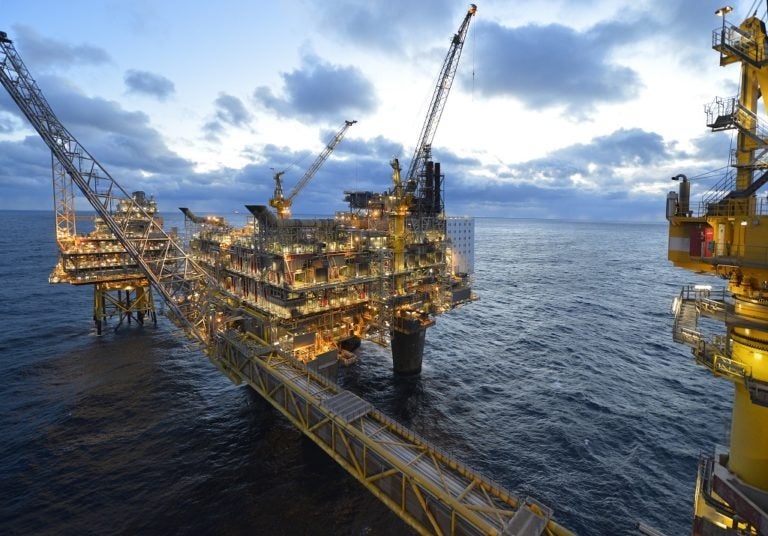
Towards the end of last year, Norwegian energy giant Equinor launched the world’s first fully automated oil and gas platform, advancing the debate over whether technology should pervade the industry any further than it already has.
Automation has been slowly making its way into the sector since the early 1990s and has contributed to debunking the idea that oil and gas professionals live a dangerous life – in fact, those working on offshore rigs now have a lower injury rate than teachers.
And yet, issues remain over whether or not automating jobs in the industry is going to exacerbate its skills crisis, which isn’t a myth and warrants serious attention, according to The Global Energy Talent Index (GETI).
Now, with the advent of an operational facility that runs without the aid of human input and relies entirely on technology in order to function, the world has a chance to assess the concrete facts.
Analysing the world’s first fully automated oil and gas platform
Equinor’s facility, called Oseberg Vestflanken H, cost the company more than £600m all told, though it was actually delivered in October 2018 20% under-budget.
Located 8km north-west of the Oseberg field centre in the North Sea, the platform’s build time was particularly expedient as it had no living quarter requirements.
“Oseberg Vestflanken H is the first platform of its kind on the Norwegian Continental Shelf with no facilities, not even a toilet,” said Anders Opedal, Equinor’s executive vice president for technology, projects and drilling.
“The topside weighs only a good 1,000 tonnes, another example of simplification in practice. This platform only has the bare essentials.”

Equinor claims Oseberg Vestflanken H will be capable of producing oil at a price below $20 (£16) a barrel for the next 22 years at a minimum.
It has a total predicted volume capacity of 110 million barrels of oil equivalent, and will extract the resource from deposits hundreds of metres below sea level, to be accessed by 11 wells.
Mr Opedal explained: “The fully automatic, unmanned and remote-operated platform is digitalisation in practice, and I am proud of Equinor and its partners for having chosen this in-house solution.
“Oseberg Vestflanken H is a pilot and our first unmanned platform. We are further developing the concept and believe that the next version will be even more competitive.”
Making the most of automation
One of the much-touted benefits of automation in any sector is its ability to remove human employees from harm’s way.
Rarely will any human personnel be on board Oseberg Vestflanken H, and it will be remotely managed from a control centre in the middle of the surrounding oil field.
Equinor spokesperson Eskil Eriksen told Offshore Technology: “The Oseberg Vestflanken H concept has been developed without compromising on safety – the platform is remotely controlled from the control room on Oseberg field centre 8km away.
“In case of incidents the control room will take necessary actions to ensure safety on the platform.
“This process is very similar to the operating of remotely operated subsea wells and installations done by the industry for decades.”

An area where automation has come under fire, however, is the implication that it will end up putting people out of work as autonomous technology and machinery gradually bolsters its case as a cheaper and more efficient business model.
A recent report by market analyst McKinsey suggested by 2030 between 75 million and 375 million people across the globe will be forced to alter their professional lives as a result of the increasingly ubiquitous trend.
For the moment, there remains little counter argument against this possibility, but from a business perspective, the many benefits of automation are easily extolled.
Peter Maier, co-president of industries at multinational software corporation SAP, said: “By 2050, the global population will approach ten billion people who need safe, reliable and sustainable energy.”
“In this complex energy market, the oil and gas industry is facing new challenges as it transitions to more efficient operations and lower carbon business models.
“Those in the sector understand that 80% of what they do is non-differentiating and they are looking for market-based standard solutions to automate these business functions.
“This allows the companies to focus on the 20% of their businesses that is differentiating and increase their efficiency.
“Automation technology can create efficiencies that make both environmental and financial sense as opportunities exist from the wellhead to the petrol pump, across the full oil and gas lifecycle.”