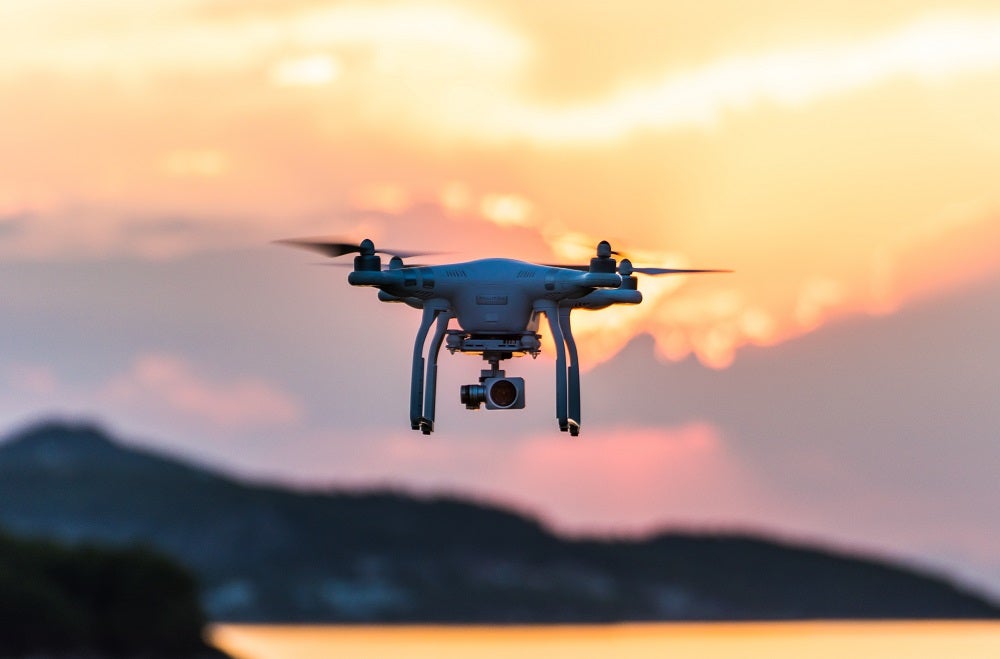
Unmanned aerial drones can offer a range of benefits to oil and gas firms, from lessening the risks to workers in hostile environments to cost-effectively gathering a host of actionable visual data from perspectives otherwise difficult to achieve. Here, Patrick Lohman – energy vice president at North Carolina, US-based commercial drone specialist PrecisionHawk – gives his insight into how oil and gas operations could reap the benefits of this increasingly-valuable technology.
Even in an uncertain economic environment, oil and gas companies can gain a competitive advantage through improving asset management and integrating drone-based data collection, processing and reporting into operational systems.
Because accurate asset management requires sufficient and actionable awareness, flying drone missions to conduct inspections and inventory assessment reduces work stoppages and increases resource efficiency.
The result is increased uptime, improved worker safety and higher profit margins.
Drones can help oil and gas operators overcome safety challenges associated with infrastructure inspections
Oil and gas infrastructure can be difficult to review on-site, and the process of conducting manual inspections can be dangerous, even fatal.
Between 2003 and 2013, the Centers for Disease Control and Prevention (CDC) found a 26.7% increase in the number of work-related fatalities in the oil and gas extraction industry.
Of the 1,189 deaths reported in that time, more than half were employed by companies that service wells and well pads.
Sending roustabouts on trucks to inspect equipment and inventory assets introduces unnecessary risk – the larger the stand-off distance a technician has while inspecting assets, the lower the risk of injury or fatality.
In response, some companies have turned to helicopter missions. Yet these are dangerous in their own right, often impacted by bad weather, cloud cover, and the challenge of a pilot maneuvering the large vehicle around an asset to provide a visual from a multitude of different angles.
Drones can collect hard-to-gather actionable visual data
Beyond these risk factors, manned inspection methods are time-intensive and rarely provide actionable visual data that can be analysed to predict and pinpoint problems.
The collection of useful information requires timely and accurate geospatial data, which is often hard to gather due to the location challenges that oilfields and pipelines present.

Drone operators fly hardware that is purpose-built for accurate data collection in rugged terrain, wet environments, and high-wind conditions.
A typical PrecisionHawk sensor payload – the data-collection hardware equipped to a drone – includes thermal, infrared and LiDAR sensors, a methane-detection laser and optical gas indicators.
Drones can add value across the oil and gas value chain
A company’s asset inspection process is a critical component of its value chain. Every professional, procedure and tool involved must add value in order to achieve an optimal outcome.
Flying drone missions increases resource efficiency at each stage of the value chain. Successful deployment of a drone-based inspection strategy relies on a comprehensive understanding of current systems, and the integration of the tools available to companies through proper implementation.
These missions can add value across the lifecycle of an oil and gas asset, including during site selection, pre-construction, progress monitoring, pre-purchase evaluation, asset management and inspection, and the decommissioning of assets.
And because a drone flyover can be less expensive than manned aircraft inspections, infrastructure can be scanned for issues more frequently, ensuring that repairs and maintenance are scheduled more economically.
Flying ‘beyond visual line of sight’ offers many benefits
Given that pipelines and oilfields occupy vast terrain, some drone-based inspection programmes only optimise maximum efficiency when pilots fly beyond visual line of sight (BVLOS).
When manpower is scarce, as companies experienced through the oil and gas crisis in 2014, it’s more resource-efficient to deploy drones to conduct well pad inspections.
One company found that drones reduced inspection costs by 66%, from $80–$90 per pad to $45–$60 per pad.
It’s not just about the cost per inspection – by flying BVLOS, the ten well pad inspections a technician could inspect in one day becomes 100 or even 125.
The real economic benefit to flying BVLOS drone missions is not cost reduction – it’s in having technicians available to focus on uptime to drive or maintain revenue production.
Effectively managing resources is the key to maximising return on investment – a drone-based inspection programme protects workers, optimally allocates resources, and provides precise, actionable data to manage assets.