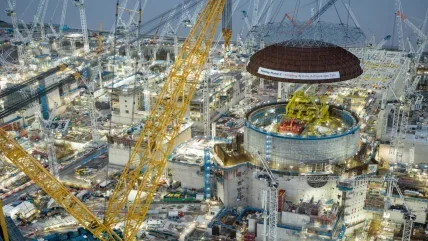
Nuclear power plants offer low carbon generation, but they are large pieces of infrastructure and as such they have to take account of carbon emissions that arise from sourcing their materials and during construction, operation and decommissioning.
Among options for power generation, nuclear’s life-cycle carbon emissions are similar to those from offshore wind, according to figures from the International Panel on Climate Change (IPCC). It estimates emissions for those two sources as 12 t/MWh. There is very little difference between them and the source with the lowest emissions, onshore wind, which has emissions of 11t/MWh. Nuclear’s carbon toll is half that of hydropower (24t/MWe) and between a half and a fifth that of solar PV, which can have lifecycle emissions as high as 45t/MWh.
Of course, all these emissions levels are tiny compared with fossil fuel generation. Coal life cycle emissions are 820t/MWh and methane gas emissions are 490t/MWe in the same IPCC ranking. (The IPCC assessment is in fact in ‘equivalent tonnes of carbon dioxide emissions’, because it takes account of different greenhouse gases, whose effect may be many times that of carbon dioxide.)
But this number is not fixed for all time. The race to a decarbonised society affects companies in the supply chain just as it does power generation companies themselves. This allows all low-carbon sources to move closer to true zero carbon as successive generations are built.
What does that mean for nuclear? The UK’s PWR new-build programme provides a useful timeline for comparison.
Carbon life cycle assessment
‘First concrete’ for Hinkley Point C took place in March 2017, although civil works had been underway for some time before then. Work on its successor, Sizewell C, is expected in the middle of this decade with a construction period that would take startup to the second half of the 2030s. During these two decades, big steps are being taken to reduce the carbon load for its components.
In 2021 NNB Generation Company HPC Ltd, Hinkley Point C’s owner, released a life cycle assessment of the carbon emissions from the plant along with other impacts – Life cycle carbon and environmental impact analysis of electricity from Hinkley Point C nuclear power plant development, prepared by Ricardo Energy and Environment with third party assessment by WSP Environmental. It found that “the core construction stage is the highest contributor per generated kWh for the majority of the environmental indicators assessed. Within this core construction life cycle assessment (LCA) stage, it was observed that in general, the highest contributing substage was that of the materials required to construct the [Hinkley Point C] HPC development, particularly those associated with the steel and concrete used.”
It went on to say that 77% of the global warming potential (GWP) value associated with construction was from energy and material usage. The energy needed for construction contributed 30%, which was split 50/50 between grid electricity and diesel. Some 47% came from the embodied carbon of the construction materials required such as reinforcing steel (15%) and concrete (just under 10%). Transportation of construction materials and earthworks to the site and of construction wastes offsite was responsible for 12% of the core infrastructure construction’s GWP.
Improving primary resource performance
Average carbon emissions from the UK grid electricity required for construction have already fallen significantly since 2017. In that year the UK government published a greenhouse gas ‘conversion factor’ for grid electricity, used by companies for annual reporting, of 0.35kg/kWh. In 2023 the government’s figure, based on the grid electricity mix in 2022, was down by more than a third, to 0.21kg/kWh. Diesel generators are not supplied from a network but the trend is in the same direction. For example, one company that provides rental diesel engines, Aggreko, set out in 2022 a pledge to cut the amount of diesel used by its organisation by 50% before 2030. It said, “Specifically, we intend to phase out offering diesel with our fuel management services from April, instead solely providing hydrotreated vegetable oil (HVO)”. It is also investigating the use of other potential low-carbon fuels such as methanol and hydrogen in fuel cells for future applications where diesel engines would previously have been used.
What about the carbon emissions embodied in the large material requirements? The concrete and steel sectors both have ambitious targets to reach Net Zero by 2050, but progress in the next decades requires some major technology developments.
Hanson is a major concrete supplier and counts Hinkley Point C among its customers. Cement is a key ingredient in concrete and Hanson’s cement business is responsible for 90% of all of its carbon emissions. Some of this arises from the energy used but around 70% is from the chemical processes involved in cement production. As a result, the only way to stop the carbon dioxide being emitted is carbon capture and storage (CCS). Hanson’s parent company Heidelberg Materials will capture and store 10 million tonnes of carbon until 2030 through CCUS projects it has in development. In the UK, Hansen has three projects:
- It is proposing to invest around £400m (US$506m) to build CCS at its Padeswood cement works, near Mold in north Wales. It would transport the captured carbon via the HyNet North West underground pipeline and store it under the seabed and it is targeted to enable Hanson to produce net zero carbon cement by 2027.
- A project at its Ketton cement works in Rutland will use a solvent to selectively capture the CO2 produced. This may require less energy than some other carbon capture technologies. The feasibility study is now complete and the demonstration unit is expected to be installed later this year.
- Along with Heidelberg Materials’ R&D team, at its Ribblesdale cement works Hanson demonstrated enforced carbonation of recycled concrete paste within the plant’s existing wet scrubber. This removes emissions from the production process and produces a secondary material that can then be used to replace virgin limestone in cement and concrete production.
These developments are expected to allow the company to move to low-carbon concrete by 2030. In the meantime, it has been able to cut emissions with changes to its concrete composition. The EcoCrete range replaces some of the cement in its concrete with Regen GGBS (ground granulated blast furnace slag). As well as reducing carbon emissions, using GGBS has increased the long-term durability of structures, does not require quarrying and reduces the need to dispose of slag.
The Ricardo report noted that there was a difference between ‘standard’ concrete and high-density nuclear concrete because it requires heavy aggregates such as magnetite or iron shot. But (in accordance with the fact, noted above, that cement carries a large party of the carbon load) it found that for the core construction stage, and thus for the total generated kWh, “generally, the sensitivity analysis indicates that whilst substituting the dataset for normal concrete with that of heavyweight concrete in the key core main HPC infrastructures, the model is not highly sensitive to this change.”
British Steel is also a major supplier to Hinkley Point C. Its decarbonisation strategy aims to reduce carbon emissions by 82% by 2035 and produce net zero steel by 2050. Its low-carbon roadmap was launched in October 2021. Some emissions reductions are achievable with management actions such as recycling, and in its most recent decarbonisation action plan British Steel says it has increased its recycled content from a historic average of 13.8% to an average of 24.7%. The roadmap also includes feasibility studies into integrating electric arc furnace steelmaking and replacing methane gas with hydrogen in operations that require direct heat.
Other steel companies are also reducing their carbon load. In a recent blog Dr Debashish Bhattacharjee, VP Technology and R&D at Tata Steel, said the company had recently conducted a successful trial injection of hydrogen gas in one of the blast furnaces at its Jamshedpur Works. This is the first time in the world that such a large quantity of hydrogen gas was continuously injected into a blast furnace. The trial demonstrated the potential for a 7-10% reduction in carbon emissions per tonne of crude steel produced. He said: “By studying the data, we now know what happens when we inject massive amounts of pure hydrogen into the furnace in terms of gas volume, reaction rates and temperatures”.
Global Energy Monitor (GEM) believes that the steel industry has begun a ‘pivotal’ shift: its recently released report says 43% of planned steelmaking capacity is now based on electric arc furnaces, with 57% using coal-based blast furnace-basic oxygen furnaces (BF-BOF). Although electric arc technology represents less than half of planned capacity the ‘pivot’ from last year’s report is significant: at that time just 33% of planned capacity was set to use electricity, against 67% based on fossil-fuelled blast furnaces. As with the cement and concrete sector, CCS is a key technology in reducing emissions.
The impact of delivering power
The embodied carbon across the electricity sector can be reduced by low-carbon variants of the major materials. High on the list for decarbonising the system as a whole is cutting emissions in the electricity transmission system, from the power plant switchyard through to the end user. Again, these types of losses affect all forms of power generation that are connected to the electricity network.
The Ricardo report on Hinkley Point C showed that power generated at Hinkley Point C will carry less of a carbon burden than the electricity delivered to the user.
It said: “Almost half of the total GWP value associated with a delivered kWh of electricity from HPC, comes from downstream impacts… this encompasses the infrastructure and operational requirements of the grid itself and includes the impacts of materials needed such as metals for pylons and emission leakages of SF6 insulation (a powerful greenhouse gas)”. That is compounded by losses on the transmission and distribution network, which add 6% to the total emissions because that loss has to be ‘topped up’.
A major problem with decarbonising the delivery phase is sulphur hexafluoride. This gas – generally abbreviated to its chemical formula, SF6, as referred to in the Ricardo comment above – has been routinely used in substations and switchgear over recent decades, as well as in smaller sealed items of electrical equipment. It provides an electrically insulated environment for substation equipment, which would previously have relied on an ‘air gap’, to avoid short circuits and subsequent local blackouts.
Because its insulating properties are so much better than air, electrical arcing is about 100 times less likely in SF6 than in air. As a result, sealing the switchgear in an SF6 atmosphere means the various components can be placed much closer together, so the volume required by the substation is smaller. The footprint of a substation with gas-insulted switchgear is 30-40% smaller than that an air-insulated version. This gives network and building designers more options on where to place electrical equipment and it is important in areas – such as cities – where space is expensive. After all, eventually, the space cost of substations feeds back to user bills. In addition, air-insulated switchgear is generally exposed to environmental conditions – dust, rain, or even animals – which makes it vulnerable to failure.
But SF6 carries a sting: it is the single most damaging greenhouse gas. Each tonne is equivalent to 23,900 tonnes of carbon dioxide. It is (with similar gases) the biggest contributor to transmission companies’ business carbon footprint (BCF) because on occasion the gas leaks.
The electricity supply industry is almost the only use of SF6 and emissions to air have increased noticeably since it entered common use. Legislators are cracking down. The European Union, for example, had previously excluded the electricity industry from restrictions on so-called F-gases imposed in regulations in 2014. But revised regulations will affect the electricity sector. Meanwhile, as the cost of carbon increases the electricity industry has a greater incentive to halt leaks. Over time, new options will replace SF6 in network equipment but the use of alternatives has been slowed as technology is developed. One technical route to replace SF6 is largely based on air but has a proportion of so-called per-and polyfluoroalkyl substances. Abbreviated to PFAS, these have caused concern over a potential threat to health – dubbed ‘forever chemicals’ in the press – and their use is set to be strictly limited, at least in the USA and the EU, where new regulations are progressing through the respective legislatures. A second alternative is not yet commercially available at high voltages. However, by the time a new plant at Sizewell is installing its switchgear and exporting power, it should be able to guarantee lower-carbon delivery of electrons across the network.
Between two reactor timelines, for Hinkley Point C and Sizewell C, initiatives to decarbonise are taking effect across the electricity industry and across the economy. They are not unique to the nuclear industry – but nuclear can benefit from the changes in telling its low-carbon story.
This article first appeared in Nuclear Engineering International magazine.