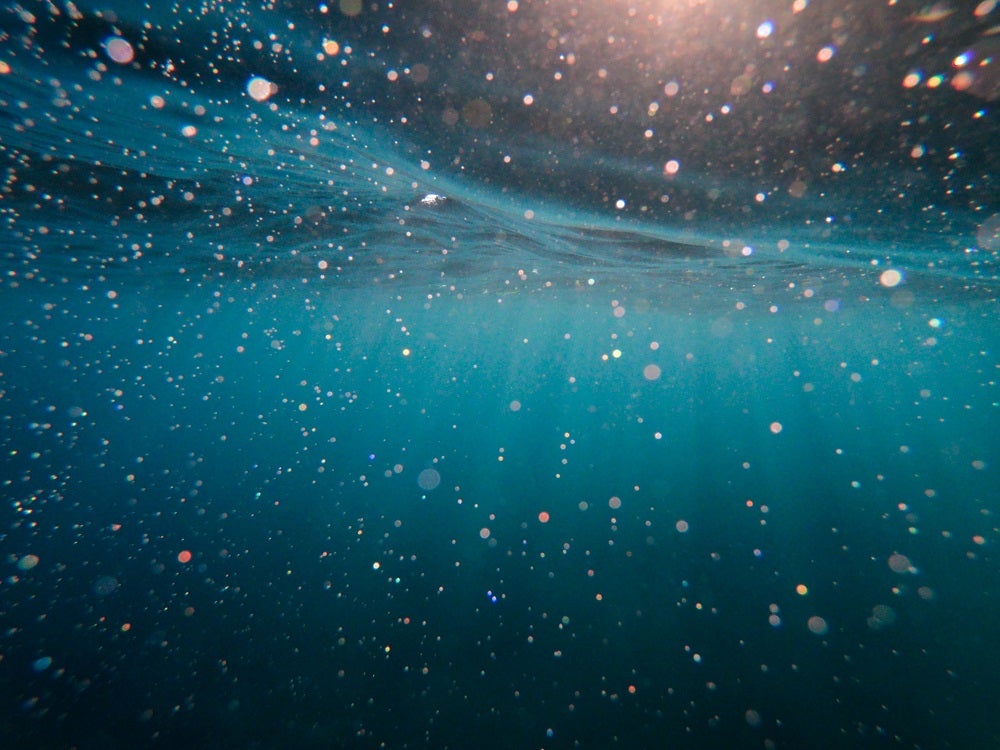
Subsea installation for oil and gas projects is a complex process that requires precision planning. World Expro writer Jonah Baker looks at how specialist companies tackle challenging environments and marshal the skills required – engineering, procurement, construction and installation – to deliver essential infrastructure efficiently and on time.
The subsea environment poses a host of challenges that the specialists who install rigs, flow routers, cables, risers and other critical infrastructure must overcome to ensure that oil and gas flow efficiently and effectively from production assets. As the industry moves further into deep water, these challenges multiply in intensity.
Every project brings its own unique set of technical difficulties. These depend upon a host of factors including environmental conditions, location and scale. In each case, installation must be based on a thorough assessment of the risk factors associated with the environment, in order to avoid poor installation, excess stresses, overload, corrosion, fatigue and cracking risks that could cause subsea systems to fail.
Of all the many skills involved, planning and design are the most important, as they underpin the success of any project and can mitigate many risks before they arise.
The successful subsea installation of any system – rigs, cables, risers and a host of other infrastructure – depends on a detailed understanding of the conditions on the seabed. This is not only because components must be able to resist the stresses that exist in such an environment, but also because the installation phase can have many knock-on effects for the entire network of subsea systems required for any given project.
The installation of components can have a marked effect on the overall complexity of the subsea infrastructure and can influence how accessible a system is for future inspection and maintenance.
The high cost of installation systems drives the need for efficiency and effective planning, but at the same time subsea systems are hard to access and lie in remote locations, so no corners can be cut if the system is to remain fully functional in the long term in deep water environments where they are subject to high external pressure.
Subsea oil and gas installations require careful design and planning
Effective project management begins with a thorough planning process. This is built on an understanding of the demands of the ocean environment, not least to ensure that the subsea installation process does not extend beyond what is necessary.
The subsea infrastructure must be efficiently designed to minimise the installation process and keep costs down, as the cost of installation can often account for well over 50% of the total investment in a subsea project. The high cost of installation comes in part from the challenging environment in which subsea infrastructure must be installed.
Using remote operated vehicles (ROVs) is costly and technically demanding in itself, and operators are reliant on limited visual and sensory data when guiding ROVs to the installation site.
It is crucial, therefore, to understand the geography of the installation site in detail before the installation process begins.

Once a clear picture of the subsea environment is obtained, and the design of the infrastructure is optimised for scale and efficiency, the installation crews need to have the hardware at their disposal to deal with potential risk factors that could jeopardise the project.
The high hydrostatic pressure of the underwater environment places great demands on the equipment and tools that are used, so they must be designed to withstand the rapidly increasing pressure at greater depths.
On top of this, changing weather can have a huge impact. Often, variations in sea and weather conditions can limit the window available for the installation process, even when it has been scheduled for months when the weather is usually calmer.
Planning for weather, strong undersea currents and other environmental factors will rarely anticipate all potential eventualities, so any project must be designed with some degree of flexibility and agility.
Efficiency and flexibility are key for an industry increasingly under cost pressure
In the industry’s current climate, the focus on cost, efficiency and flexibility continues to grow. There is rising pressure on companies to bring projects online faster and less expensively, as the appetite for short-cycle projects increases.
Uncertainty about oil demand in an increasingly carbon-conscious world, and about oil prices going forward, is leading to a slight cooling of interest in capital intensive megaprojects in regions such as the North Sea, with the focus shifting towards projects that can be brought online quickly and at relatively low cost.
One such project is Neptune Energy’s joint venture with BP and JAPEX for the Seagull development oil project, which is set to start next year. TechnipFMC will construct and install the wellheads, trees, an umbilical, flowlines, a four-slot manifold, a subsea wye structure and a subsea control system.
“As the operator, it provides us with the opportunity to demonstrate our capability to safely execute a technologically challenging subsea development,” said Neptune Energy’s UK managing director, Pete Jones, at the announcement of the project.
Seagull is a high-pressure, high-temperature development that will be tied back to the Eastern Trough Area Project (ETAP) central processing facility (CPF) partially using existing subsea infrastructure. It is expected to initially produce around 50,000 barrels of oil equivalent (boe) per day.
TechnipFMC’s focus is the optimisation of subsea fields from the concept stage through to production, and it will need all of its integrated engineering, procurement, construction and installation capabilities get the subsea infrastructure ready for the first oil to flow from the project in 2021.
Subsea 7 has specialised in deep water equipment installation
Subsea 7 is one company that is well aware of the challenges. In July, it was awarded a contract by Equinor for the installation and diving operations on the Europipe II, Heimdal and Statfjord (EHS) fields, located in the Danish and Norwegian sectors of the North Sea.
The contract calls on the company to co-ordinate engineering, procurement, construction and installation (EPCI) capabilities for pipeline end manifolds (PLEM), bypass and tie-in spools for the Europipe II gas pipeline, Oseberg Gas Transport and Statpipe pipelines operated by Gassco.
The first step will involve project management and engineering, including front-end engineering (FEED), at Subsea 7’s office in Stavanger, Norway, with offshore installation scheduled for 2020, 2021 and 2022. Crucial to that phase will be Subsea 7’s state-of-the-art diving vessels, along with its heavy construction and light construction vessels.
The North Sea presents significant technical challenges that could result in high capital expenditure, so the onus is on the installation company to handle the design and delivery phases as cost-efficiently as possible.
At greater sea depths, the length of tiebacks is longer, which could have an impact on flow efficiency, as well as raising the risk of scale deposition and hydrate formulation, which could impact flow assurance. Temperature is also a factor, often falling well below the North Sea’s annual average of 10.5°C.

Partnering with innovative technology providers to perform installations in difficult conditions is a key strand of its strategy.
Global subsea equipment specialist Ashtead Technology recently completed a subsea installation-monitoring project for Subsea 7 as part of Equinor’s Utgard development in the central North Sea. It deployed its deflection-monitoring system (DMS) to capture critical data that could support the development of an accurate subsea template.
The DMS is used for the real-time monitoring of structure deflection, heading, pitch, roll, depth and suction at differential pressures. The data it produces can help to minimise the risk of structural damage during the installation process.
Calibrated to reduce noise from the sensor data and to increase resolution, the system ran autonomously once it had been installed, being remotely controlled using an acoustic data link, radio frequency communications and an ROV hot stab, so that there was no need to have direct involvement of a diver or an ROV.
North Sea embodies many of the challenges facing subsea oil and gas installations
A lot more activity can be expected in the North Sea in the years ahead. Just recently, Ineos, the owner of extensive oil and gas assets, announced a planned investment of £500m ($623m) to extend the life of the Forties Pipeline System, the main oil and gas artery in the North Sea, by 20 years or more.
The project aims to improve reliability for the pipeline, through which around 40% of the UK’s oil and gas is transported.
While this region embodies many of the challenges that subsea installation experts must overcome, projects are under way across the globe, many of which must tackle longer tiebacks, deeper water and many other unique problems.
Constant research and testing of components and processes is required to ensure that these problems are solved in the most cost-efficient manner, hence the industry’s investment in facilities such as HARSH Lab.
Launched last year by Basque research and technological development centre Tecnalia, Europe’s first floating laboratory for testing in a real offshore marine environment will be able to test materials and components in three exposure areas – atmospheric, splash and immersion – which will enable the performance of umbilicals, risers, handling and anchoring systems to be evaluated.
Data on components will no doubt inform future subsea installation projects, helping them to reduce cost and time to market. Using this data well, however, depends on the project management and installation skills of the subsea specialists.
This article originally appeared in the winter 2019 edition of World Expro. The full issue can be viewed here.