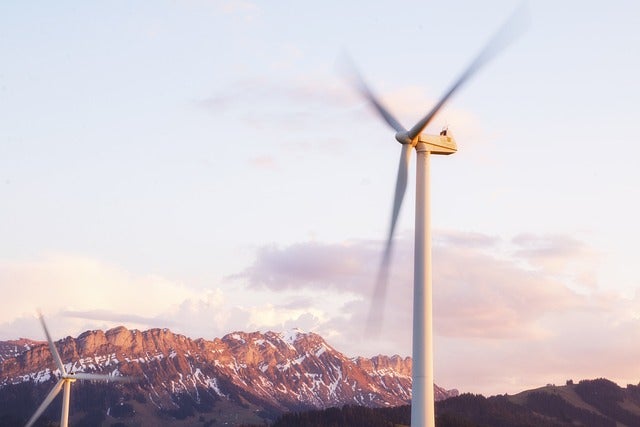
Construction has always been a difficult and dangerous business, which is why we’ve always pushed the envelope in designing and developing technology to make it faster, easier and safer. Take the crane, for example. While the earliest cranes date back to Mesopotamia – or modern Iraq – around 3,000 BC, these were used to transport water for irrigation – the earliest cranes designed for lifting heavy loads were developed by the Ancient Greeks in the late 6th century BC.
From there, the technology grew ever-more advanced and efficient, going from making use of weights to treadwheels to hydraulics, and then right into the modern age. They’ve had to develop and become more complex, of course, as the demands on construction abilities have grown too – humanity now builds vast and complicated structures on high mountains and far out at sea, with no sign of slowing down. It’s apt, then, that the word “crane” stems from its resemblance to the long neck of a bird, as one Austrian company looks to iterate on the traditional form of a crane – by having it take flight.
A flying start
Founded in 2017, the Ventus Group offers a range of services to optimise the performance of wind farms around the world by reducing risk, maintenance and repair costs, as well as extension of wind turbines. It is a leading provider of end-to-end optimisation solutions for wind turbine performance, with turbine rotor efficiency as its primary focus, as damaged or poorly aligned turbine blades are the most common cause for underperformance. In 2018, the company received funding from the Austrian Research Promotion Agency (FFG) – the national funding agency for industrial research and development – to patent its rotor monitoring technology, consisting of its proprietary sensor nodes, algorithms, software and so on, which was commercially launched at the end of September 2022.
Ventus’ work here in the wind energy sector, and its subsequent conversations with original equipment manufacturers (OEMs), led the company to begin development of a flying heavy-lifting crane capable of transporting tools or spare parts from an onshore site to an offshore service vessel or substation. This crane would also be used to transport tools up to the surface of turbine blades in order to carry out repair work, and then transported safely back to the ground.
Traditional cranes present a number of challenges for the wind energy industry, which typically builds its turbines in hard-to-reach areas with the highest wind speeds – whether that’s out at sea or up on a mountainside. However, even building in more reachable areas presents challenges of its own. “Many countries in Europe are defined as ‘low-wind areas’,” explains Shavkat Mingaliev, CEO of Ventus Group. “In order to capture the wind, you need to build taller towers – and the higher you go up, the more prohibitive are the crane costs.”
His OEM contacts in the wind industry were clear that – to a certain height – they were happy to continue working with traditional cranes, but beyond that point the option of a flying crane was increasingly alluring. Seeing the potential in such a project, Ventus Group teamed up with Unmanned Helicopters, a helicopter drone manufacturer, in October 2021 to develop a heavy-lifting solution.
This ultimately resulted in the UH-200-Beyond-M helicopter drone, which Ventus demonstrated at a tech demo it hosted just outside Warsaw, Poland, back in February, to more than 50 members of the press and industry. Converted from a CH7 Kompress, a small-to-mid Italian helicopter intended primarily for sport use, the UH-200-Beyond-M can carry a payload of up to 230kg, with a four-stroke engine, a maximum speed of 200km/h and a cruising speed of 160km/h.
The drone also boasts an altitude ceiling of 10,000ft and a control radius of 32km over radio link – or an unlimited control distance within a GSM, 5G or LTE network range. Similarly, since this drone was designed to operate both offshore and in mountainous areas, it is also designed to be rugged and reliable, capable of operating across a temperature range of -30°C–+45°C, a maximum wind speed of 15m/s and precipitation of up to 1mm/h.
The helicopter model, with its one main rotor and a smaller tail rotor, stands out against much of the drone offerings on market, which typically consist of multirotor models. Ventus’s decision here was no accident, however – as Mingaliev notes, this form is best suited to the tasks it’s intended for. “Helicopter technology has been in existence for over 130 years now,” he adds. “[On the other hand,] conventional multicopter – multi-rotor – drones have issues with energy efficiency. For example, at higher wind speeds, they need to deploy all their motors in order to hover in a given position, whereas a helicopter flies better when there is wind.”
This can make helicopter drones superior to their multicopter brethren for certain use cases, particularly as companies look towards building fully electric drones, where battery life and energy efficiency is all-important. The UH-200-Beyond-M uses conventional gasoline, but it can also run on sustainable aviation fuel. “We know that there is a tendency in the wind turbine industry, because of the renewable nature of the business, to go for environmentally friendly types of fuel,” Mingaliev notes. “Sustainable aviation fuels can have the same qualities as gasoline, with small adjustments.”
A little drone goes a long way
Ventus and Unmanned Helicopters have also designed a fully electric small helicopter drone, the UH-7- Beyond-S, which has a payload capacity of up to 7–12kg depending on the version – the cargo model offering the full 12kg. It boasts a particular advantage when it comes to licensing, as even with its payload capacity the maximum take-off weight of the drone remains under 25kg, meaning it falls under the ‘open’ category for leisure drone activities and low-risk commercial activities – specifically the A3 sub-category.
This requires the drone not to fly near or over people and to keep at least 150m away from residential, commercial or industrial areas, while also requiring operators to have passed the necessary training and examinations defined by their national competent authority. These restrictions are minimal, all things considered, making the UH-7-Beyond-S perfect for its intended purpose.
“In many instances, you don’t even need [the operational licence], unless you are flying beyond visual line of sight (BVLOS),” Mingaliev adds. On this note, Unmanned Helicopters obtained a licence from the Polish Civil Aviation Authority in March for the BVLOS flying of the UH-7-Beyond-S, which is valid for two years – which Mingaliev expects will simplify the process of obtaining permits to fly BVLOS in other EU countries as well.
Another advantage that this small drone possesses is that due to the energy efficiency of helicopter drones, its endurance far surpasses multirotor models. “A good-quality industrial drone, with a payload, can perhaps fly between 30–45 minutes,” says Mingaliev. “With the same type of payload, our helicopter drone can fly up to two hours. So, we have the endurance that is two times longer than any other competitor that we know of today.”
Similarly, as these drones can be outfitted with different tools and cameras depending on the task at hand, it makes them adaptable for a wide variety of situations. Ventus’ principal offering, its dynamic blade pitch angle measurement service, has excelled at onshore sites – in 2022, however, the company took the UH-7-Beyond-S and integrated its highspeed camera, and now offers its dynamic blade pitch service commercially offshore as well. This is hugely useful for the owners of wind farms, as blade pitch angles can have a huge impact on the efficiency of a turbine, enabling operators to adjust or correct any low-performing turbines.
“For the small helicopter, the sky’s the limit – for example, you can use it for the benefit of telecom companies to inspect the antennas or to deliver spares to these antennas,” Mingaliev adds. The UH-7- Beyond-S is particularly suited to this challenge, as many commercial drones fail at this task due to the very strong electromagnetic emissions at play. Ventus’s more rugged and reliable model, on the other hand, will better be able to weather this obstacle.
The UH-7-Beyond-S is also currently being used for powerline inspection in different countries, and Ventus are engaged with different oil and gas companies, where it is demonstrating the drone’s ability to transport different types of tools between remote settlements, such as offshore islands or hydrogen hubs built alongside offshore wind farms.
Beyond this, the small helicopter drone can be used to inspect different kinds of infrastructure – such as bridges, high-rise buildings and water towers, the latter of which Ventus recently completed a pilot project for in the Netherlands. Similarly, powerline inspections and even use at ski resorts, examining the technical condition of ski lifts.
A pioneering spirit
From there, now that it has successfully demonstrated its ability to convert a 230kg payload-carrying helicopter into an unmanned aerial system, Ventus is in talks with customers from civilian and military sectors looking to see if the same could be done for even larger helicopter models.
“In the near future, we will probably see the UH-500- Beyond-L – a larger version,” Mingaliev notes. “We have small, medium and there will be L and perhaps an XL.” While many companies are working on heavy-lifting drones in some form or another, he feels confident that Ventus and Unmanned Helicopters remain a several steps ahead of the competition. “The feedback we are receiving from existing and potential customers is that we are one of the very few who not only claim [to have] this capability, but we can actually fly the drone with the payload and for the customer, today.”
Of course, these heavy-lifting drones are only the latest additions to Ventus’s array of products. For years, the company have been operating multicopter drones for offshore wind turbine blade inspection, with framework agreements in place with offshore wind turbine owners. Currently, the company have plans to in place to take their expertise with multicopter and helicopter drones and establish a separate subsidiary called Ventus Aero, which it will use to push its drone offerings even further.
“We genuinely believe we can pioneer the heavy lifting delivery of different spares or tools for both onshore and offshore customers from the wind industry,” says Mingaliev, reiterating that the technology offers great potential beyond the wind industry as well, with the construction sector next up in Ventus’s sights, where health and safety concerns encourage automation where possible.
“Everything is going towards autonomous flying – towards the greater need for drones and the greater ways to deploy to deploy drones,” he concludes. “Ventus Aero will be created as an operator of different types of drones for the wind industry to begin with, and then the construction and telecom industries, or supplying remote settlements in Europe and Asia with certain supplies, especially in mountainous areas. We believe that there are many different use cases for our drones.”
One thing is for sure – technology will always continue to develop, to iterate, to adapt. Ventus’s drones are just the latest in a long line of advancements in heavy lifting technology, from the simple cranes of the ancient Greeks and now to the sky above. The only question that remains is how far this flight will take them.
This article first appeared in World Wind Technology magazine.