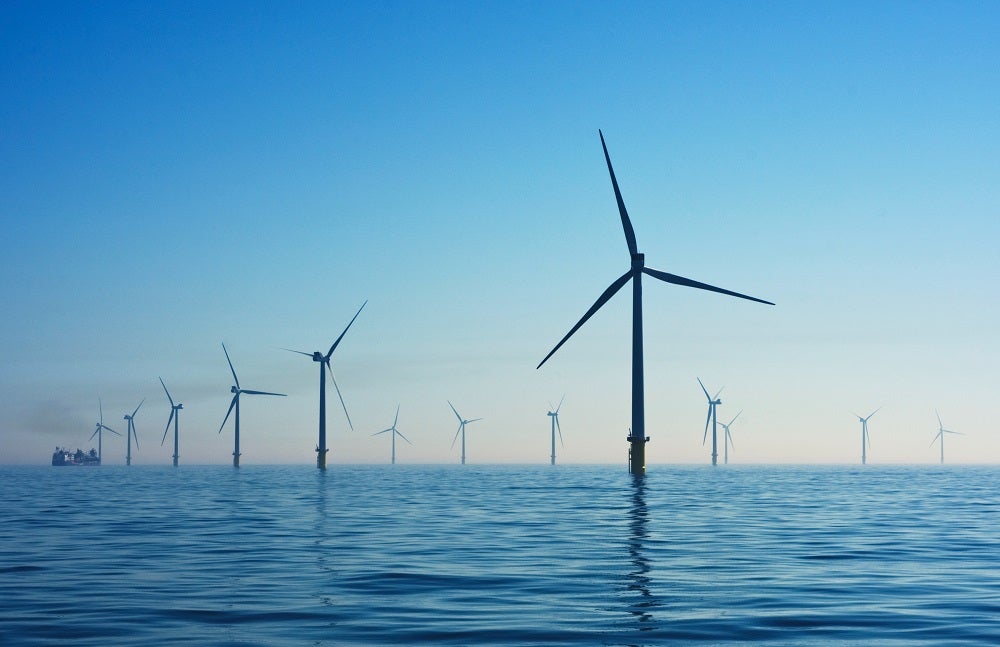
The growth of the internet of things (IoT) has the potential to offer significant advantages to offshore wind power maintenance, with sensor technology able to provide constant data on the functioning of turbines. César Yanes, project coordinator of the ROMEO Project, discusses the use of IoT to move from corrective to condition-based maintenance with World Wind Technology writer Kerry Taylor-Smith.
Wind provides a clean and renewable source of energy, and is relatively simple: the wind spins blades attached to a turbine that turns and generates power.
Except it’s not that simple, as turbines are expensive – around $1m each – and complex pieces of equipment that can include up to 1,000 sensors, actuators, integrating strain gauges, bearing monitors and power conditioning technology.
The turbine can control blade speed and power generation – a sophisticated task demanding numerous cooperating processors closing high-speed loops and implementing intelligent monitoring and optimisation algorithms.
There’s a lot that could go wrong during normal, everyday functioning.
IoT technology can monitor and regulate the operation of offshore wind power turbines
Offshore wind farms are often shown to be calm, tranquil places consisting of hundreds of wind turbines slowly turning in the breeze – if at all. It is a challenge to integrate these turbines so that they all work together in these hard to reach places out at sea. Key to achieving this could be hidden in the latest advances in information and communication technologies, such as the internet of things.
IoT is an interconnection via the internet of computing devices embedded in everyday objects – think fridges, heating systems and similar technology – with the ability to send and receive data.
It extends our current internet connectivity beyond standard devices to any range of traditionally non-internet-enabled devices to allow them to communicate and interact – it also allows them to be remotely monitored and controlled.
This is where IoT could be really useful, as it could be employed to monitor and regulate the operation of infrastructure like offshore wind farms. It can monitor events or changes in the structural conditions that might affect safety or increase risk, schedule repair and maintenance activities, or improve incident management and emergency response efforts.
ROMEO aims to optimise the performance of offshore wind farms, extend their lifetimes and reduce costs
One such project intending to take advantage of these recent technological advances is ROMEO: reliable operations, maintenance decision tools and strategies for high levelised cost of electricity/energy (LCOE) reduction on offshore wind.
The EU Horizon 2020 venture hopes to reduce the cost of maintaining offshore wind turbines using predictive machine- learning algorithms, IoT and cloud computing.
The main objective of the five-year project is to develop a platform for the analysis and management of data gathered from offshore wind power generation plants during their operation and use this data to develop methods of improving the operation and maintenance (O&M) of wind farms.
“ROMEO intends to advance towards the optimisation of operation and maintenance of offshore wind power farms, the lifetime extension of wind turbines and the reduction of the levelised cost of energy,” explains César Yanes, coordinator of ROMEO project for Iberdrola, a Spanish public multinational electric utility company and one of the partners in the project.
To accomplish this, the project is developing advanced monitoring strategies and tools, in addition to analysing the performance of the wind farm turbines in real time. A cloud-based IoT analytics ecosystem platform will include models for detecting, diagnosing and prognosing faults in wind turbine components.
The flexibility and interoperability of the platform will provide an advanced analytics network to promote better understanding of the performance of the main wind turbine components in operation in real time, and for failure diagnostics and prognosis, helping to maximise turbine lifespan and minimising O&M costs.

This will result in an increase in a wind farm’s reliability, and a decrease in the number of failures and the downtime of a wind turbine generator (WTG), an increase in the lifetime of key turbine components, and a decrease in O&M costs by reducing the resources required for annual inspections of turbines.
“Despite significant advances with regards to O&M strategies to maximise the energy yield, there is still room for improvement to alleviate their impact in LCOE and improve cost competitiveness of offshore wind energy,” says Yanes.
This is especially important for offshore wind where O&M costs are higher than onshore, due to distance to coast or harsh weather conditions.
He adds: “This challenge can be partially overcome thanks to the implementation of monitoring systems and diagnosis and prognosis models to optimise the operation and maintenance, maximise the lifetime and better understand real performance of the wind turbines.
“These technologies must be tested under demanding real conditions with the main aim of analysing the improvements achieved in the whole life cycle of the main components of a wind turbine at wind farm scale.”
The O&M information management system developed within ROMEO will be put to the test at three multi-scale offshore pilots: Teesside and East Anglia in the UK, and Wikinger, an offshore windfarm in German waters.
IoT technology could help wind-power operators employ more efficient maintenance strategies
ROMEO hopes to make a significant reduction in O&M costs by decreasing the number of inspections and unexpected major correctives, helping to analyse the possibility for lifetime extension of wind turbine components and the substructure.
“The added value of the novel O&M solutions/concepts will be the capacity to understand the operational behaviour of key components of a wind turbine and its substructure,” explains Yanes.
The hope is that the assembly of the cloud, IoT and machine learning could transition wind turbine maintenance from a calendar-based, corrective maintenance agenda to a conditioning schedule by analysing the real-time behaviour of turbines.
Key failure modes such as fatigue, corrosion or wear have been analysed in order to evolve from the current calendar-based maintenance into condition-based maintenance, allowing better planning of activities.
Yanes adds: “Within the renewables business there is a clear trend towards the transition of maintenance strategies.
“The old-fashioned strategies (corrective and preventive) consist of planned scheduled maintenance, where maintenance is performed based upon predefined scheduled intervals or when a corrective action is needed. These strategies do not consider the real status of components and may carry inefficient resource allocation relevant in specific sectors such as offshore wind energy.”
With condition-based maintenance, repairs are performed only after certain indicators show evidence of decreasing performance of key components/equipment, or if an upcoming failure is detected.
This strategy allows maintenance to be carried out on an as-needed basis, allowing the best planning of activities reducing logistic and material costs while increasing availability. It also allows the costs associated with maintenance to be drastically cut by minimising the occurrence of serious faults.

“The most usual practice is to follow the fixed time intervals and scope of inspections defined in standards, or local regulation,” says Yanes. “However, there is a clear technology demand for generating low-cost-monitoring technologies that could allow the reduction of the number of inspections and the better understanding of the real behaviour of the structure.”
Such a move should result in a reduction in the number of unexpected major correctives undertaken by identifying faults in both WTG and substructures much earlier, and increase health and safety in the industry by reducing the number of corrective missions required. It will also improve the performance of new and currently operating offshore wind power plants, and therefore reduce the cost of energy.
Siemens Wind Power is experimenting with IoT technology
Siemens Wind Power – one of the largest wind turbine manufacturers – is also hoping to put the power of IoT to good use by incorporating industrial internet-based solutions to integrate its systems. This will allow for faster control within turbines, assimilating it to their control centre for predictive maintenance and business diagnostics.
The firm hopes to optimise power, monitor the health of turbines and react to the environment around them – and this technology means that it can control and monitor a wind farm array with up to 500 wind turbines in real time.
When a storm tears through an offshore wind farm, the control system must decide how to take energy out of gusts to generate constant power and balance the wind load across the turbines.
Real-time messaging allows remote monitoring and troubleshooting of the wind farm’s operation, meaning the turbulence can be managed through the farm, and performance and wear and tear is uniform throughout the site.
“Predictability of individual turbine behaviour is key as the objective is for all turbines to be available for operation when needed, which puts significant constraints on owner operators,” explains Yanes.
“Failure of turbine components should be avoided. Information from sensors and systems from offshore wind farms is key to provide insights to detect, diagnose and prognose failures.”
In order to analyse such vast amounts of data, an IoT cloud-based platform will allow the data storage, and the execution of the physical and data-driven machine-learning models, and will deliver the results to an O&M platform to support decisions, believes Yanes.
It is clear that technological advances being made in computing and the internet have a huge role to play in energy generation of the future. The IoT can enable a company to monitor its wind turbines and their health, allowing it to switch to a condition-based maintenance schedule where turbines and their structures are repaired on an as-needed basis.
This move offers the opportunity to lower O&M costs, reducing the overall cost of wind energy.
This article originally appeared in the summer 2019 edition of World Wind Technology. The full issue can be viewed here.