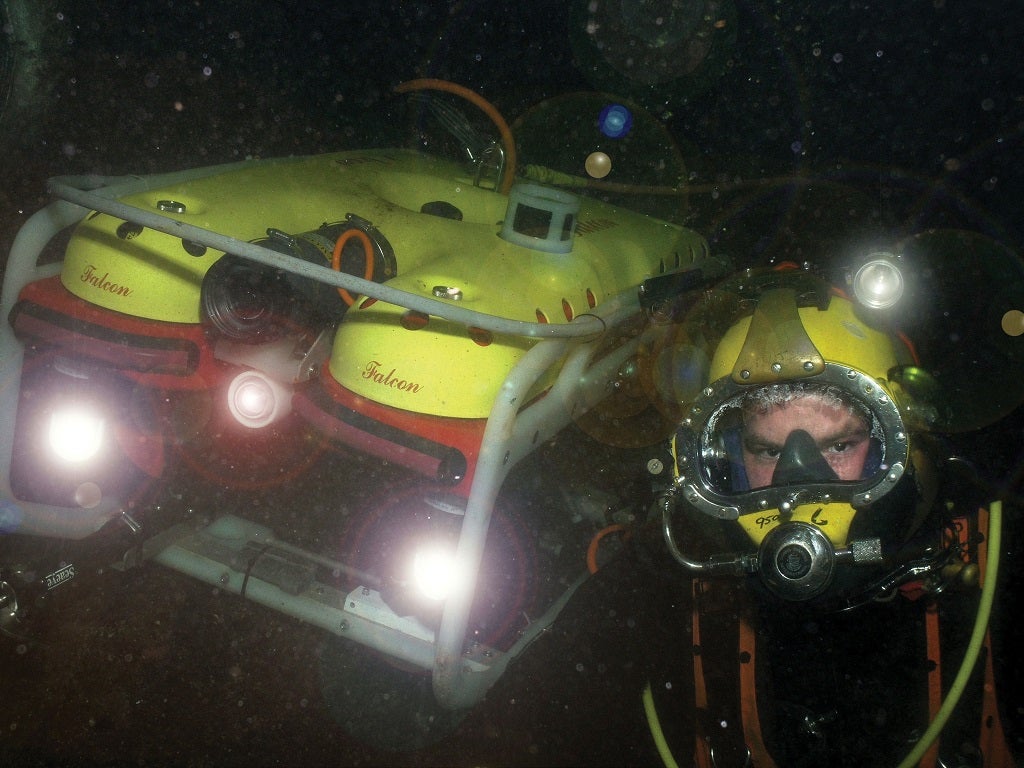
Robotics has become an ever-more critical part in ensuring dam and tunnel infrastructure security, safety and maintenance.
Owners and operators know the technology helps secure the integrity of their facility by providing vital data for immediate and long-term resource management.
Insurers and regulatory authorities, meanwhile, appreciate that the data acquired can help mitigate risk to supply and infrastructure.
Underwater robotic vehicles, specifically, are a sophisticated resource that can gather detailed high intensity imaging, video film and data that will pinpoint, measure and record the exact location of defects, corrosion and obstructions – and remove debris where possible.
Here we take a closer look at some of the areas where the technology is solving perennial challenges in the hydropower sector.
Robotics and dam safety
Working in zero visibility
Robotics systems can work in zero visibility and in strong currents and operate in difficult to access locations including down inspection hatches.
They can also roam along tunnels, through rises and falls and tight bends, for over 20 km.
Dam operators benefit from advances in intelligent control and miniaturisation that have made robotics smaller and smarter and able to handle ever more advanced and sophisticated cameras and sensors, whilst manoeuvring with precision around and inside complex structures and down long tunnels.
They are used globally in a wide range of applications, one such example coming from Thailand.
Across the country’s 14 dams, underwater robotic vehicles, commonly known as Falcons, can inspect for leaks and debris obstruction, along with supporting diver operations and safety.
At each of the dams it can check for debris at the inlet pipes feeding the generators while they are still running – as it has the power and intelligent control to hold steady in the strong flow while observing the status at the inlet and sending back information to the surface.
Solving crack detection
Vital for detailed inspection and light work tasks, Falcons are considered essential for diver support, along with going into places too dangerous for divers.
In the French Alps, in freezing conditions at the Tignes Dam, one of the robotics vehicles is currently working on assessing the integrity of the dam wall, the water inlets and the depth of sediment.

A special sonar is fitted for extra fine 2D imaging and crack detection, along with an Ethernet HD camera with integrated lasers for scale referencing.
Meanwhile, the Guri Dam in Venezuela enhanced its Falcon with an advanced sonar and position location system enabling it to create stable images whilst a self-optimising video enhancement gathered high quality photos as the vehicle swam in various rotations.
At a dam in Italy, the Falcon operator Subsea Fenix recently had a similar problem.
It needed to mount a 3D sonar system high enough above the robotic vehicle to gather all-round images whilst avoiding the vehicle’s chassis obstructing the scan – yet swimming any distance top-loaded in this way, was not possible.
The firm’s solution was to create a retractable structure that lowers the topside mass whilst the Falcon is swimming, then remotely raises it when needed.
The full inspection package gathered accurate visual 2D and 3D sonar data of inlets and outlets, grids, tunnels and ramps.
It not only showed debris and sediment accumulation, but revealed rock fall damage to the rail used to lower the massive outflow closure gate, and rock debris blocking the cable wheels that lowered the gate.

In addition to dam infrastructure deployment, underwater robotic vehicles play a vital role in long tunnel inspection as they can handle turbulent and flowing water during inspection and light maintenance.
This avoids draining the tunnel and makes more frequent inspections easier.
Diver safety
Underwater robotic vehicles come in various sizes, power and resource configurations.
Advanced intelligent distributed control architecture, matched to precise power control, gives the operator not only precision manipulation of the vehicle, but allows data gathering technology to be added and changed as needed.
Sophisticated systems architecture of this nature can also more readily accommodate technology advances, making the vehicle as future proof as possible.
One of their most important features is general diver support and safety.
A robotic vehicle can preview the point of interest before a dive, take down a safety line, oversee the diver during the mission and transport tools back and forth.
It can also go places too dangerous for divers to operate, such as penstock pipes, tunnels and turbine inlets whilst in operation.