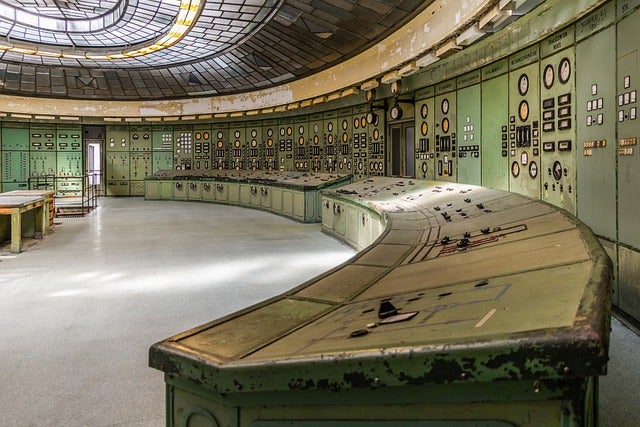
DTE Energy’s Dearborn Central Energy Plant (CEP) generates electricity and distributes chilled water, hot water and steam to buildings at the Ford Dearborn Research and Engineering Campus (REC). The CEP consists of a combined heat and power (CHP) plant and a chilled/hot water plant for combined power and steam generation. A wide array of technology is deployed to make it possible for the entire CHP plant to be largely manned by one person per shift to take care of maintenance and operations.
“A single person looks after the entire 34 MW, 87 000 square foot facility 76% of the time,” said Kevin Siess, Regional Operations Manager at DTE Energy. “Our plant operators are also our maintenance staff who can monitor the plant and its control systems while they are doing their rounds.”
Integrated systems
The CEP opened on the first day of 2020. Although its design included plenty of systems to streamline plant operations, COVID-19-inspired lockdowns provided the impetus to further innovate in plant monitoring. What has been assembled is a fully integrated array of software and control solutions:
- Vital Technology Services (VTS) HardHAT system provides the plant’s digital twin, front-end of 3D modelling, inventory and computerised maintenance monitoring systems (CMMS).
- MapEx Software provides first-principle physics-based modelling and heat balance that feeds into advanced pattern recognition (APR) software and machine learning-based analytics.
- SureSense APR (advanced pattern recognition) software by Expert Microsystems.
- Solar turbine’s Turbotronic control system for sequencing, control, and protection of the gas turbine package, and monitoring of associated auxiliary systems.
- A Rockwell Automation historian and Allen Bradley PlantPAx distributed control system (DCS) to control the entire CEP.
“Around 12,000 data points are gathered up in one place from the various control and software systems and all of it goes into the historian,” said Siess. “That data is all available in VTS.
We get trip alerts automatically on high-value critical equipment such as the gas turbines, heat recovery steam generators (HRSGs) and feedwater pumps.”
A lightweight 3D model is viewable by plant personnel on remote devices during maintenance rounds. Smart tags on components and equipment show up in the 3D model to provide abundant digital data. The system offers a single source of truth for document control, DCS, historian, CMMS, plant instrumentation (PI) system, inventory software, and more. In addition, drones are used to supplement maintenance checks. They incorporate image recognition technology that can detect hot spots and puddles as well as methane, steam or other leaks.
“Drones are a lot more efficient than putting hardwired AI/IOT sensors everywhere,” said Siess. Mathematical algorithms identify patterns in historical data. These patterns are trained into the system to detect changes in ongoing plant operating data that arise from a developing problem.
Turbine monitoring
The combined cycle facility includes two 14.5 MW Solar Titan 130 gas turbines and a 5 MW condensing steam turbine from Siemens Energy. As Ford does all its engine testing at a nearby dynamometer lab, there is almost no tolerance for electricity interruption.
Siess gave an example of how the CHP monitoring systems help prevent unscheduled outages. After a recent scheduled outage, SureSense generated an alert about a slight increase in oil temperature exiting shaft bearings. The seal had registered a temperature of 219°F since plant opening. Soon after the outage, it rose by 10°F. While still 40°F below the alarm level, the software flagged the condition as abnormal. The operator alerted Solar Turbines, which is monitoring the seal and plan to replace it during the next scheduled outage unless the problem worsens.
“A sudden shift in oil temperature can lead to more varnish potential and make the unit and ancillary cooling equipment work harder,” said Siess. “It is vital that we catch issues at an early stage to prevent a major failure.”
Another example concerned a problematic gas compressor. Drilling into data within the HardHat system, the operators discovered a slide gate out of calibration that caused unnecessary recirculation of gas. This increased parasitic load and system wear. It was repaired before serious problems arose.
Similarly, APR detected a thermocouple deviation in the gas turbine exhaust that hadn’t yet shown up in the turbine control system. A shutdown was ordered to rapidly clear the fuel injectors. As a result, a GT trip or outage was avoided.
Preventive maintenance (PM) is preferred to calendar-based maintenance schedules that can result in over-greasing of parts or unnecessary replacement of components.
The CMMS know the number of hours equipment, components and systems have run and sends alerts when it is time for inspection. All rotating equipment oils are sampled and analysed quarterly to make sure they are free of impurities.
HRSG operation and maintenance
The HardHat system aids operators in monitoring all aspects of running and maintaining two HRSGs from Rentech Boiler Systems. It keeps track of a great many parameters to ensure everything is running smoothly. For example, the high-fired
waterwall, O-type HRSGs should provide up to 225 kilo-pounds per hour (KPPH) of 200 PSIG saturated steam, which is vital to Ford operations. In addition, another up to 90 KPPH can be consumed in the steam turbine as part of combined cycle power generation.
“Advanced pattern management and 3D modelling enable operators to keep a close eye on the maintenance of HRSG steam production as well as hot water and high-pressure steam metrics,” said Siess.
Operators can view each HRSG in the 3D model and drill down into systems and components as needed. The CMMS push out maintenance actions coming due. Parts are flagged that need to be maintained or replaced, based on usage.
Take the case of a temperature transmitter in the HRSG’s feedwater header. The operator can click on the part to review documentation, part numbers, past maintenance records, examine any required safety checks, view instrument and sensor readouts and review work orders (a flashing feed control valve on the screen would indicate an active work order). At the end of a shift, the new operator can open the system to see any work orders opened and resolved that day, which reduces the need for a lengthy turnover of duties.
A recent incident involved power loss to the HRSG. The system automatically generated alerts. The investigation detected a power supply drop-off to the PLC, which then tripped the HRSG.
“We picked up this problem in the HRSG and resolved it within 90 minutes,” said Siess. “As the asset database in HardHat has information on all part numbers, vendors and specs, it saves us a lot of time in routine maintenance.”
The Rentech HRSGs include supplemental firing. By raising the gas turbine exhaust temperature via supplemental firing, steam production can be increased by approximately 300%. Operators control supplemental firing from the booth and can keep a close eye on temperature, pressure and steam output numbers to ensure everything is operating as intended.
“The key is to not to waste time and resources in looking for information or engaging in unnecessary activities – everything is prioritised and at the operator’s fingertips,” said Siess.
“This kind of automation is increasingly needed as the power generation labour pool is rapidly shrinking.”
Building confidence in automation
A system like this isn’t going to go in one day and hey presto, perfect operation from there on out. Siess laid out the trajectory of steady improvement the facility has undergone: nine unit trips in 2020; five in 2021; and two in 2022. Hours of unplanned downtime fell from 50 hours in 2020 to only four in 2022.
The facility schedules a spring and autumn outage to take care of major maintenance actions and inspections. During those windows, Solar Turbines comes on site as part of a long-term service agreement.
Each gas turbine and HRSG is taken down for two to three days. While one unit is being serviced, the other continues to operate to ensure the flow of steam to Ford is never interrupted. Features built into the Rentech HRSG provide further assurance of steam flow. A fresh- air-firing capability utilises a forced draft fan so the HRSG can be operated when the gas turbine is offline. The fan draws in ambient air and the duct burner provides heat to generate 80 KPPH of steam. A louvre-type diverter valve installed between the HRSG and the turbine facilitates steam/electricity switching. If there is no current steam demand, flue gas from the turbine can be diverted up a bypass stack and not through the HRSG to generate only electricity and not steam.
Siess added that automation enables DTE to untether the operator from the chair to go on maintenance rounds for 45 minutes or more without anyone in the control room. Data on plant operation is available via mobile device, which brings the control room into the field. Alerts are issued if anything needs attention.
“The right technology gives people enough confidence in automation so they can walk away,” said Siess. “Our operations staff are now comfortably performing 80% of all maintenance activities.”
This article first appeared in Modern Power Systems magazine.