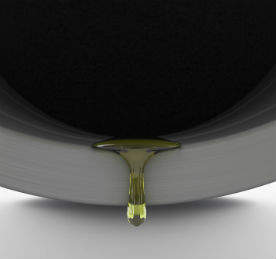
The era of easy oil and gas is over. With most new discoveries requiring high capital investment, many operators in the Norwegian and UK sectors are now contemplating continuing production from mature fields for up to 25 years.
Enhanced oil-recovery techniques can improve mature field output substantially, but continued production at minimum cost relies on keeping existing assets, such as cranes, platforms, pipelines, flowlines and risers, working well beyond their initial design life. Lifetime extension (LTE) projects are the way to achieve this.
"Even if repairs and additional inspections are needed, using existing facilities beyond their design life will be economically viable in many cases," says Hesham Abdel Haleem, lead integrity engineer at Wood Group Kenny. "Today’s projects can take advantage of the conservative standards of old assets where parameters like pipeline wall thickness were often overdesigned. The main priority is that safety requirements should not be compromised."
Asset management
Pipelines and their associated infrastructure are particularly important in keeping oil flowing cost-effectively. Using tie-backs to existing pipelines is also the standard way to economically develop and produce smaller new fields in mature regions.
To successfully extend asset lifespan, operators typically employ an LTE study to demonstrate to regulators the technical, operational and organisational integrity necessary to continue safe operation. The starting point is to estimate the current condition of the assets involved. That’s simple to say but, in practice, it involves gathering and then studying data from many sources.
That includes the original design and engineering, procurement, construction, installation and commissioning (EPCIC) documentation, as well as operational manuals. Then there’s condition-based monitoring data, plus other operational data such as pressure, temperature, fluid analysis results, frequency and type of inhibition dosage, and so on.
Engineers must also collate data from previous investigations: ROV or diver general visual inspections, NDT results, in-line inspections (ILI)and stress-strained state inspections. Wading through large quantities of mostly non-essential, outdated data covering the asset’s original design, fabrication and installation can cause confusion and significantly adds to the assessment workload.
"Companies investing in systems and procedures to handle this data efficiently and accurately will have a straightforward LTE study," says Haleem. "However, handling a huge amount of data is not easy and has to be optimised. The key here is quality, not quantity."
A data management plan for LTE and integrity is the way forward. Wood Group Kenny advises operators to develop a template to collect data with the required parameters and documents for each of the systems, equipment and associated components from all the different services or departments involved in an asset’s management.
Collecting only relevant data over the life of an asset minimises costs and speeds LTE projects along. Haleem gives the example of one client that installed an advanced monitoring system. This acquired a large amount of high-quality data that had to be stored and analysed periodically.
"In this case, the actual benefit from it was negligible, so it was an unnecessary task that added to the operational cost," says Haleem. "This emphasises the importance of data management."
With the data in place, engineers can then assess the current asset condition qualitatively and quantatively according to historical and current operating conditions, as well as using inspection data. For pipelines, that means identifying and evaluating threats like corrosion, erosion, subsidence and external damage from dropped objects or other impacts.
Based on failure probability and possible consequences like pitting, local wall thinning, buckling or bursting, they can then highlight the most critical threats to current integrity. As part of this assessment, engineers must establish whether the documentation is of good enough quality to assess condition reliably.
Many factors can produce misaligned and inconsistent information: mergers and acquisitions, computing system migrations or poor quality assurance. Any uncertainty in background data or inspection results could lead to the wrong decisions.
"Quantifying the level of knowledge based on the availability and quality of the background information is the real challenge for LTE," says Haleem. "So far, there are no guidelines for how to conduct it in a quantitative manner."
Future proof
The next stage is to evaluate the risks of each threat for the future LTE period. Information on future pipeline operation or any planned modifications is vital at this stage. For example, a new tie-in might change operating pressure, temperature or fluid condition.
If altered operating conditions will change the original design criteria, then additional engineering studies may well be required. Engineers also conduct gap analysis to detect any changes in industry standards since the asset was designed.
This future assessment takes a probabilistic risk-assessment approach – expert judgment combined with reliability data when available. Corrosion is typically the leading mechanism of deterioration, with 27% of pipeline failures in the North Sea and 40% in the Gulf of Mexico due to corrosion (DNV RP F-116).
"The risks should be evaluated with regard to the operator’s acceptance criteria, which are compliant with the technical authority," says Haleem. "When we face a lack of data, assumptions will be mainly based on the experience of the assessor and the operational knowledge of the particular field, which we call ‘educated assumption’."
These qualitative or semi-quantitative assessment can be sufficient for risk scoring, but engineers also use quantitative calculations that employ probabilistic models to give a rate of degradation for certain critical threats, such as corrosion. The more accurate the probabilistic models are, the more precise the remaining-life prediction will be.
Corrosion is known as a ‘time-dependent degradation’ and may have high uncertainty, hence high safety factors are in place during the corrosion-modelling process to accommodate uncertainty in the operational data and the data on the product chemical composition.
"If no ILI data is available, then the only assessment we can make will be established on the corrosion-rate calculation based on mathematical models," says Haleem. "This will be very conservative and may not reflect the actual condition of the asset."
Life assessment
Increasing the accuracy of pipeline life prediction via better probabilistic modelling of imperfect inspection data is one valuable area of research. One 2014 doctoral paper used stochastic techniques to more accurately predict corrosion growth in oil and natural gas pipelines.
"This is potentially the next step," says Haleem. "However, sufficient good data to develop probability distribution is still needed. Furthermore, evaluation of the stochastic models using uncertain inspection data is a computationally challenging task."
Where valid data is missing, further conservative mitigation actions are often required to assess and assure asset integrity. Those include extra tests and inspections, along with other recommendations such as enhanced monitoring during the future LTE period.
One example is where missing operational data makes it impossible to calculate a pipeline’s corrosion rate. That would require a fresh ILI that could then be compared with previous results to calculate corrosion growth rate and so predict the remaining life. The same process would occur if pipe wall thickness data is incorrect or unavailable.
With the assessment complete, the operator can then work out the current and ongoing costs of supporting future operations – as well as the cost of any further inspections, there is often extra remedial work required to assure future operational integrity.
Typical options include repairing or replacing substandard pipeline sections, introducing a new corrosion-management regime, perhaps by retrofitting anodes, or switching to less demanding operating parameters such as de-rating the pipe or changing the fluid from oil to dry gas.
"If all of these options are exhausted, then the pipeline life cannot be extended and replacement would be the only option," says Haleem. "The cost of replacement, remaining reservoir life and, of course, oil price will all play a role in the decision-making."
As LTE projects increase in number and importance, the industry is focusing on ways to improve effectiveness. Developing cross-industry methodologies would be one way to speed up and improve the data-collection process during assessment.
"Wood Group Kenny is looking to develop a proprietary system for data collection where evaluation of data quality and availability would be based on the engineers’ expertise and judgment," says Haleem. "There is no artificial intelligence that can replace engineering judgment in this aspect yet."
Standards and regulation also evolve. Introduced in 2011, ISO/TS-12747 offers guidance in assessing the feasibility of extending the service life of rigid metallic pipelines. Norway’s GL122 standard also gives guidelines for LTE assessment and documentation.
In 2015, the Norwegian Oil and Gas Association issued a guideline referring to NORSOKS standard. Norway’s SINTEF also released a report in 2010 covering ageing and life extension. The UK Health and Safety Executive launched its KP4 initiative in 2010 to determine how well asset-integrity risks associated with ageing and life extension are being managed in offshore oil and gas. So far, this has involved numerous onshore and offshore inspection of duty holders’ management systems based on a variety of specialist templates.
"We need updated regulations to specify what to assess and, where possible, what the acceptance level of different threats is," says Haleem. "At the moment, it is left up to the assessor’s judgment to demonstrate the integrity of the asset and the Safety Authority criteria. We also need a plan for data management throughout an asset’s life cycle for LTE, integrity and decommissioning."
Above all, successfully extending asset lifetime depends on excellent maintenance, along with ongoing intelligent monitoring and integrity assessment. Keeping the asset in optimum condition and collecting the data to prove it gives the operators the best chance of a long profitable life for their infrastructure.