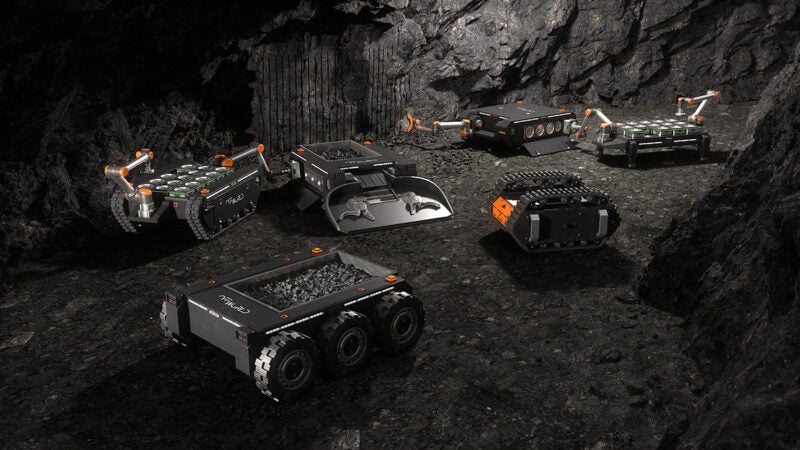
Miners have always relied on collaboration. You can glimpse it in a hundred ways, from union solidarity to the importance of teamwork in emergencies. In 2010, to give one example, the 33 miners saved from a collapse in Chile only survived thanks to spectacular cross-industry support, with engineers, geologists, drilling specialists and other experts all lending a hand. You can even see it in music, in the old mining songs once sung in collieries from Durham to West Virginia. “My daddy was a miner, he’s now in the air and sun,” goes one of the most moving, composed in 1931 and later immortalised by Pete Seeger. “He’ll be with you fellow workers, until the battle’s won.”
Now, imagine a mine just as steeped in fellowship as the pits of old – but remove the actual miners from the scene. When you first hear it, this simply sounds impossible. But if you speak to insiders, you may be convinced otherwise. After all, they’re building a world where human labourers are replaced by robots, drones that can learn, adapt and cooperate just as effectively as their flesh-and-blood forebears. The consequences here, it goes without saying, are truly revolutionary, with so-called ‘swarm robotic mining’ potentially offering safe, sustainable operations everywhere from extraction to collection to hauling.
Yet, if MarketsandMarkets has found that swarm robotic mining could become a $3bn sector by 2028, up from less than $1bn today, success clearly requires more than unleashing a gaggle of devices and hoping for the best. For one thing, getting the machines just to function as individuals involves a fiendish mix of algorithms and training regimens, even as collective action requires even more complicated technology. There are other difficulties here too, from adapting to breakdowns to understanding the ideal number of robots on a single site. And hovering over it all is an appreciation, even among automation fanatics, that actual people can’t be removed from the mining landscape completely – even if machines can bring it pretty close.
A new swarm
Automation is everywhere in contemporary mining. Quite aside from the headline figures, with the sector predicted to enjoy CAGR of over 6% through 2027, this transformation can be glimpsed up and down the supply chain. Yet, if teleoperated bulldozers in Chile compete for attention with robotic clean-up machines in Utah, Dr Jekan Thanga sees these practical achievements as anchored in technology. From the constant miniaturisation of electronics to exponential performance bumps epitomised by Moore’s law, the associate professor of aerospace and mechanical engineering at the University of Arizona argues that scientific advances are “fundamental” to understanding this burgeoning field.
With this in mind, it makes sense that operators are increasingly excited about advances in fully automated vehicles – machines that can exploit the latest AI advances to drill or haul totally independently. And if single devices are impressive enough here – especially since sending humans down a mineshaft can be dangerous and expensive – swarm robotic mining is even more striking. Plausibly encompassing dozens of robots, trained to function both independently and as a team, they’re already being trialled by experts across the planet.
One prominent example here is Anglo-American, which has been investigating swarm robots since around 2018. Another is OffWorld. Headquartered in a Los Angeles suburb, Jim Keravala, the firm’s co-founder and CEO, says his company were the “originators” of the whole concept. And like the spread of automation more broadly, Keravala argues technology is the driving force. As he phrases it: “The unique value proposition of swarm intelligence and heterogeneous swarm intelligence – with fully autonomous, rugged, robust robots – is a paradigm shift for mining opportunities here on earth.”
Such enthusiasm isn’t hard to understand when you consider how these machines might one day be employed. Both Keravala and Thanga compare them with ant colonies, with individuals going about their business, but in support of a greater mission. To that end, OffWorld has already developed a range of specialised machines, each fulfilling a specific industry role. Looking like a cross between a robotic vacuum and a First World War tank, OffWorld’s excavators are equipped with a saw and a drill. Collectors, moreover, have the appearance of snowploughs, whereas haulers have a deep cavity for ore or rubble. The point, at any rate, is that each model can seamlessly interact, without any human guidance, with excavators passing material to collectors, which can then scoop it into haulers.
Mining intelligence
How is this automated ant farm achieved in practice? As so often, technology is key. In the first place, each of OffWorld’s machines is what Keravala calls an ‘edge’ server. Dispensing with the need for remote servers, and the necessity to shuttle data to and fro, this system allows machines to make decisions much faster. That’s obviously helpful in a crowded mining environment, particularly when you factor in the other robots zipping about the place. In a similar vein, Thanga says that a decentralised approach allows machines to not only communicate intelligently with their environment, but also with each other. Trained on a specific set of rules, like the need to avoid collisions with other robots, the professor explains that swarm robots are otherwise given free rein to come up with “creative behaviours” to problems. Machine learning is now becoming so powerful, in fact, that Thanga and his colleagues have actually witnessed robots mimic insects for real, for instance spontaneously forming “bucket brigades” in much the same way that ants carry food back to base.
To put it differently, swarm robots can not only work effectively together – they can also learn to deepen their relationships in real-time. If, to give one hypothetical example, a gang of surveying robots use ground-penetrating radars and other sensors to map an open pit copper mine, the information they gather can then automatically be transmitted to excavators, in turn informing how they approach drilling. Nor are these big-picture ideas the only places where this technology excels. Using laparoscopy, the same precision technique used in certain types of surgery, OffWorld’s excavator robots can target the metal ore they need, rather than smashing a rock face up wholesale. Beyond saving time and money, this focused approach can have positive environmental consequences too. “It’s selective mining,” is how Keravala phrases it, noting that excavating with the swarm avoids the need for either hydrocarbons or “drill and blast” tactics – both techniques that have helped turn mining into one of the most polluting industries on the planet.
Not, of course, that any of this is easy. For starters, Thanga describes the difficulty of giving robots flexibility on the one hand, and ensuring they don’t go rogue – and fail to complete their tasks. Deciding exactly how many robots a particular project requires has proved tricky too. “Too many cooks spoil the soup,” is how Thanga puts it, noting that there’s always a risk machines end up spending more time negotiating traffic jams than they do hewing rock. A broader challenge involves proving to operators that these complex devices can really bolster operations in practice. At the same time, Thanga says that swarms must meet the “safety requisites” expected of them. To be fair, there are signs that the sector is progressing at speed. “We’re looking to first deployments in the 2025 period,” Keravala says, adding that OffWorld’s surveyor robots are even further advanced.
Man maids
Speak to the experts, meanwhile, and there are hints that swarm robots could yet achieve even more remarkable collaboration. If Thanga’s bucket brigades are one example here, the professor invokes another image to describe what mining machines might one day manage. If Roman legionaries joined their shields into the famous tortoise formation, bunching close together before marching ahead as a single unit, Thanga has seen drones do something similar. That could be particularly useful for drilling operations – an activity predicated on power and consistency – not least when a cluster of robots all moving in the same direction could push forward even devices that have failed.
All the same, it’d be wrong to envisage a future where robots buzz about without any interference. Especially in hazardous mines, a flesh-and-blood intelligence needs to ensure that their robot allies don’t get too confused – and manually intervene if they do. For his part, Keravala foresees people only needing to be at the surface of underground mines. “We’re much more about humans on the loop – rather than humans in the loop,” he explains, suggesting that their role will involve “anomaly management” rather than the direct “curation” of devices. It seems clear, in other words, that Pete Seeger’s talk of comradeship won’t vanish entirely, even if the sector’s conception of the term may ultimately need to expand.
This article first appeared in World Mining Frontiers magazine.