
While not yet a reality, the realisation of commercial fusion is drawing closer if the level of private investment in fusion technology is any guide.
According to the Global Fusion Industry in 2022 report from the Fusion Industry Association, investment in private fusion companies has more than doubled over the last year. Over the same period, eight new fusion companies have been founded, bringing the total to more than 30. As an indication of the growing investor confidence in the fusion sector, six companies have now each raised more than $200m. Reported highlights over the last year include the $1.8bn going to Commonwealth Fusion Systems and $500m earmarked for Helion Energy. Overall, private fusion companies have announced close to $5bn of collective funding, up some 140% on the 2021 figures, the FIA says. Private investment in fusion has now exceeded state-backed funding for the first time, although the International Thermonuclear Experimental Reactor (ITER) project remains a focus for much of the international effort.
Perhaps the world’s best-known fusion project, first plasma at ITER is now set to be pushed back again, this following the impact of the global pandemic and further technical difficulties. Although the revised schedule has not yet been established, by some estimates first plasma is not now expected until 2027. The current schedule envisaged first plasma in 2025 and the start of operations with deuterium-tritium fuel in 2035. The new timetable is to be finalised after the appointment of a new director general following the death of former Director-General Bernard Bigot. The Council has launched a process to select a successor DG and the new schedule is expected to be approved by the ITER Council in spring 2023.
Despite the delay, progress to complete the tokamak fusion device – under construction Saint-Paul-lès-Durance in southern France – is progressing. In May the first of nine sub-sections of the plasma chamber was lifted into the machine well. Weighing around 1,000 tonnes, the section forms one 40° arc of the vacuum vessel sector. It is fitted with silver-coated thermal shields, and two D-shaped toroidal field coils comprising vertical superconducting electromagnets. Eight other similar assemblies will form the complete chamber and toroidal field coil structure. Once complete, the vacuum vessel will be 19.4 metres across and 11.4 metres high. It will have an interior volume of 1,400 m³ and can contain 840 m³ of plasma, 10 times more than the current largest operating tokomak.
More recently, in July Japan’s Mitsubishi Heavy Industries Ltd (MHI) delivered testing equipment that is to confirm and demonstrate the safety of the Test Blanket Module (TBM) for ITER. The blanket is one of the components that comprises the inner wall of the fusion reactor. It is a critical component that extracts the heat generated by the reactor, as well as providing for the self-sustaining breeding of tritium used as fuel.
Designed to prove the feasibility of fusion technology, construction on ITER first began in 2010 and the initial first plasma was targeted for 2018. ITER is not expected to generate electricity and the unique 35-nation international project was widely expected to hit delays during its development. ITER is nonetheless more than 75% complete and over the last two components have continued to arrive at the site. Each member has completed first-of-a-kind components that have required engineering innovation in fields as diverse as materials science, electromagnetism, cryogenics and robotics.
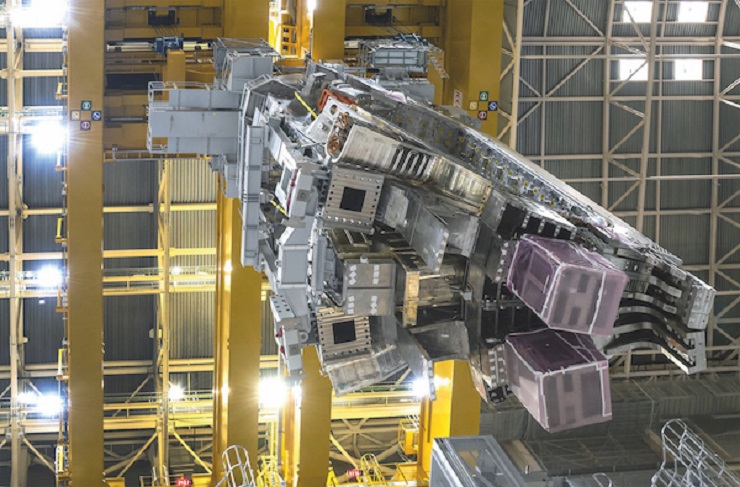
Beyond ITER
Looking to the next generation of fusion technology, the UK Atomic Energy Authority (UKAEA) has developed a laser-welding robot snake capable of operating inside the pipework of a fusion power plant. The patented DEMO snake will be remotely operated inside the hazardous environments within fusion reactors working in pipes with limited access. The project also required the development of an ultrasonic sensor-system to identify each precise working location as the snake moves through the pipework.
The £2.7m (US$2.5m), seven-year project came under UKAEA’s Remote Applications in Challenging Environments programme (RACE) as part of EUROfusion’s DEMO fusion programme. This is expected to be successor to the ITER project. “In fusion machines, pipework has to be connected and disconnected remotely because of the hazardous environment. Pipework in DEMO is extra challenging because of the limited working space,” explained Tristan Tremethick, Lead Mechanical Design Engineer at UKAEA.
“Robots are a key part of our mission to deliver low carbon fusion energy, and we need to become skilled in controlling machines like this one remotely. That’s because they will be used to maintain fusion energy power plants. We won’t be able to send people in, robots will keep them running – it’s the future,” Tremethick added.
RACE has also developed a laser cutting tool operating on the same principles as the welding snake.
Elsewhere in the UK, Cerberus Nuclear and Assystem are developing the in-board shield design for the Spherical Tokamak for Energy Production (STEP) reactor, the UKAEA’s prototype fusion plant.
The project concerns the extreme environment within the central column of the STEP fusion reactor where temperatures can range from over 100 million oC in the plasma to below -200oC in the superconducting magnet cryogenic system over the space of just a few metres.
Cerberus Nuclear and Assystem are to develop radiation shielding and cooling strategies within the in-board shield section of the central column to protect the sensitive toroidal magnets. Cerberus aims to optimise the shielding in order to maximise the operational life of these components.
A concept reactor design is anticipated by 2024 with first operations expected in the early 2040s. A site is due to be selected this year from five shortlisted locations across the UK.
Systems, engineering and technology consultancy, Frazer-Nash has undertaken a viability study for the UKAEA into a hydrogen isotopic separation technique, also as part of the STEP programme.
The viability and optioneering study will explore a technique known as a Thermal Cycle Absorption Process (TCAP) for separating and recycling protium, deuterium and tritium.
Japan’s Kyoto Fusioneering Ltd has also completed the preliminary design of an integrated testing facility for testing power generation systems for fusion reactors. The Unique Integrated Testing Facility (UNITY) will test both the heat extraction and fuel cycle systems, allowing companies to focus resources on fusion power core development. UNITY is to be equipped with a test blanket module, primary cooling loops with both liquid metal and molten salt, heat exchangers, a tritium recovery system, and an electricity generator. They will be integrated with a test diverter module, tritium pumps, and a tritium fuel circulation system. These components are not only be required for the DEMO-type plant, which will follow ITER, but are also needed for power plant designs being developed in the private sector.
Construction is due to start in Japan around August with the testing loop scheduled to be completed by March 2023. Full UNITY construction and the subsequent demonstration of electricity generation is planned by the end of 2025.
A number of novel fusion reactor developments have also taken place recently.
Fusion breakthroughs
The UK Atomic Energy Authority (UKAEA) has independently validated that First Light Fusion has achieved fusion. This is the first time that fusion has been achieved using the unique targets developed by First Light.
First Light aims to solve the problem of fusion power with the simplest machine possible and its projectile technology. Projectile fusion is a new approach to inertial fusion that is simpler, more energy efficient, and has lower physics risk, First Light says.
Instead of using complex and expensive lasers or magnets to generate or maintain the conditions needed for fusion, First Light used its two-stage hyper-velocity gas gun to launch a projectile at a target containing the fusion fuel.
First Light’s key technology is the target design, which focuses the energy of the projectile, imploding the fuel to the temperatures and densities needed to make fusion happen.
“The projectile reached a speed of 6.5 km per second before impact. First Light’s highly sophisticated target focuses this impact, with the fuel accelerated to over 70 km per second as it implodes, an increase in velocity achieved through our proprietary advanced target design, making it the fastest moving object on earth at that point,” First Light explained in a statement.
First Light’s power plant design involves the target being dropped into the reaction chamber and the projectile launched downwards through the same entrance, so it catches up with and impacts the target at the right moment and a pulse of fusion energy is released. That energy is absorbed by lithium flowing inside the chamber, heating it up. The flowing liquid protects the chamber from the huge energy release, sidestepping some of the most difficult engineering issues in other approaches to fusion. Finally, a heat exchanger transfers the heat of the lithium to water and a conventional steam cycle to generate electricity.
UKAEA was invited to analyse and validate First Light’s fusion results before they were made public and confirmed that there is evidence First Light has produced neutrons consistent with those produced from the fusion of deuterium fuel.
With its relatively simple equipment, built in large part from readily available components, the University of Oxford spin-out achieved fusion having spent less than £45m (US$58.5m). First Light also claims a rate of performance improvement faster than any other fusion scheme in history. A peer reviewed analysis conducted by First Light shows that projectile fusion offers a pathway to a very competitive Levelised Cost Of Energy (LCOE) of under $50/MWh, directly competing on cost with renewables.
Plans for a “gain” experiment – in which more energy is generated than is put in – are advancing. First Light expects to partner with existing power producers to develop a roughly 150 MWe pilot plant costing less than US$1bn in the 2030s. The company is already working with UBS Investment Bank to explore strategic options for the next phase of its scientific and commercial development.
Meanwhile, Australia’s first fusion energy company, HB11 Energy, said it had “demonstrated a world-first ‘material’ number of fusion reactions by a private company, producing ten times more fusion reactions than expected based on earlier experiments at the same facility”. HB11 Energy’s results were published in the peer-reviewed scientific journal, Applied Sciences, and demonstrate non-thermal fusion of hydrogen and boron-11 using high-power lasers. This approach differs radically from most other fusion efforts to date that require heating of hydrogen isotopes to millions of degrees, the company noted.
HB11 Energy’s research demonstrated that its hydrogen-boron energy technology is now four orders of magnitude away from achieving net energy gain when catalysed by a laser.
The project was performed at the LFEX petawatt laser facility at Osaka University in Japan as there is no high-power laser facility in Australia.
Commenting on the development Dr Warren McKenzie, co-founder and managing director of HB11 Energy, said: “Our unique approach to large-scale clean electricity generation uses an aneutronic fusion reaction between hydrogen and boron-11 that does not use any radioactive fuels or generate uncontrollable radioactive waste. Achieving this on a large scale would be a game-changer, but to do this locally we will need significant investment in our sovereign capability, including having a petawatt laser in Australia.”
HB11 Energy claims it is now the global frontrunner in the race to commercialise fusion. Its results came just before the National Ignition Facility (NIF) at the US Lawrence Livermore National Laboratory also demonstrated laser-driven fusion.
These developments are a strong indication not just of growing confidence in the fusion industry, but also the likelihood of commercial fusion becoming reality well within the moving 50-year window of long-standing repute.
According to an FIA survey of people working in private fusion companies, more than 90% believe fusion power will be supplying the grid by the 2030s and over 80% think fusion will be considered commercially viable in a similar timeframe.
As Andrew Holland, Chief Executive Officer of the Fusion Industry Association, says in the report: “Fusion is on a pathway towards commercial relevance, at a time when the world desperately needs new clean energy options. With investment accelerating, it is increasingly likely that commercial fusion will become a reality within the next two decades, providing the basis for prosperity, safety, and security for many years to come”.
This article first appeared in Nuclear Engineering International magazine.