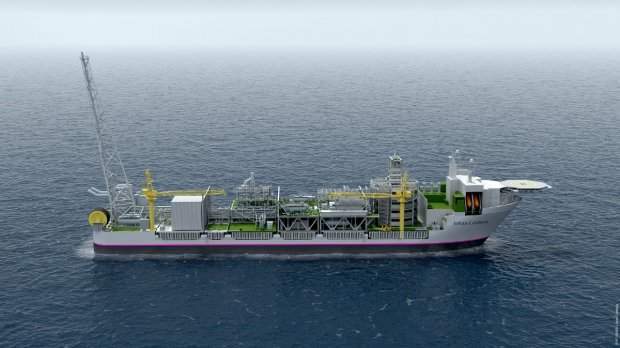
Under its contract, the GE company will deliver turbomachinery equipment for the topside structure for the floating production, storage and offloading vessel (FPSO) to be associated with the offshore oil project.
The equipment to be supplied includes two gas turbine generators with LM2500+ G4 Dry Low Emission with Dual Fuel capability direct coupled with two poles electric generators.
BHGE said that each of the gas turbine generator train will comprise a waste heat recovery unit on its exhaust system. This unit will enable energy of the turbine fumes to be recovered for maximizing efficiency.
BHGE will also supply balance of plant (BOP) auxiliaries associated with the gas turbines and the waste recovery units.
The GE company plans to test and preassemble the equipment into three industrial modules at its turbomachinery and process solutions facilities in Massa and Avenza in Italy. The modules shipment is scheduled to be made in the fourth quarter of 2019, said BHGE.
BHGE turbomachinery & process solutions director Paolo Ruggeri said: “The modularization of the units that we can execute in our Avenza module construction yard represents an innovative solution that we were able to offer to Statoil during the initial phase of the design.
“It will allow a significant reduction in the number of interfaces and activities to be performed by the customer at site and at the FPSO construction yard.”
In February, Statoil had given contracts to Kværner and Siemens related to the FPSO vessel to be deployed in the Johan Castberg field.
Kværner, under a $481.3m contract will build and install the topside modules for the vessel. Aker Solutions, as a subcontractor of Kvaerner holds a contract to deliver two modules for water and chemical injection for the offshore oil project.
On the other hand, Siemens will engineer, manufacture and commission the SGT-750 gas turbine-driven compression train of the Johan Castberg FPSO vessel.