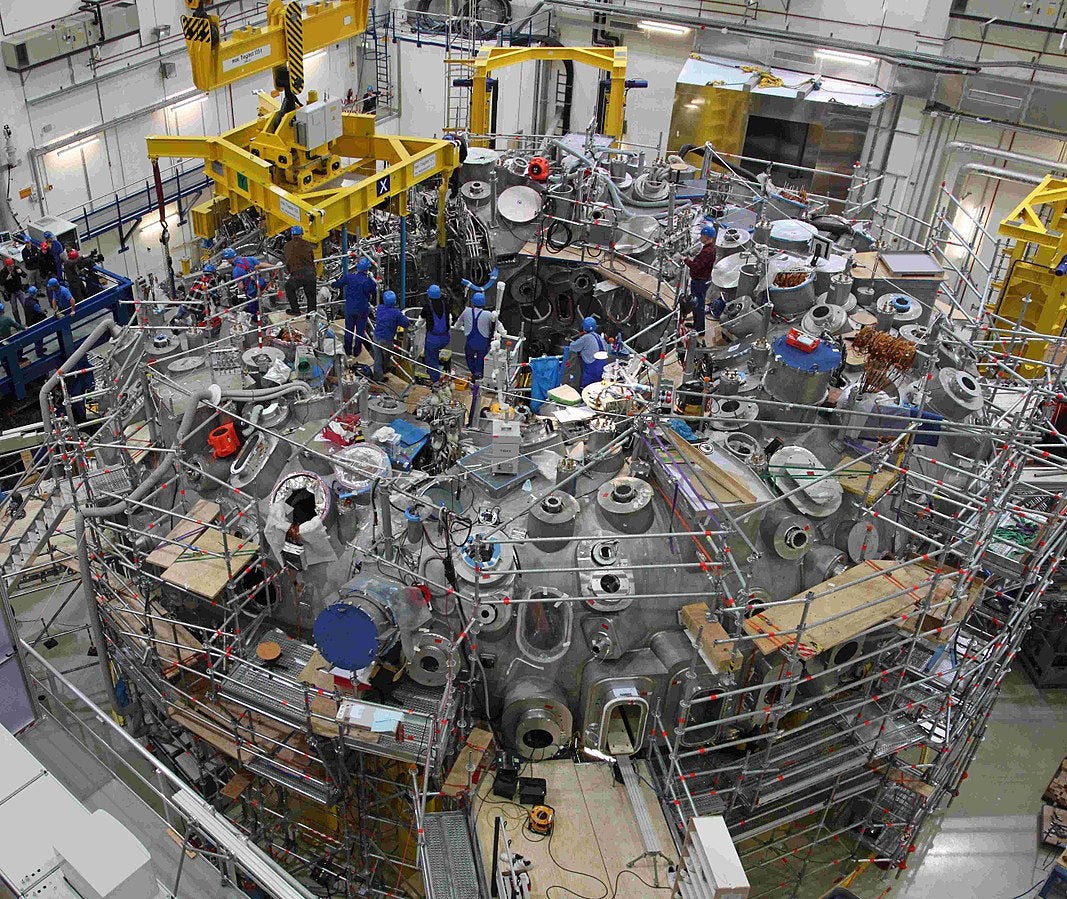
Fusion has been on the far horizon for so long, that the practicalities of it as an industrial-scale generation fleet have not been at the forefront of discussion. In January, when the International Energy Agency published its Energy Technology Perspectives report for 2023 – one that heralded a “new industrial age – the age of clean energy technology” and examined global supply chains for energy technologies and fuels – fusion was not mentioned at all in the 450-page report. That has to change if recent successes in the industry, in developing the fusion process and attracting private investors, are to be translated into fleets of fusion reactors rolled out in a timescale of years rather than multiple decades.
There are key development issues that have to be solved in stepping up from a developing technology to a commercial industry both within the technology envelope (such as the heat transfer and power generation ‘balance of plant’) and in the industry (such as developing the necessary supply chains and skills).
In comparison with other power generation types, nuclear’s fuel requirements are tiny, in terms of the volume of fuel required to produce terawatts of electrical energy. That does not mean they can be dismissed.
The fuel requirements for most nuclear fusion reactor designs are deuterium and tritium. Deuterium is naturally occurring. Concentrations of deuterium in water vary, but typically there is one deuterium atom for around 7000 hydrogen atoms. It can be distilled from water and it is routinely produced for scientific and industrial applications. Deuterium can also be stored for long periods.
Tritium presents a different challenge. Because its half-life is around 12 years it cannot be stockpiled. In fusion reactors, it is expected to be produced within the fusion reactor itself, ‘bred’ when neutrons escaping the plasma interact with the lithium blanket or wall surrounding the tokamak (in this nuclear reaction the lithium absorbs the neutron and splits into tritium and helium).
This means the fusion industry has to secure supplies of lithium that match its plans for growth. A 1000MW fusion reactor is said to require very small volumes of fuel in operation – around 125kg per year of deuterium and about the same weight as lithium.
The first catch: this represents the lithium and deuterium consumed during the year. The initial lithium blanket required at reactor start-up will be more of the order of 20 tonnes.
The second catch: only one isotope of lithium – Li-6 – produces heat during the nuclear reaction (2kg of Li-6 is required to produce 1kg of tritium) and the excess neutrons are required for both tritium production and heat transfer. The more abundant isotope, Li-7, which represents between 92% and 98% of naturally occurring lithium is not conducive to the reaction. It is not clear what proportion of Li-6 will be required in the lithium blanket but proportions in the literature vary upwards from 40%.
Furthermore, once it has been ‘bred’ the tritium gas has to be extracted from the lithium blanket and it is not clear what efficiency can be achieved in the capture and extraction process.
As the nuclear fission industry has found time and again, even small volumes of nuclear fuel rely on an extensive global supply chain to source, transport and process fuel, and that can mean bottlenecks that may represent major risks to the industry or the environmental damage that comes with resource extraction.
Lithium production
Lithium production is not free from environmental issues. It is produced in two ways. Some accumulations of saline groundwater are rich in dissolved lithium. It is also found in minerals hosted in pegmatites, rock units formed when mineral-rich magma intrudes from magma chambers into the Earth’s crust.
For the brine option, drilling at the site allows the brine to be pumped to the surface. It is kept in evaporation ponds for months or years until most of the liquid water content has been removed through evaporation, although this may be sped up with reverse osmosis. Extracting the lithium then requires several stages of purification, chemical separation of other by-products, filtration, and treatment to produce the product for sale, such as using sodium carbonate to produce lithium carbonate. Mineral deposits may have a higher lithium content but the material has to be mined and pulverised before the lithium can be extracted with chemical reagents that form a slurry that is heated, filtered, and concentrated through an evaporation process to form saleable lithium salts. The higher energy consumption, chemicals, and materials involved in extracting lithium from mineral ore mean typical lithium costs are twice those of brine extraction.
According to the US Geological Survey, four mineral operations in Australia, two brine operations each in Argentina and Chile, and two brine and one mineral operation in China accounted for the majority of global lithium production in 2021.
The IEA says anticipated capacity additions would lead supply in 2030 to be only slightly more diverse than it is now, mostly thanks to the start-up of mining in Canada. Australia and Chile will still account for around 70% of all mining once all those additions are fully operational. China has more than half of all capacity for refining lithium into specialised battery chemicals.
The separation of Li-6 from Li-7 presents another potential environmental issue.
The World Nuclear Association lists two options. Mercury-based separation relies on Li-6’s greater affinity to mercury. It says that when a lithium-mercury amalgam is mixed with lithium hydroxide, the Li-6 concentrates in the amalgam and the Li-7 in the hydroxide. A counter-flow of amalgam and hydroxide passes through cascades. This requires a lot of mercury and today this is undertaken only in Russia and China. The process is currently banned in the USA, where 11,000t of mercury was used in a previous process that involved significant losses to “wastes, spills and evaporation”. WNA says the alternatives are laser processes on metal vapour or chemical separation using crown ethers.
Meeting commercial needs
If the fusion industry is to be significant in meeting our electricity needs it will have to have not one 1000MW plant but hundreds or thousands.
The Statista website shows global lithium production hovered just above the 30,000-tonne mark during the early 2010s (up a third from the previous decade). Production began to step up in 2017 (when it was nearly 70,00o tonnes) and it was estimated at 100,000 tonnes in 2021. In its January report, IEA estimated global demand for lithium – almost entirely for electric vehicle batteries and motors – would be 700,000 tonnes per year by 2050.
If fusion reactors were to represent 5GW of supply by then – with five of the 1000MW units noted above – the industry’s annual lithium demand would be less than 1 tonne of Li-6 but up to twenty times as much unseparated lithium, along with 100 tonnes of start-up volumes. Extra would be required to ‘top up’ those figures after losses along the lithium conversion and tritium production and collection process.
That total remains a rounding error in the lithium industry. But the industry will aim to be larger than this: if it matches the current fission industry, with closer to 500GW of capacity, its demand for lithium will increase to the hundreds of tonnes – with the complexity that a large proportion of the lithium, in the form of discarded Li-7-rich material, can be offered back to the market.
This means that if the fusion industry is to play a significant part in meeting demand (including charging millions of electric vehicles) it will become a significant lithium customer.
One important point for the fusion industry is that its fuel supply marks a distinct difference from the uranium industry, where the nuclear industry is (almost) the only consumer. It places the fusion industry in a different position: being one of many customers offers protection if fusion development is slow or interrupted because lithium production will continue for other markets. But it also means fusion plant operators will have powerful competitors in securing necessary supplies of lithium.
In addition, the price of lithium may be volatile – it has risen in recent years in response to increased demand, but prices dropped again over the last year as abstraction companies responded to growing demand and higher prices by finding new resources.
The nascent fusion industry may have little market power to secure lithium at a low price – but should that be the industry’s aim?
At this point recycling lithium is in its infancy. The IEA raises the option of recycling lithium batteries but says this is difficult due to their complex composition. Pyrometallurgy – smelting the battery to separate its metals – is not currently adapted to recover lithium. An alternative method, cathode healing, requires battery components to be physically unpackaged, separated and recycled or reused. Under the US Infrastructure Investment and Jobs Act the Department of Energy has allocated $3bn in funding for battery manufacturing – largely new lithium sources such as Lilac Solutions production from low-concentration brine and recycling but also Cirba Solutions is developing a facility to recycle lithium-ion batteries.
It is likely that recycling EV batteries will become commonplace in future but behind them come different types of batteries or other uses where recovering the lithium is more difficult.
What does this offer for fusion? Even more than in the case of fission, fuel (lithium) cost will be a small part of the overall generation cost and processing is required to abstract the volume of Li-6 required. This suggests the industry can take the option to pay above-rock-bottom prices for its lithium. It could decide to pay a premium price to help develop lithium recycling facilities and fuel the fusion industry – possibly in its entirety – from lithium that would otherwise enter the waste stream. In fact, fusion’s requirement for lithium gives it an opportunity for a wholly beneficial story on the ‘fuel cycle front end’.
An industry that provides power from the sun – and fuels it from waste – would surely be the electricity industry of the future.
This article first appeared in Nuclear Engineering International magazine.